The construction of Line 3 is progressing satisfactorily
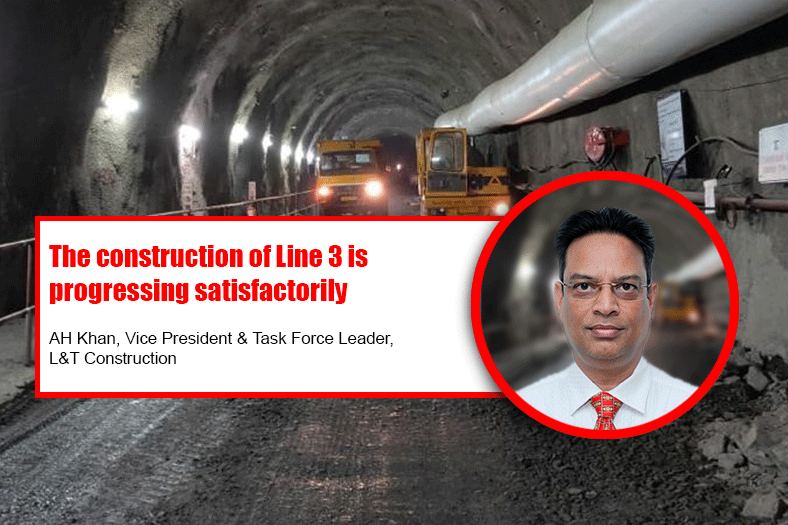
Larsen & Toubro is employing a wide range of technologies to improve operational efficiencies at the Metro 3 project says AH Khan, Vice President & Task Force Leader, L&T Construction.
What is the scope of work involved in the project?
Larsen & Toubro is involved in two crucial packages of the Mumbai Metro 3: UGC 01 and UGC 07. Package UGC 01 is in South Mumbai and the scope includes the construction of four stations at Cuffe Parade, Vidhan Bhavan, Churchgate and Hutatma Chowk and associated tunnels. The tunnel boring (twin tunnel) commences at the north end of the Cuffe Parade Station and terminates at the CSMT Metro Station. The Cuffe Parade Station accommodates a cross-over and stabling area. The scope also includes MEP & architectural works.
Package UGC 07, located near the country’s second busiest airport, the scope includes the construction of three stations at Marol Naka, MIDC and SEEPZ and associated tunnels. Three TBMs (Tunnel Boring Machines) are being used in this package, launched from two locations: two from Midshaft near Pali Ground and one from ramp area near the depot. The scope also includes MEP & architectural works.
Can you tell us about the work completed and the deadlines involved?
The construction of Line 3 is progressing satisfactorily. For both the packages, the station box excavation and a major amount of work on the slab station boxes have been completed. While the tunneling involved in Package UGC 07 is over, that for UGC 01 is in advance stage with more than 50 per cent completed.
Metro 3 is also using the New Austrian Tunnelling Method (NATM) which is proceeding at a steady pace and about 40 per cent of the work has been completed.
What are some of the core challenges your firm has had to address on-site?
Each project has its own special set of challenges and UGC-01 and UGC-07 are no exception. Apart from being located in the middle of one of the most expensive residential areas in the world – in fact, in some cases the excavations are within 2 m of some heritage structures, the project team faces other challenges like testing ground conditions, limited working space, underground perils, statutory requirements, taxing logistics, and many more. These challenges are being overcome by meticulous planning & monitoring, engineered solutions and, a few times, by nimble footed thinking.
Experts have been deployed, not only from core construction sectors but also for tunneling, blasting work, resolving technical issues, traffic management, structural stability, utility diversion etc.
The project team has been able to overcome these hurdles, innovating noise mitigation modifications for piling, erecting noise barriers, developing harmonious relations with ‘neighbours’, and maintaining excellent communication with all stakeholder
What kind of technology and specific machines are being utilized to accomplish this project?
The construction of stations involves excavating hard rock exceeding at times 120MPa, going as deep as 30 m in some places. Tunnels pass through varying strata – hard, soft as well as mixed face rock. The tunneling is carried out with TBMs. The opening ratios, position of screw conveyor, mucking methods, etc are taken into account before selecting a Rock Mode / Earth Pressure Balancing Mode Single shield XRE Series Crossover TBM, which can bore through the hardest rock, handle maximum water ingress, manage sinkholes and bore through a mixed face.
NATM has also been adopted for locations where TBM tunneling is not feasible. In such cases, the emphasis has been laid on minimum obstruction during blasting. Real-time vibration, tilt and geospatial monitoring has been prescribed for heritage buildings. The equipment deployed are Single and Double Boom Jumbo, Shotcrete machines, etc.
The Cross – Passage works are being executed with the Drill and Blast method. With the growing adoption of digital solutions to improve efficiencies, this project has adopted several of them including RFID, BIM (Building Information Modelling), training workers Virtual Reality and the like.
What strategies do you have in place to ensure reliability, sustainability and energy efficiency in this project?
As one of the world’s foremost engineering and construction conglomerates, Larsen & Toubro is employing a wide range of technologies and lean construction techniques to improve operation efficiencies at the Metro 3 project. Efficient project management and planning, tracking of men, materials and equipment, better training have all helped to accelerate the speed, reliability and sustainability of construction, improved quality and safety and, at the same time, saved precious man hours, environment and cost.
Cookie Consent
We use cookies to personalize your experience. By continuing to visit this website you agree to our Terms & Conditions, Privacy Policy and Cookie Policy.