How PEB can save money
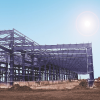
Analysis on money saving aspects of using PEB.
Indian construction industry which consists of infrastructure, housing and real estate, and industrial segments has grown by leaps and bounds for past decade and half and accounts for more than 9 per cent of India’s GDP.
Quality of construction has also improved significantly over the last decade due to increase in exposure to the global construction technologies and best practices. The project duration has become shorter and there is a special focus on safety standards. There is a shift from in-situ construction to factory–controlled pre-engineered high quality construction. This has also changed the requirement of engineering, material and skills required for the construction industry.
The usage of steel and especially PEB has grown very rapidly in the Indian construction industry. PEB concept was not well known in the country and since then has experienced tremendous growth which has increased the awareness among consultants, customers, entrepreneurs, builders, contractors, architects, etc. In current scenario, anyone planning to put up a factory or a warehouse immediately thinks of a PEB with the industry yet to achieve its true potential. With adequate attention from the government, this industry can dramatically reduce construction time for industrial and infrastructure sectors and will be very economical for construction industry. Pre-engineered construction impacts speed, quality and pricing of industrial construction, has green benefits, and a high resale value. It’s not surprising that Indian industrial construction is eminently poised for a big PEB wave given India’s renewed focus on infrastructure and the new industrial thrust. Though PEB has many advantages but how far is it economical is a crucial aspect.
Sharing his views on how PEB can save money D Raju, Managing Director, Kirby Building Systems India Pvt Ltd observes that PEB is not expensive rather it is economical. On this note, he says, “The perception about PEB being costlier is only a notion as the industry has grown by more than 15 to 20 per cent during the first decade of this century and is growing at a slower rate for last 5 years or so due to global economic factors. This growth is in itself shows that these structures are not very expensive but economical in nature as the overall project cost comes down.”
He also adds, “With companies looking for faster project completion which in turn will give faster returns on their investments, PEB is the only one stop solution to fulfill their requirements.”
On the other hand, Gautam Suri, Founder and Director, Interarch also agrees upon Raju’s views. He says, “The higher cost barriers is just a preconceived perception of people who have never used PEB. We feel the market for pre-engineered steel construction is growing exponentially in India with consumers opting for new-age technologies as well as the need for fast construction. All sectors in India are expanding in terms of business and more and more companies are coming to India which gives pre-engineered steel sector huge potential to grow.”
Suri mentions some of the pre–engineered steel building have unmatched advantages over a concrete building in this case some of the factor which may influence are:
• Construction time is reduced by at-most 30 to 40 per cent which gives early occupancy and early ROI.
• Large clear span structures up to 100 metre and clear height of up to 30 metre are possible and mezzanine floors can be constructed which help in maximum usage of space and hence provide better utilisation of money spent every sq. ft.
• Less energy consumption due to sky-lighting available in industrial and warehouse buildings hence less electricity consumption.
• Easy to construct and easy to expand in future when required without disturbing existing operations.
• Fire and earth quake resistant – very low or negligible maintenance cost which again saves in overall cost of the building.
• Cheaper foundation work due to lighter foundations.
PEB is no more a new concept in India. It’s application is very well known for construction of Industrial buildings. Jayanta Chakraborty, Sr. GM-SCM, Phenix Construction Technologies shares some of the prevailing reason for choosing PEB over conventional buildings are:
Reduction of construction time: Buildings are typically delivered in just a few weeks after approval of drawings. Foundation and anchor bolts are cast in parallel with manufacture of the building. Site assembly is fast, as all building components are delivered finished, ready for site bolting. This reduces total construction time on a project by at least 50 per cent.
Optimisation of resources: Buildings are designed in such a way that usage of steel is reduced to the minimum possible extent by using efficient design tools like Strucad, Omnicad, Tecla etc. This is done without compromising the strength of the building. In fact, building stability is tested in severe seismic and high wind speed environment before the building leaves the drawing board.
Flexibility for future expansion: Buildings are future ready in terms of expansion. This gives a great relief to the promoter or inventor.
Large clear space inside the building: Buildings have efficient clear space. This provide efficient utilisation inside the built-up area.
Negligible maintenance cost: Buildings are constructed and painted in such a way that hardly any maintenance is required. Buildings are normally coming up with 25 to 50 years structural stability. Even roof sheeting and wall sheeting provided with 10 to 20 years colour fading warrantee.
Energy conservation: Buildings are fitted with natural ventilation and lighting system – resulting to reduction of electric energy consumption. Even rain water harvesting can be done by very simple modification of the building. To make the energy conservation more effective, some entrepreneurs are putting solar cells at the roof top for energy conservation.
Building aesthetics: Buildings are no more a means of housing machinery in it. Now buildings are fashion statement as well. Architects are more focused on the look of the building. PEB gives a most economic solution to that as well. Simply forming the wall panel in a different way and by putting structural glazing, the building looks elegant. Weather proof and fire hazard: Safety first, is the slogan all buildings that are manufactured now. By carefully selecting specific building material – buildings are made fire resistant (insulation, paint, etc). This also enhances the life of the building without radically changing the cost structure.
Opportunity cost: Due to the systems approach, there is a significant saving in design, manufacturing and site erection cost. The faster occupancy and earlier realisation of revenue. The saved time in construction has indirect effect on higher ROI. The overall price per square metre may be as much as 30 per cent lower than conventional building.
Future opportunities for PEB
The government’s ‘Make in India’ campaign and recent approval of ordinance for amendment of Land Acquisition Act for development of infrastructure and industry related projects will further give a boost to the PEB industry. Further, the government is planning for implementation of 100 smart cities and this can be efficiently done using pre-engineered steel construction as done in developed countries providing an affordable and sustainable material for construction. Structural steel demand is based on India’s economic growth and new CAPEX investments or announcement of new projects mostly in the construction industry consisting of infrastructure, industrial infrastructure and real estate segments. Recent announcement of increased investment in the infrastructure segment and revival of stalled projects including some new investments will help the growth of steel structures in India
.
————————-
The perception about PEB being costlier is only a notion…
D Raju, MD, Kirby Building Systems India
—————————
The overall price per square metre may be as much as 30 per cent lower than conventional building.
Jayanta Chakraborty, Sr. GM-SCM, Phenix Construction Technologies
———————–
The higher cost barriers is just a preconceived perception of people who have never used PEB.
Gautam Suri, Founder Director Interarch
Cookie Consent
We use cookies to personalize your experience. By continuing to visit this website you agree to our Terms & Conditions, Privacy Policy and Cookie Policy.