The advent of tech-infused prefabrication
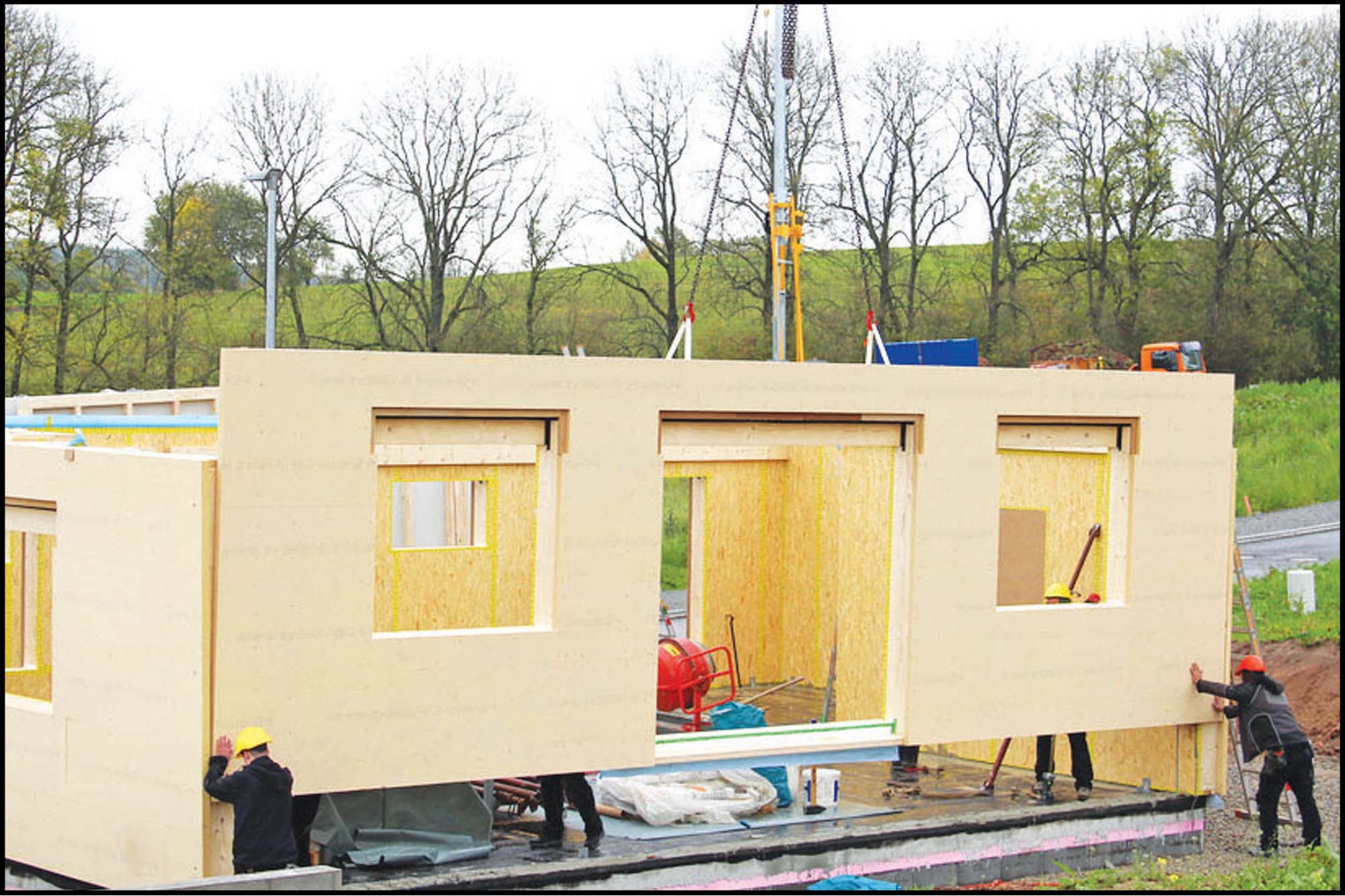
The leading experts across the PEB and Prefab industry have shared their views on energy-efficient building designs, highlighting the latest advancements, cutting-edge practices, and sustainable technologies for modular construction.
In recent years, a notable technological shift in prefab, PEB (Pre-Engineered Buildings), and modular construction methods is observed. Advancements across various fronts mark this transformation. Digital design tools like Building Information Modelling (BIM) have revolutionised planning and coordination. At the same time, the exploration of advanced materials and manufacturing techniques, such as 3D printing and robotic assembly, has enhanced efficiency and precision in production. Off-site construction and assembly have become increasingly prevalent, leveraging controlled factory conditions to expedite timelines and improve construction quality.
Advancements in design software, materials innovation, manufacturing techniques, automation, digitalisation, and sustainability characterise the prefab, PEB, and modular construction technology shift. These advancements enable architects and engineers to create precise, intricate designs while utilising lightweight and high-strength materials such as engineered timber and advanced steel. Modern manufacturing techniques, including off-site prefabrication and robotic assembly, improve efficiency and quality control while automation streamlines processes and reduces labour costs.
“Lavina Rodrigues, Founder of Pyra Built & Designs, highlights the versatility of 3D printing technology in construction, the efficiency of BIM for planning, the enhanced performance offered by AI integrated with AutoCAD, and the potential of upcoming technologies like Linder for quicker measurement, while addressing challenges such as supply chain constraints, skilled labour shortages, regulatory hurdles, cost limitations, and design flexibility issues in the context of the growing demand for PEB and prefab construction, noting the comparative flexibility limitations of prefab construction against RCC.” Further to the discussion, Rahul Jindal, Managing Director of Loom Crafts, underscores the significance of embracing technologies like BIM and AI to propel the future of the prefab industry, particularly in addressing India’s skilled labour shortage, emphasising the need for a shift towards a more process-oriented approach in prefab construction.”
“Hamsavardhan, Founder of PRESET Building Systems Private Limited, emphasises the shift towards factory-based manufacturing in construction, highlighting that the majority of building components are now produced off-site and assembled on-site, with technology playing a pivotal role in this transformation, leading to a reduced focus on on-site work and a greater emphasis on factory-made components.”
Structural steel, insulated metal panels (IMPs), and fibreglass reinforced panels (FRP) are top choices for climate efficiency and durability in prefab and PEB constructions. Structural steel provides unparalleled strength and versatility while being highly recyclable. IMPs offer excellent thermal insulation and weather resistance, which are ideal for reducing energy consumption and ensuring longevity. With their lightweight yet durable properties, FRP panels provide corrosion resistance and thermal insulation, making them suitable for various weather conditions. Together, these materials contribute to sustainable and resilient prefab and PEB structures, meeting the demands of diverse climates while minimising environmental impact. Lavina says “In our prefab projects, we’ve experimented with various materials for walls, such as ready-made panels for easy assembly, doubling up as slabs, eliminating the need for Siporex blocks or brick walls, and incorporating prefab staircases, resulting in significantly faster construction times due to off-site manufacturing, which would otherwise take weeks.”
The surge in demand for prefab and PEB (Pre-Engineered Buildings) is catalysing the need for a proficient workforce adept at implementing these modern construction methodologies. With these innovative techniques gaining prominence, construction firms need more skilled labour trained in prefab and PEB methodologies. To confront this challenge head-on, industry stakeholders invest in workforce development initiatives and vocational training programs tailored specifically for prefab and modular construction. These initiatives strive to equip workers with the requisite skills and expertise to fabricate, assemble, and install prefab components efficiently. Furthermore, collaborations between educational institutions, industry associations, and governmental bodies are fostering the creation of specialised curricula and certification courses aligned with the demands of prefab and PEB construction. In alignment with this trend, Rahul observes that prefab demand is soaring in the market due to its unparalleled speed in construction. Prefab structures are meticulously designed and manufactured in factories, ensuring structural robustness and driving up demand. However, addressing the need for skilled labour rests on the shoulders of manufacturers, who are responsible for adapting workers to the technology and providing comprehensive training programs.
Transportation constraints impact the feasibility and cost-effectiveness of modular or prefab projects. The size and weight of modular components may require specialised transportation arrangements, such as oversized or heavy-load permits, which can add logistical complexities and costs to the project. Transportation distances between the manufacturing facility and the construction site can also affect project timelines and expenses. Longer distances may incur higher transportation costs and increase the risk of delays due to traffic or adverse weather conditions. Moreover, limitations in infrastructure or accessibility to the construction site can further exacerbate transportation challenges, potentially hindering the efficient delivery and installation of modular components. While discussing the challenges, Hamsavardhan states, “To mitigate these challenges, strategic planning, coordination, and consideration of transportation factors are essential to optimise project outcomes and minimise overall expenses.”
Cookie Consent
We use cookies to personalize your experience. By continuing to visit this website you agree to our Terms & Conditions, Privacy Policy and Cookie Policy.