Building Big
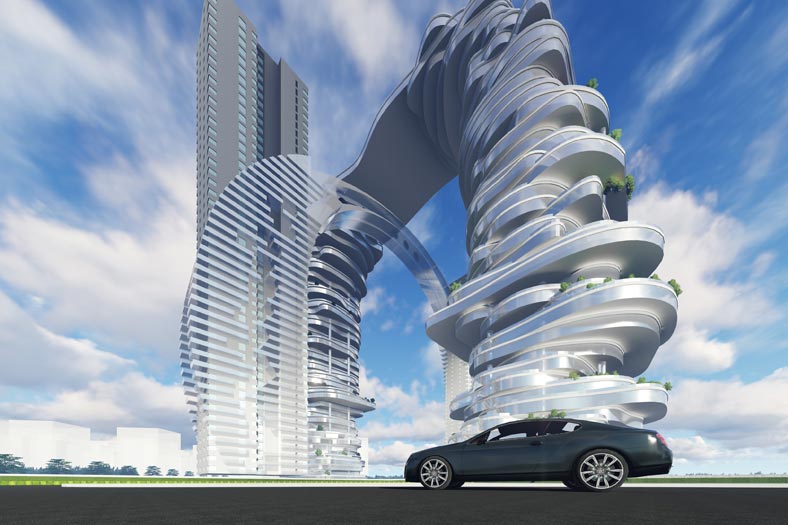
What technology goes into making a high rise building
The uniqueness of a high rise building has always been appealing but in reality it is a very complicated structure. To develop these complicated structures it is very essential to have proper planning, execution, right building materials and most importantly the technologies which play a crucial role in building huge structures. Here we feature some of the latest technologies that go into making high rise buildings.
Ultra high strength, self–compacting concrete
High rise structures include the use of durable materials. Ultra high strength concrete, self–compacting concrete are widely acceptable. Apart from the basic structural materials, modern projects require a variety of secondary materials for a variety of purposes such as construction chemicals, waterproofing materials, durability aids etc.
Sharing his views on technology that goes into making a high rise building Ashwani Pahuja, Executive Director – Technical Innovation, Dalmia Cement (Bharat) Ltd says, “Concrete grades in the order of M80 now being used for high-rise buildings in India. Early high strength fibre reinforced concrete is also being adopted. Self-compacting concrete is one of the most adopted materials where vibrator accessibility is the key issue. Modern concretes are generally made using fly ash, GGBFS, silica fume and chemical admixtures making concrete durable at the one hand and sustainability at the other hand. Corrosion Inhibiters when used for reinforced concrete, minimises the probability of corrosion in reinforcement and thus makes the structure durable. In highly corrosive environment, the use of advanced composite fibre reinforced polymers (FRP) is attractive as a replacement for conventional steel reinforcements.”
Ashok Kularia, Managing Director, ANJ Group adds, “Like any other building the base is very important in high-rise buildings. It has to be strong enough to support really heavy gravity loads. These are usually concrete piers or caissons. The building has to be strong enough to withstand the natural forces such as earthquakes and tornados. Hence, these building are made using steel frames sometimes combined with concrete. Sometimes closely spaced columns are used to make a more stable frame. Some even use bundled-tube systems. In bundles-tube system, in order to make really rigid columns they use framing tubes.”
Precast concrete blocks, hollow blocks, fly ash based light weight aerated concrete walling and roofing blocks etc, are good solution for wall system. Pahuja also informs about how right techniques help speeding up construction. He says, “Selection of advance technique plays vital role in successful and timely completion of the high rise building project. Since these projects are normally executed in mega cities, installation and operation of this huge equipment is a challenge due to space constraint. It is necessary to install high pressure pumps, automated concrete batching plants and placer booms. New construction techniques are also uses jump forms, slip forms, self-climbing forms system, etc.”
Availability of coarse aggregates from natural sources or crushed rock is depleting; at the same time, due to demolition of old structures, roads etc, large amount of debris is generated annually and their disposal pose problems for the society. Research in this area has now established that the debris can be crushed, processed and recycled as coarse aggregate for fresh concrete. Also IS:383 recently allowed to use recycled concrete aggregates for making the concrete but to the limited percentage. “Self curing shrinkage free concrete can also be used produced by combined use of an expansive agent and a PC based water reducing super-plasticiser results in a shrinkage-free concrete even in the absence of any wet curing,” he informs.
High-rise construction is very complex construction system and challenging while execution. Planner need to take into account the construction management system while construction and during serviceability. Pahuja shares the most common complexities/challenges from concrete point of view:
• Installation and operation of construction equipment such as automated form work system, hoists, high pressure pumps, cranes, concrete placer, booms etc.
• Capacity to deliver the concrete above 100 metres height with adequate discharge rate.
• Selection and quality control of optimum/right concrete mix design with desired slump. Pumping of high performance concrete and its temperature control.
• Variability of raw materials and availability of right quality of coarse and fine aggregates.
• Quality control of pumping system and concrete placing method.
• De-shuttering technique and curing methodology of concrete.
Tall building design requires a unique collaboration particularly between the architect and the engineer. This interdisciplinary approach to resolving building planning, construction, and usage issues plays a vital role and because of the scale and complexity of tall buildings, this teamwork often begins at the earliest stages of the design process and continues well into construction, believes Architect S P Anchuri.
He also believes that concrete is preferable. He states, “Many reasons are there why architects, owners, designers, engineers, and contractors, choose to work with concrete especially for tall structures. In fact world tallest building Bhurj Khalifa is in concrete. For end users, there is reduced noise between units, less building sway from lateral forces like wind forces because the mass and stiffness of concrete dampens movement, and above all increased fire safety, concrete can be faster to install than structural steel, we can construct floors on three-day cycles. The advances in concrete technology e.g. self compacting concrete it possible to consolidate concrete around congested steel reinforcement, increasingly an issue for high-rise construction.”
The availability of special ingredients to make very high strength, durable, workable high performance concrete has lead to make it designer’s best choice. Anchuri notes, “It can be seen that most high-rise residential towers, as well as hotel construction, use concrete construction systems. Geographical trends greatly influence building construction decisions.”
Design considerations also influence trends. Structurally reinforced concrete construction becomes very efficient when bay sizes between columns don’t exceed 20×30 feet. This creates an ideal situation for contractors to use flat-plate floor construction methods. Flat-plate floors reduce forming time and increase productivity. Owners also can benefit from this form of construction because it’s sometimes possible to get an extra floor without increasing the height of a building.
Anchuri adds, “When column spaces are wide I feel it is necessary to add either concrete or steel beams or also can go for composite structure, my next best choice.”
Precast technology
As the several technologies available in construction industry the precast prestressed technology will lead on top because it is similar to regular concrete, factory made with good finishes and quality, time saving, required less manpower etc, believes Shridhara C N, Head-Technical and Marketing, Preca Solutions India Pvt Ltd.
He adds, “When we are talking on high rise buildings, lot of things will come in to picture. Firstly, structural stability, integrity of architectural features, integrity of services without clashes. But all these can be easily handled present new technologies and softwares. In precast, always it is safer to construct wall and slab system. After construction it will act as box system. Box structures always more stable in resisting lateral forces like seismic and wind forces. Also this system will give smooth bottom without any column and beam projections. If you construct residential towers the wall and slab system will ease so many challenges of interior consultants. As walls are concrete walls, all the services can be embedded in the walls, no chipping or chiseling work required at site after construction.”
Also as a high rise structures building walls in conventional way using concrete blocks or bricks will consume lot of time and hectic job. If one think of plastering block walls required large manpower and lot of scaffoldings. As precast walls, it will produce at factory and erect at site using cranes Plastering is not required on top of these walls.”If you plan properly even painting can be done at factory and can be erect at site or you can opt for colour concrete itself for casting. It will save lot of time and decrease the maintenance cost,” he briefs.
Tunnel Form technology
There are various construction techniques that are largely followed in India. Aluminium formwork technology is a revolutionary construction system, which has been quite extensively used in India. Using this unique formwork, walls, floor slabs, columns, beams, stairs, balconies together with door and window openings are cast in place in a single site based operation. The resulting building structure is very strong, accurate in dimensions and tolerances, with a high quality of finished concrete surface. It is fast, adaptable and very cost effective. Formwork technology makes use of concrete as the principal building material for the prime reasons of cost and accessibility. It can construct all type of concrete structures.
According to Sachin Bhandari, CEO, VTP Realty, “The process of construction of buildings is getting better, more efficient and seamless by the day because of advancements in technology. One such technology that specially helps with high rise buildings and we use at VTP Realty is called Tunnel Form technology.” It is a highly efficient industrialised system of onsite construction. In this technology, a stable structure is put up on a 24-hour cycle basis. It enables the builder to construct large slabs and walls in one operation on a daily cycle. This technology brings together speed, quality and precision of concrete produced in factory with the flexibility of in-situ construction. This technology is a perfect fit for repetitive cellular projects; for instance, hotels, schools, apartment blocks etc. The tunnel form technique is commonly used for multi-storey buildings as it reduces cycle time.
“Another popular technique for high-rise buildings is Jump Formwork, where the formwork supports itself on the concrete cast earlier so does not rely on support or access from other parts of the building. Jump form systems are suitable for construction of vertical concrete elements in high-rise structures,” informs Bhandari.
Shuttering technology
For high rise building the shuttering technology is the most important issue, says Yashaswi Shroff, Director, Alcove Realty. He adds, “The shuttering should be such that it can take care of all the parameters of safety, quality, ease of operation and the speed. System shuttering is the norm for high rise buildings.”
The exact type of system shutter depends from building to building, depends on the height, depends on the architecture. Super high-rise building generally use jump form and also for a medium high rise building it is aluminium shuttering is generally used. This gives a perfect verticality and ease of construction especially it can cater to the speed which is required for high- rise building.
Cranes and hoists
In a high-rise building construction, tower cranes are used for transporting all the materials and the passenger hoists are for transporting the manpower from the bottom to top and both of these have to take care of the height and also the safety parameters. “For a high rise building cranes have to be much superior, higher speed for lifting and also when multiple cranes are used it is to be seen that one crane does not collide with the other,” suggests Shroff.
Cookie Consent
We use cookies to personalize your experience. By continuing to visit this website you agree to our Terms & Conditions, Privacy Policy and Cookie Policy.