The four dimensions of industrialized construction
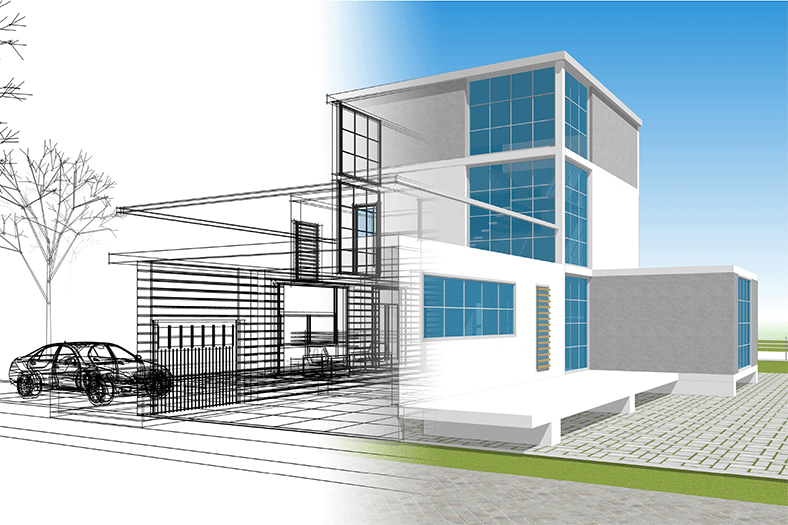
This detailed analysis has been co-authored by Eric Ottinger, Harshit Minglani, Mark Gibson, FRICS and Amanda Alexander.
Introduction
Industrialized or manufactured construction is a familiar concept. We have been building with components and even whole wall panels for years. However, with a heightened focus on efficiency due to skilled labor shortages and tighter margins, industrialized construction is accelerating across the globe. As we noted in our first paper, “Technological advancements disrupting the global construction industry,” modular and prefabricated building accounted for approximately US $237b of construction activity in 2019.1,2 This industrialized (“prefabrication”, “prefab” or “modular”) approach shifts many activities away from the construction site and into a factory. Prefabricated building components are then shipped from the factory to the construction site for assembly. While this technique has been around for centuries, recent success stories have compelled developers and contractors to apply prefabrication to their projects. Utilizing this approach can present new opportunities, however, it introduces additional risks to consider as well. This research explores the opportunities and risks of industrialized construction in relation to the four core dimensions of project management. The research concludes with a high-level assessment and potential future state of the industry.
Introduction to industrialized construction
Industrialization realizes benefits from standardized designs that are repeatedly applied and executed in a controlled environment. Factories are typically set up using these designs to mass produce a product or limited selection of products. Similarly, with industrialized construction, it is more feasible and efficient to build the same product repetitively. As such, industrialized contractors arrange their factory to produce a limited selection of prefabricated building products. According to a survey conducted by Commercial Construction Index (CCI), 62% of general contractors are using prefabricated components, of which nearly half have seen increased use in the last three years.3 Industrialized construction is typically applied by contractors utilizing one of five typologies. Typologies range from individual components to complete modules that are prefabricated in the factory and then shipped to the site location.
Precast concrete is one such prefabricated module, usually identified in Typology 1 or 2. It has been gaining widespread popularity, especially with advancements in geopolymer cement products and prefabricated lightweight aerated concrete (PLAC). Having extensive application, the precast concrete building systems provide an alternative solution to the routine and time-consuming process of forming and pouring reinforced concrete. It can be performed offsite and then later transported to the construction site. In Middle Eastern countries, many houses are built with concrete floors, roofs and walls. General contractors reported using prefabricated and modular exterior walls in 65% of their projects.3 Design repetition of housing presents a significant opportunity for industrialized construction. Countries around the world are struggling to meet the demand. In 2014, McKinsey projected that 1.6 billion people would be in need of affordable housing by 2025.5 That number has already been surpassed. In March 2020, the United Nations (UN) reported that 1.8 billion people in the world live in substandard housing conditions or homelessness.6 The UN projects this to increase to 3 billion people by 2030.7 This problem will continue to escalate with urban expansion and rising prices. Slow income growth and the prospects of a recession further exacerbate this issue. The Organization for Economic Co-operation and Development showed that 2019 quarter three housing prices have grown faster than incomes in over half of countries.8 This research suggests that it will take approximately US $1.6t to US $2.1t per year to address the growing affordable housing gap in the next 10 years.9 Should the demand continue to accelerate at the speed of the last five years, the cost could be substantially more.
Scope
Opportunity
Given the increasing demand of projects that could be built using prefabricated components, there has never been a better time to adopt industrialized construction. There is no limit to where industrialized methods can be applied, and anything with a repetitive series of components are ideal building types. However, the decision to build using modular construction techniques and adopting the applicable design solution must be made early. Identifying the scope of work early in the planning phase is especially important. This is relevant to small pods and panels, as well as entire buildings designed and constructed this way. New opportunities in the commercial sector are being explored. Asset classes, such as office and retail, are being added to the usual candidates of multifamily, hotels, mixed use and hospitals; all which have building components that can be standardized for replicated application. This doesn’t mean that all of the buildings have to look the same. The structural and foundational components of walls, floors, ceilings and roofs can be constructed using industrialized methods while still allowing for customized finishes. Offices, conference rooms, restrooms, hallways, kitchens and bedrooms can be constructed in modules as well. Case studies, such as Broad Sustainable Building’s modular 57-story Ark Hotel, have paved the way for commercial contractors to pursue this strategy. During adverse times, such as the COVID-19 pandemic, prefabrication has made vital contributions to remediation efforts. Utilizing prefabricated modules, Chinese contractors built a 1,000-bed, 645,000 square foot medical facility in 10 days.9 When commercial design plans incorporate repetition of components and modules, industrialized construction can become highly beneficial and attractive.
Risk
Historically, design standardization has led to declining interest of home buyers and high-end commercial developers. Owners often want a unique product that showcases aesthetics. Commercial developments attract customers with customized features that enhance the user experience. In many cases, projects require customization. Predefined conditions, such as plot size, structural regulations and design ordinances are unique to a project’s location. When constructing tenant improvements, designers and contractors must work within the confined interior build out. Likewise, inherited projects are typically predesigned or partially built at the time of acquisition. Many developers often require additional customized options and finishes. These situations can be challenging when applying industrialized methods.
Limited design options are often not fully context- or user-specific and can lack the ability for customization. Should customization be required, the contractor may have to modify its standard industrialized scope. Design and factory changes can incur time, cost and quality implications. In some cases, contractors may have to revert back to traditional construction methods. We have seen some modular construction projects that were functional, aesthetic and financial failures. All of these failures were traced back to a lack of definition during the planning phase, where elements should have benefited from industrialized methods at the outset. Failure to properly design the industrialized components into the plan set led to subsequent issues on-site. Like most construction projects, risk increases with the size of the building.
This risk becomes more prevalent when utilizing industrialization. Single family homes are much easier and repetitive to construct than large commercial projects. As commercial projects scale, customization requirements increase in complexity, thereby decreasing the application of a standardized approach. Understanding the level of customization is key to determining feasibility. Risk analysis should always be conducted to determine if and to what degree an industrialized approach is the most effective option. The industry is still working to understand these limitations, and how best to scale industrialized strategies.
Time
Opportunity
Industrialized designs can be reapplied to multiple projects, saving time in the planning, procurement, manufacturing and deployment phases. With similar products repetitively being built in one factory, production time is reduced. Nearly 79% of contractors reported schedule reduction using offsite factories.³ As processes become more standardized, workflows and efficiencies become optimized. Workers have predictable schedules because they perform the same activities continuously on a daily basis. Sequential production lines are established that alleviate crowded workspace and allow mobility.
Enhanced coordination enables less rework to be performed. All tools and equipment are readily available in a factory, which minimizes down time. Building inspectors can perform approximately 90% of their inspections within the factory, alleviating the need to schedule multiple site inspections.10 With inspectors coming to factories on a daily basis, consistent relationships and expectations are established that further enhance productivity. It also alleviates inspection delays, which are renowned in booming metropolises. Industrialized construction also offers contractors the advantage of preparing the construction site and prefabricating building components in parallel. Whereas city ordinances often only allow construction during daylight hours; factory work provides the benefit of performing many activities 24 hours per day. Work performed in the factory reduces labor on the project site by up to 80%.3 With much of the traditional trade work brought in-house to the factory, it eases the burden of on-site management. Multiple contractors are alleviated from “working on top of each other,” as they are often required in a traditional setting. Approximately 89% of contractors have realized increased on-site efficiency when using industrialized construction.
Less on-site activity reduces dependencies on the schedule’s critical path. Because the on-site work is limited to constructing the foundation, assembling modules and applying finishes, the schedule is compressed. A simpler, sequential progression can then be established. McKinsey found that industrialized construction leads to schedule compression of up to 50%.11 Schedule compression also minimizes environmental risks, such as weather and seasonality. When the construction site is wet, windy or experiencing extreme temperature; it can slow productivity or delay work until conditions improve. On the other hand, factories provide a controlled, interior environment that is maintained on a daily basis. Moisture is mitigated, wind is removed and temperature remains consistent, thereby allowing work to continue.
Utilizing industrialization, a 2,500 square foot house can take approximately six weeks for site work, three weeks to assemble the modular components and an additional seven weeks for the façade and finishes to be completed.10 This is substantially less than traditional construction that can take eight months to build the same house.
Risk
While there is increasing demand for construction; productivity in the industry has been lagging far behind that of general manufacturing.12,13 This is due to many factors, including increasing design complexity, more regulation, demand for eco-friendly materials, and reduced availability of skilled labor and raw materials. Whereas general manufacturing has seen increased automation, industrialized construction is still reliant upon field labor. If the assembly teams are not experienced at panelized construction, time and costs will increase. If the panels are not aligned correctly, the design does not accommodate industrialized manufacturing. In particular, failure to design to industrialized construction can lead to significant rework on-site due to misalignment. Due to this, accurately estimating productivity in modular projects carries risk. New industrialized methods do not have years of project data to utilize for analysis. Additionally, productivity assumptions are highly sensitive in this industry. As each module is built in the production line through a sequential process, underestimating the time to build one component can impact the entire project.
This estimating uncertainty has steered many developers away from industrialized methods. Conducting a sensitivity analysis on one industrialized project’s housing panels, we found that each panel had a 3.13% impact per hour of production. If a mistake were made in the initial panel, it could affect the construction of other components down the production line. Scaling production to thousands of panels and components amplifies this risk and could cause a contractor to operate behind schedule from the onset of a project.
Change orders during the manufacturing process are therefore particularly damaging. Ultimately, there should be fewer errors in industrialized construction, however the consequences can be much more severe. As site work (excavating, foundation, etc.) and building components in a factory occur simultaneously, it introduces another risk. Delay of site or factory work may impact the other. If site work is delayed and the material or components are ready, additional staging area could be required. If the site work is completed but the prefabricated components are not ready, the construction site may sit idle. This risk is less of a concern when purchasing materials “off the shelf,” as in traditional construction. Contingency plans for such instances should be established for every project.
Cost
Opportunity
Reducing schedule duration through repetition leads to lower construction costs. McKinsey reports that industrialized construction can cut costs by up to 20%.11 With most industrialized designs repeatedly used for multiple projects, design costs can be allocated proportionally. Customized design costs are typically 7% to 12% of a project budget. Depending on repeatability, industrialized design costs can be 10% to that of traditional construction projects.10 In addition to cost savings, this presents opportunity for revenue diversification, such as selling inhouse architectural designs and prefabricated components. As industrialization continues to gain efficiency, investors and contractors can realize a quicker payback period due to a compressed schedule, leading to less interest cost. This also allows for the general conditions’ scope to decrease.
Monthly costs, such as project and site management, project controls, traffic control, daily cleanup, property protection, security, equipment usage, rentals and utilities therefore become much lower. Cost savings are found in the factory setting as well. Factories reduce waste by controlling inventory and protecting building materials, whereas construction sites can be disorganized causing tools and material to go missing. According to CCI, 79% of contractors highlighted reduced waste as a key benefit of industrialized construction.3 Industrialized standardization also stipulates that work is executed with greater precision. Therefore, fewer measurement errors are made that require materials to be discarded.
Additionally, as the modular structure is substantially completed inside the factory; there is less weather, vandalism and theft risk, thereby reducing material damage and replacement. With less exterior exposure, equipment’s useful life is expanded as well. Industrialization also provides cost savings in labor. Site labor often requires specialized trade subcontractors that charge a markup. Much of this trade work, such as mechanical, electrical and plumbing (MEP), is moved in-house to the factory and can be conducted by lower-skilled manufacturing labor. General contractors reported using prefabricated and modular MEP systems in 51% of their projects.3 The site labor is therefore reduced and has lower skill requirements as well, where the primary task is to assemble the premanufactured components. As in any industry, lower-skilled labor demands less payment than skilled expertise. Almost 70% of contractors reported lower construction cost as one of the key benefits of adopting prefab and modular technology.
Reducing on-site equipment and labor with enhanced coordination in the factory make it easier to implement safety measures. Approximately 71% of contractors highlighted safety as a derived benefit of industrialization.3 With factories operating in a controlled setting, industrialized projects have an estimated 80% lower accident rate than site-intensive construction.5 Enhanced safety allows work to be performed with confidence and can alleviate costs derived from accidents.
Contractors can realize additional cost savings by integrating the supply chain and centralizing procurement to the factory. It can provide greater control and flexibility of logistics and an ability for economies of scale. Ordering greater material quantities in bulk, contractors can purchase directly from manufacturers and remove intermediaries’ markups.
Risk
Industrialized construction faces financing challenges unlike the traditional industry. New methods of industrialized construction have a limited track record, resulting in many lenders hesitant to commit. If a developer is able to secure the initial financing, underbidding could require additional capital. When lenders do approve, a significant upfront payment and higher interest rate are often required. Typically, lenders allocate monthly loan draws based on percentage of on-site work complete. With industrialized construction occurring in the factory, the offsite prefabricated components do not add value to the construction site. The percent complete becomes difficult to assess, therefore impacting loan distributions.
Lenders will often limit industrialized loan distributions to site work, component delivery and project completion milestones. This requires contractors to maintain greater amounts of working capital. Should their liquidity dry up, supplier payments can be disrupted, leading to material and service delays. Industrialized firms may have significant upfront costs. Recently built factories with specialized equipment have cost upwards of US $100m. McKinsey estimates that the allocated factory cost can consist of between 5% and 15% of a project’s total budget.11 Architectural designs and manufacturing processes must be developed as well. Semitrucks built for oversized loads are often purchased to transport the prefabricated modules. Whereas cost reduction is expected in the long term, the capital investment is mostly speculative. These capital expenses and any operational costs should be included in return on investment calculations of the supported projects. Some industrialized firms are experimenting with temporary portable factories at the construction site.
This comes with its own set of risks. There is added infrastructure cost for building each portable factory, some of which (i.e. foundations and utilities) cannot be carried to the next site. Additionally, the footprint may not be readily available or incur rental costs. It requires additional transportation, staging, mobilization and demobilization. Assembling and replacing specialized equipment can be complicated, time consuming and require specialized labor. Whereas prefabrication work is executed in a predictable factory environment, transporting equipment and modules to the construction site can be challenging. Robust project, supply chain and logistical controls are required to ensure timely and effective deliveries. Size, shape and material have to be considered. Small streets, hills, bridge clearances and power lines may have to be avoided with oversized loads. Bumpy streets can cause concrete and other brittle materials to crack. Modules with drywall and windows have increased risk due to compression and movement. When damaged, it may require shipping replacement materials. One way to mitigate this risk is to build the modules stronger.
This often requires additional time and material. Added costs for logistics, transportation, packaging, material and insurance are to be expected. Some larger industrialized companies have been working toward owning multiple stages of the supply chain. This incurs additional operational risks. Contractors must commit to greater vertical integration of design and construction early in the project lifecycle. Managing both the factory and construction site can be challenging. Mistakes in the factory can affect assembly of the on-site modules. Should assembly errors happen, replacement materials or modules may be required.
Often, and especially with young or fast-growth companies, poor coordination incurs additional costs. All processes and departments need to be in complete alignment. Resource selection and adequate training is essential to operating any specialized equipment and properly manufacturing and assembling prefabricated components. These skillsets may require unique and additional training. Due to the project-based and cyclical nature of the construction industry, contractors often rush selection and training. Ambitious growth or schedule plans may drive a company to hire and mobilize quickly. This increases the chance that performance expectations will be missed
Quality
Opportunity
Standardizing the factory processes can vastly improve production quality. Repetitively performing distinct tasks enables specified skillsets to be gained. Standard operating procedures help ensure accuracy and consistency. This can also enhance quality by providing a more thorough inspection than traditional construction. Components can be tested in the factory at different build stages for resilience and sustainability. Should modifications be required; they can be completed prior to being shipped to the site. Subsequently, better quality products can be quickly replicated to scale output. Almost 73% of contractors identified increased quality as one of the key benefits derived from prefabrication.3 Increased production quality can have a significant impact on building operations. Less repairs for leaks and building settlement will be required.
It can help alleviate the regular maintenance program and prolong the useful life of the asset. This supports whole life costing of a building, of which operations can be up to five times the cost of the capital investment.14 As the industry transitions to the use of robotics, exact specifications will be met on a routine basis. The arrival of 3D printing, machine learning, artificial intelligence, internet of things, and other technologies are expected to provide additional quality enhancements. Completely integrating automation can eventually eliminate errors, enhancing the user experience.
Many contractors are applying digitization to the built modules as well. New technologies, such as sensors, energy management systems, solar panels and battery packs can be incorporated with internet of things to create smart buildings. This enhances sustainability and enables carbon neutrality, net zero energy use and predictive maintenance. Founded in 2015, Katerra has developed fully integrated building systems with data feedback loops, providing customers an end-to-end solution that enables better visibility and decision making. Enhanced construction and building operations mitigate global warming. With construction and buildings estimated to contribute 39% of worldwide carbon emissions, the market for lean and green construction is experiencing rapid growth.15 This has increased the awareness of industrialized sustainability benefits.
As the prefabricated structures are also built much quicker, less energy is expended than traditional construction. Less time on the construction site reduces contamination, such as fumes and runoff. It also produces less noise pollution and public disturbance, which often instigates neighborhood complaints that can subject mandated working hours. By eliminating waste and minimizing its environmental footprint, industrialized construction can be a driving factor to petition communal support. Modular buildings can also be recycled. Certain components can be disassembled, relocated and refurbished. This reduces the demand for raw materials, further minimizing the amount of energy used to create a building. It also introduces the potential for multiple uses. In the last decade, developers have used shipping containers to build affordable housing and student apartment complexes.
Risk
Industrialized construction products have a poor industry perception as being cheaply constructed with low-quality material that leads to substandard performance. Unfortunately, this is based on the mobile and modular home industry of the past, where this has been historically accurate. This negative connotation has kept many developers and investors away to avoid exposure. While this perception is a barrier for new entrants, it is improving for most users who have experienced newer prefab and modular products. With enhanced technology constructing higher quality products, this historical market perception is no longer accurate. Nevertheless, it will require substantial marketing and years of continued success to build industry trust.
Conclusion
While industrialized construction is gaining momentum, a “house-hold brand name” has not yet been established. To achieve this accolade, many firms are focusing resources on digitization and employing new strategies in prefabrication and modularization. Technology is a dominant theme and is laying the groundwork for the future. It continues to transform the back office and supply chain of the development process and reshape conventional property uses. Many of these technologies, such as robotics, 3D printing and internet of things, are expected to provide substantial contributions. As innovation continues to influence industrialized methods, industry demand will rise for expedited schedules, lower costs and greater quality to maximize value creation. This will help meet the rising need of affordable housing and sustainable infrastructure. With market forces aligned to substantiate economic activity, the construction industry will continue to drive industrialization forward. We expect that a dominant set of players capitalizing on this opportunity will emerge in the next five years. They will focus exclusively on industrialized construction, and will bring design, supply, manufacturing, construction and assembly all under one roof. Their business models will focus on repetitive building types such as multitenant or single-family housing. These industrialized builders will be influential to homebuilding as Tesla has become to automobiles. With anticipation of derived benefit, it is unlikely that any of these dominant players will be traditional construction companies.
Instead, they will become vertically integrated, technology-backed manufacturers. Such industrialized disruption and opportunity have expanded interest of investors and capital markets. As more capital flows into the sector, there will be increasing scope for the lines between traditional and alternative structures to merge. With technology driving market acceptance and growth, new financial models will be developed. Different mathematics will be applied to understand the cost, time and quality factors. As componentization becomes commonplace and transferrable to various asset classes, financers will be able to evaluate the modules while still in the factory. This will help lift lending restrictions and make capital more accessible.
Efficiency levers will further lower the cost of capital. We expect to see lending products transition to manufacturing models in the near future – based on ROI, margin and profitability. Additional profits will be captured and cost savings shared between the contractors and customers. This will enable industrialized growth to begin approaching an exponential upward trend in regard to the global construction industry at large.
Cookie Consent
We use cookies to personalize your experience. By continuing to visit this website you agree to our Terms & Conditions, Privacy Policy and Cookie Policy.