Bridging with formwork
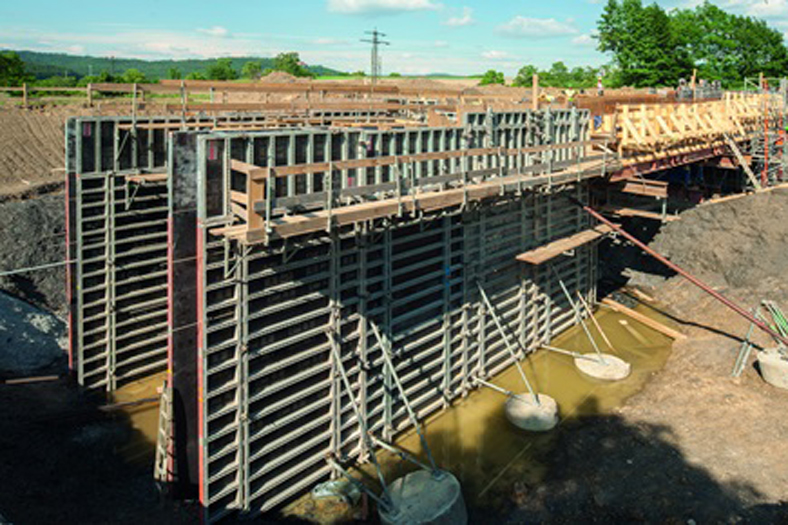
Analysis on how formwork innovation helps in bridge construction
India has developed marvellous bridges over the years and another magnificent piece of art is on its way that is Chenab Bridge which is being built in Jammu and Kashmir which is expected to be taller than Eiffel Tower. There will be many more to come as there are lot of technological development is happening in the way the bridges are constructed today.
Like any other technology formwork also plays a significant role in making bridges. Technology advancement has enabled challenging bridge constructions. Construction technology for the bridges has changed and it has become much easier and less time consuming to build technically complex in-situ concrete bridges. In the ancient times the long suspension bridges were made up manually with wooden beams and rocks. Innovative formwork technology has replaced the manual construction of earlier times. New technologies have defined a way to build impressive bridges from both technical and aesthetical point of view.
Explaining how formwork innovation helps in bridge building Raj Lakhani, Managing Director, PERI (India) Pvt Ltd says, “PERI products are designed to provide users and construction companies with the advantages in terms of handling, enhanced safety as well as cost savings. PERI is constantly into R&D, innovating and developing fast and cost effective solutions for the market. Faster execution on the site is due to proper technical designs and documentations. Due to the varied structure geometries in a project, the advanced system formwork has an edge over the conventional steel formwork. It makes the construction cost effective and efficient.”
The major advantage of using innovative formwork systems is that the standard components can be used as per the project requirement without any modification. “Sophisticated 3D formworking technology helps to give a better visualisation of the structure and helps to do an in depth planning about the formwork technology to be used suitable for the project. It guarantees best possible work flows by determining the time and the sequence of activities. Detail work documents along with the system helps the people on site to understand the application of the system. This helps to achieve cost effective and efficient on site forming operations,” adds Lakhani.
Each bridge is unique based on its wide range of structures, temporary states during construction, construction methodology, and formwork system to be used, safety at site infrastructure, budget and workflow planning, believes a spokesperson from DOKA India. He adds, “Understanding the project requirement, client requirement, involving in the project from tender stage helps us identified cost efficient formwork for the project and with continuous Doka support till completion of the project helps customer to save resources as well as time and money.”
Pradeep Ghumare, Director, NOE Formwork India Pvt Ltd shares few points on how this formwork innovation helps in bridge building:
• NOEtop formwork system saves time and labour
• NOEtop large panels result in short construction times for affordable housing
• Large cast concrete areas offer huge advantage of final perfect and fair-faced concrete surfaces
• NOEtop formwork system is highly cost-effective.
Aadvanced formwork designed for bridge building
To be in race companies are developing innovative technologies. Let us understand what advanced formwork has the companies designed specifically for the bridge building.
Infrastructure is one sector where PERI has a growing footprint. The company has been associated with various landmark projects which includes bridge pylons and bridge piers. It has developed certain state-of-the-art systems especially for the infrastructure projects. It also has proved its mettle in delivery customised solutions for every complex need in a cost effective manner.
Briefing on the advanced formwork that PERI has designed for bridge building Lakhani says, “ALPHAKIT is the new construction kit for shoring structures for bridges with spans and heights of up to 25 m. ALPHAKIT convinces through its minimum number of lightweight individual components and quickly mounted fitting pin connections. PERI SCS is widely used for bridge piers and inclined pylons. PERI SCS serves as a load-bearing structure for supporting single-sided, non-tied or two-sided, anchored wall formwork. The SCS climbing system is a highly cost effective system as the modular concept with multi-piece brackets facilitates optimum adaptation and flexibility to suit project-specific requirements and geometries. PERI VARIOKIT is used for the cantilever construction using balanced cantilever method. It is our experiences and ability to design the formwork as per the project specifications dealing with the technical complexities in the most economical way.”
With a permissible concrete pressure of 88 kN/mt. sq., NOEtop panel formwork system from NOE Germany is extremely suitable for bridge construction projects. NOEtop formwork is available in many different panel sizes: height 0.66, 1.32, 2.65, 3.31 and 5.30 mt; width 0.25 to 5.30 mt. NOEtop XXL panel, with dimensions of 5.30 x 2.65 mt and a form-face area of over 14 mt. sq., is one of the largest formwork panels in the world market. NOEtop large panels can be used end-on or side-on without disrupting the panel grid.”
“NOEtop steel frame formwork system has integral bracing, hence can also be used as beam formwork. The tie-rods can be positioned anywhere within the bracing. All the system’s frames and profiles are hot-dip galvanised from inside and outside to make them extremely robust and durable,” says Ghumare.
NOEtop performs excellently, due to its particularly thick-walled steel frames of 3.5 mm, which give the panels their extraordinary strength. Its system eases the task of bridge construction team in respect of huge range of available accessories: self-securing walkway brackets, articulating external formwork corner units and much more.
Portable NOEtop stripping corners are specially designed for use in lift shafts, stair wells and building shells where space is tight. With its unique design, the stripping corners can be drawn-in on themselves easily, to release the forms from the concrete, and let out again into position for the next pour, without having to dismantle the internal formwork units. Hence dismantling the internal formwork unit, e.g. in the case of lift shafts or stairwell cores, is not necessary when using NOEtop stripping corners.
Moreover, NOEtop’s adjustable internal and external corners make erecting non-square (non-ninety degrees) formwork corners a very quick operation. They have an easily operated mechanism that allows corners to be set at angles between 60 to 180 degrees. A PU corner strip protects the mechanism by preventing cement or rust from forming deposits inside it and stops water from bleeding out of the concrete. Hence the NOEtop stripping corners considerably simplifies the work of the site construction team, where very few walls meet at right angles.
It is possible to cast 15 metre-high fair-faced concrete walls in one single-pour only by using NOEtop – the proven wall formwork system manufactured by NOE-Schaltechnik, Germany. The 15m wall height not only presents the risk of concrete segregation; but particular care is also necessary in the design of the formwork. Its great height generates enormous concrete pressures on the panels during the pour. To be adequately equipped for these tasks, the NOEtop steel frame formwork system is capable of withstanding a concrete pressure of 88 kN/mt. sq., and outstanding robustness.
Whenever there is a demanding requirement of aesthetically uniform concrete surface viz. where majority of concrete surfaces are fair-faced and to be left visible – then use of NOEply formwork facing offers several advantages: It strips off easily from the concrete and gives the surface a consistent appearance, despite being used a number of times. Variations in colour can be avoided.
Doka India has designed a pylon climbing project for Hindustan Construction Company Ltd for their Bandra- Worli Sea link. The advanced climbing formwork SKE 100 helped contractor to achieve difficult shape of concrete and even inclination of the pylon. It provided greater safety, access and workability which lead to successful completion of this project.
Cookie Consent
We use cookies to personalize your experience. By continuing to visit this website you agree to our Terms & Conditions, Privacy Policy and Cookie Policy.