Acclimatisation and moisture assessment, the key to laminate performance
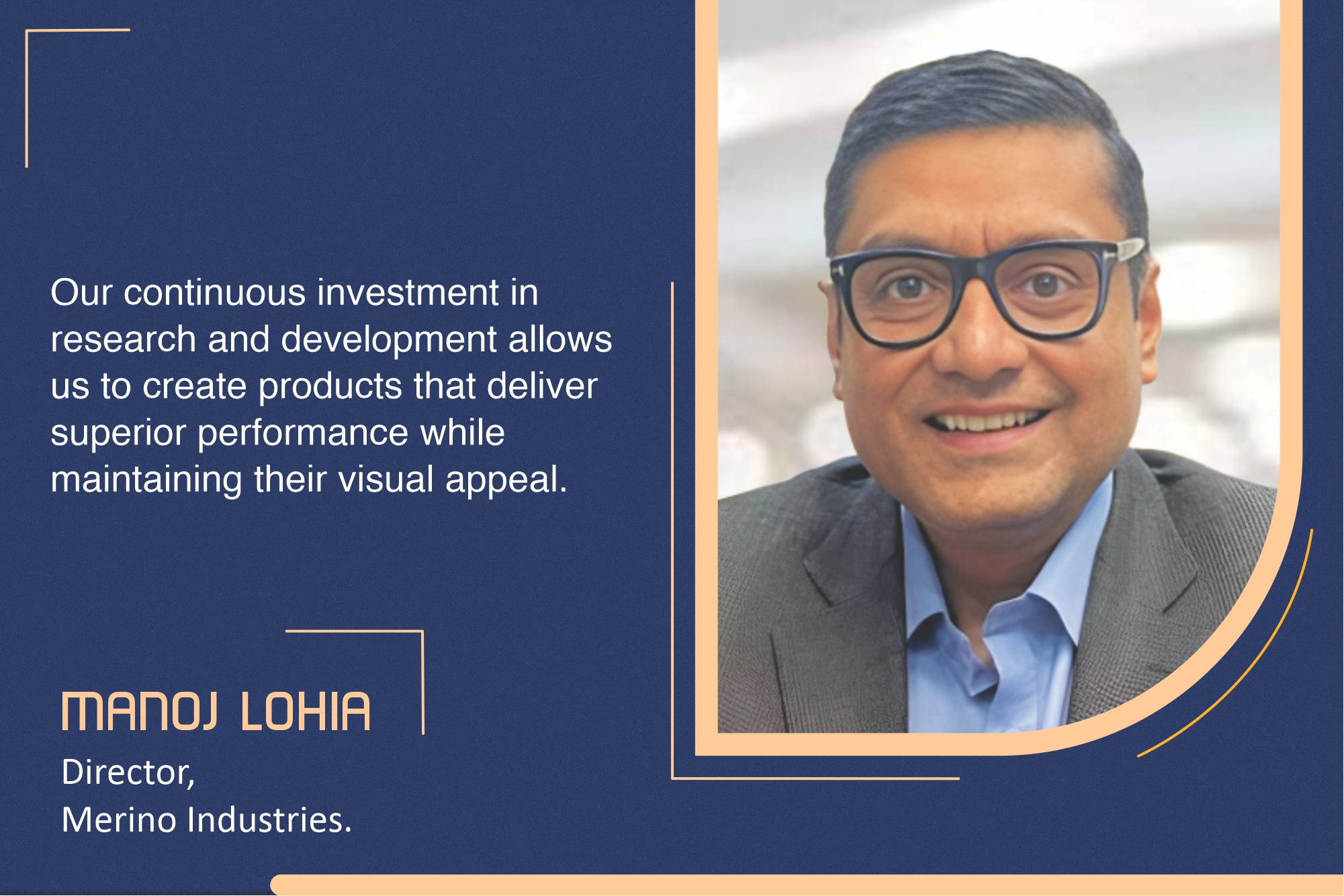
Manoj Lohia shares his insights on the laminate solutions offered by Merino Industries, the international certifications they comply with, and how they are tailored to different applications. Manoj also emphasises the importance of acclimatisation and moisture assessment for enhanced laminate performance.
How are your laminate solutions tailored for different applications?
We offer various laminate solutions, from general-purpose to fire-retardant and chemical-resistant laminates. The general-purpose laminates are preferred for furniture, wall panelling, doors, and cabinetry. Laminate solutions used in airports, hospitals, and hospitality spaces are of FR+ fire-retardant grade, halogen-free, and comply with stringent fire safety standards. Our chemical-resistant Chem+ laminate solutions are designed for laboratories and industrial environments. These laminates meet SEFA 3 standards and can withstand harsh chemical interactions without compromising durability.
Please explain the testing methods you adopt to ensure the performance (wet weather, structural integrity, fire resistance, etc.) of your laminates.
We adhere to internationally recognised testing methodologies, ensuring that our products meet and exceed industry standards. Our FR+ fire-retardant laminates are subjected to rigorous testing at Warrington Fire Laboratory, UK, as per BS-476 standards, for Class-I fire rating, which significantly limits flame spread. The fire behaviour of our products is assessed through their compliance with the ASTM E-84 standards. Our Chem+ laminates, designed to provide high resistance to chemicals, are evaluated under the SEFA 3 standards, where the products are subjected to a 24-h chemical spot test to ensure resilience against acids, alkalis, and solvents. Our laminates are tested under varying temperature and humidity conditions for stability, ensuring they do not warp, crack, or degrade over time.
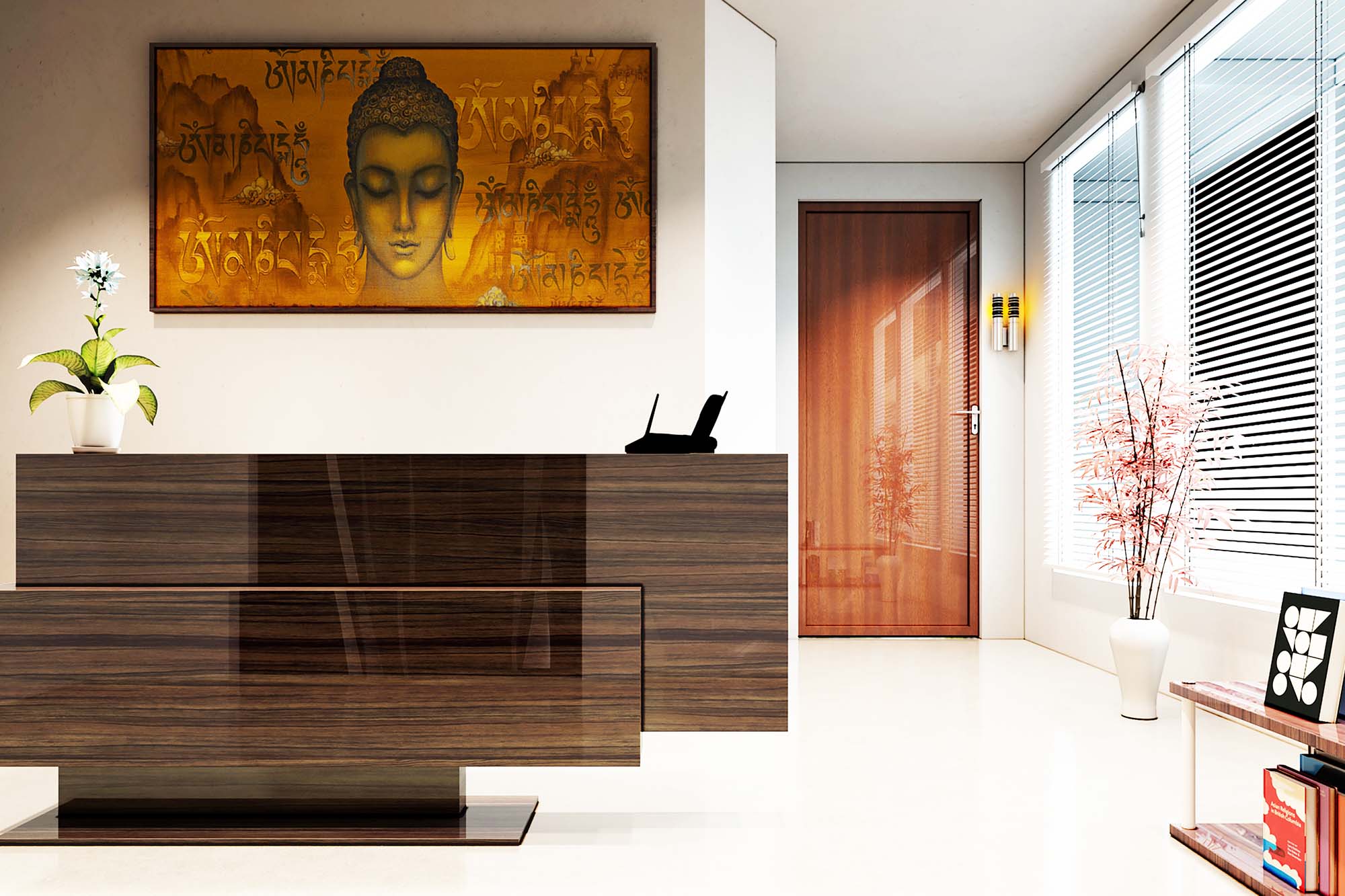
What factors do you consider to ensure proper sealing and waterproofing during the installation of laminates?
Proper installation is critical, especially in humid environments and varying temperatures. Acclimatisation is the most important aspect; before installation, laminates should be stored in the target environment for at least 48 hours to adapt to the local temperature and humidity. Moisture assessment is another crucial step, as excess moisture in the substrate can lead to warping. Our strategies to create an effective moisture barrier include using a waterproof underlayment and sealing the edges with silicone-based caulking. We ensure proper edge banding and joint sealing for high-humidity zones such as kitchens and bathrooms to prevent water penetration and enhance durability. We also share the required practice guidelines with installers through our technical team, which ensures our laminates’ performance.
What factors set your company apart from its competitors?
Innovation, quality, and sustainability are the three pillars on which Merino Industries has built its reputation. Other defining factors are our expansive product portfolio and technology-driven solutions. The product portfolio, with over 400+ designs in multiple finishes and sizes, allows architects, designers, and homeowners to find solutions that perfectly align with their needs. Our tech-driven solutions, which include fire-retardant, chemical-resistant, and high-durability laminates, enhance both safety and longevity. Compliance with GREENGUARD Gold Certification and IS 2046:2005 standards add credibility to our products.
For more details, visit: https://www.merinolaminates.com/en/
Cookie Consent
We use cookies to personalize your experience. By continuing to visit this website you agree to our Terms & Conditions, Privacy Policy and Cookie Policy.