Indian construction market needs globally popular high-tech solutions
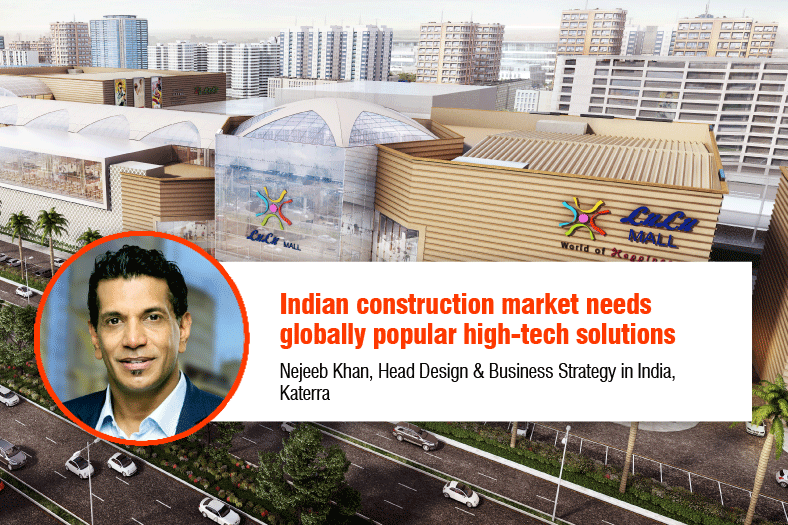
What is the status of your ongoing projects in India?
In India, companies in the retail, commercial buildings, hospitals, hotel, and residential space are our key clients. We have witnessed keen interest in adopting a modern technology-driven approach amongst players, where the construction completion time is critical to business success. At present, we are working with brands such as Infosys, Embassy Group, Lulu Mall, Bosch, KMCH Hospitals, Vaishnavi Builders, GEMS Schools amongst others, and are in the process of completing and delivering over 5 million sq. ft, spread across varied projects by December 2019.
For Infosys, we are in the process of constructing their fourth project, an office building covering about 1.6 million square feet, located at Electronic City in Bengaluru. Apart from this, we are also building the largest mall in Lucknow – Lulu Mall, 2 million sq. ft. and second hospital project for KMCH, 1 million sq. ft. The company has recently won new business – second office building with Embassy – 3A, GKNM Hospital and around 1.5 million office building space in Hyderabad.
What kind of technology have you adopted widely across the globe for construction?
At Katerra, we are using technology across the building delivery cycle right from design to procurement and offsite manufacturing to onsite installation and delivery of the building. Our technology-driven building products are designed for manufacturing and assembly (DFMA), which enables our clients to benefit from speed and cost optimisation while still having a unique building design.
Our automated assembly-line, factory-built components including, bathroom, rooms, double walls, beams amongst others are entirely built offsite including all mechanical, electrical and plumbing work, finishes, and fittings. Finished components are delivered onsite (JIT) just-in-time using predetermined software simulated schedules and assembled onsite. Using this integrated technology approach helps us deliver projects 50 per cent faster and more sustainably than traditional construction.
What are the best practices in the global construction world that is being brought to India?
Across the globe, Data-Driven Design, DFMA, Modular Construction, Offsite Manufacturing, Intelligent Buildings, and Construction Software are gaining prominence. These new solutions need to be adapted to suit the Indian market and its unique needs to bring about real change. To cater to India’s growing demand for quality community infrastructure like offices, hospitals, hotels, malls, and housing, using traditional construction methods would not suffice. With the help of local R&D and global technologies, Katerra is developing advanced construction methods and solutions for the Indian market. The use of such an approach is critical to delivering quality infrastructure.
What is the current market scenario and what does the future hold?
Slated to have the world’s third-largest construction industry by 2025, India is witnessing a high uptake of modular techniques within its construction sector. We have the potential similar to China to embrace technology-based construction methods and build world-class infrastructure, faster and better than ever before. Today, every MNC is growing its footprint in India, which indicates that there will be a significant requirement for offices and tech parks across the country in the coming years. Alongside this, India also has a growing need for quality retail, housing, education institutions, and hospitals to support its booming urban population. We believe the construction industry in India has tremendous potential, and it will be an important market for Katerra.
What are the company’s investment plans in India?
Katerra started in India over two years ago developing construction based software solutions. We then entered construction operations in 2018. In the short span of two years, we have already tripled in revenue. Apart from our factory at Krishnagiri near Bangalore, we have broken ground on a 50-acre offsite manufacturing factory in Hyderabad, to cover the South region. Next, we have plans to invest in a mega plant in the Mumbai-Pune region in the latter part of the year, followed by a plant in NCR to cover the North market. The plan for Katerra is to have five mega plants in the country within the next four years and 15 to 20 smaller onsite plants to be able to address pan India needs. Our overall goal is to cover markets across India through substantial investments. Our investments in India currently stand at INR 250 million-plus, which is estimated to grow upto $ 750 in the next 5 years.
Data-Driven Design, DFMA, Modular Construction, Offsite Manufacturing, Intelligent Buildings, and Construction Software are gaining prominence globally and these new solutions need to be adapted to suit the Indian market.
Nejeeb Khan, Head Design & Business Strategy in India, Katerra
Cookie Consent
We use cookies to personalize your experience. By continuing to visit this website you agree to our Terms & Conditions, Privacy Policy and Cookie Policy.