6 advanced materials for future buildings
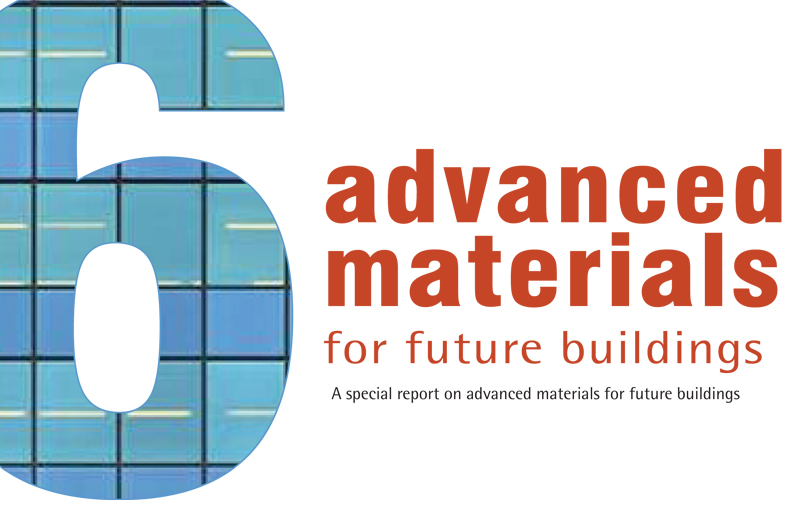
A special report on advanced materials for future buildings
Construction chemical plays a major role in the construction industry and it has changed the way the construction is done today. Due to various requirements in construction industry there are many advanced construction chemicals are used during the construction like additives, concrete chemicals, composite materials etc which are already changing the construction industry. Here we bring an article on advanced building material that will change the future of construction.
Most advanced construction chemical
Dry-mix systems
In a few years from now, with widespread knowledge of the interaction of new materials and application technologies, the proliferation of technology in the construction sector will be unparalleled and will transform the way we build in India.
While explaining the most advanced construction chemical that will change the future of construction Sunny Surlaker, Head Admixtures Division, MC-Bauchemie (India) Pvt. Ltd says, “The construction chemical industry is more about “Evolution, rather than Revolution”. Dry-mix systems, be it in the form of plasters, mortars, waterproofing or flooring are being preferred to make the construction faster and easier. However, costs do have an effect in pushing the widespread use of these types of materials.”
Keeping this in mind, MC-Bauchemie introduced special additives that will bridge the gap between the construction chemicals and the dry-mix industry. Instead of using multiple additives to enhance properties of mortars, we have come up with a single additive system for mortars. Mc-plaster additive is an additive for large scale production of plaster, imparting stability, water retention, non-sagging, and bonding properties to plaster.”
Mc-plaster additive is a combination of selected additives designed to impart the plaster with specific properties like resistance to water penetration, stability, non-sagging, open time, workability and water-retention. The solution can be customised for a variety of options. Dosage is economical at 0.1 to 0.4 per cent by weight of the dry-mix or 0.5 to 1.0 per cent by weight of cement.
External building plasters are the first line of defence in providing the external envelope to the building walls. Surlaker observed that plastering the external walls in the building, today involves multiple problems like quality of cement, availability of quality natural sand, wastage on account of plastering practices and skilled labour for application. “We at MC-Bauchemie, sought to address the plastering from the material point of view. MC’s plaster additives combines many benefits like waterproofing, excellent bonding, thixotropy, smooth finish, minimal rebound, spay ability and minimal labour into one well-designed product. This material can be used universally for: site-made plaster, dry-mix mortar manufacturers or masonry cement manufacturers to enhance the properties of plaster or similar mortars,” says Surlaker.
MC’s plaster additive has the robustness to convert any mortar, to a spray able, easily finish able, durable wall plaster. The robustness of this formulation, allows it to be used with multiple raw material sources including crushed sand, manufactured sand, GGBSF, fly ash, natural sand, PPC and other base raw materials for plaster. The company believe this material to be an excellent bridge between making site mixed mortars to manufacturing excellent dry-mix mortars. It is a product that meets a niche, but widespread need in the construction industry for external finishing of structures.
Composite materials
Composite materials are set to change the future of construction. These are polymers reinforced with glass/natural/carbon fibres. Composite materials are not new – they are used widely in windmills, marine industry and recently, to greatly reduce the weight of commercial aircraft. In current times that require superior performance in demanding conditions (corrosion resistance, higher strength, and increased durability) at the same time managing weight implications, composite materials provide the perfect material choice for construction.
Describing about the features of composite materials Jashan Bhumkar, Director-Business Development, Soujanya Colour Pvt Ltd shares, “Having one-fifth the density of steel, composites are lightweight materials that match up to and sometimes even exceed the strength and stiffness of conventional construction materials. Composite materials are 30 to 45 per cent lighter than aluminium structures designed to the same functional requirements, and at the same time have 4 to 6 times greater tensile strength. Fibre Reinforced Plastics (FRP) has strength-to-weight ratios 50 times that of concrete and 18 times that of steel. The high strength-to-weight ratio means that additional floor space can be added by using composites. They can be used effectively in waterway bridges that have a lift-up section to reduce energy requirements in lifting.”
Composites have inherent corrosion resistant properties making them suitable for use in exterior cladding, ducts, saline environments, water handling systems and underground applications. The various fabrication processes – casting, infusion, lamination, extrusion, pultrusion, moulding etc, lend great flexibility to the design with complex, aesthetically pleasing shapes possible to be made with ease.
Soujanya Color offers a complete colour solution for composites. The company’s flow able liquid colours with brilliant tinting strength are compatible with all composite systems including FRP, epoxy composites, unsaturated polyester, polyurethanes, etc, and can be used in various fabrication processes. These colour dispersions mix easily with the composite matrix and lend an even UV-stable, non-fading colour tone to the material. Moreover, these products are solvent-free and are have greater than 50 per cent biodegradable components.
Flowable stone
Construction chemicals are an inevitable part of the concrete making process today. With the advent of special types of concrete, the expectations from pouring flowable stone have changed manifold as most of the structural engineers want to play around with the sections available to the client at large, believes Nachiket Choksi, Director, SKOF India. Sizing, dimensioning and all that has got to do with the finished aesthetics, strength properties; durability of the structure is available from the concrete product in today’s advances in concrete technology.
But a great challenge lies ahead to the concrete technologist who has to get all these performances from the constituents of the mix to the final product keeping in mind the requirements of the designers, believes Choksi.
Making concrete behave, occupy places – the way someone thought it to do and behave as required; has brought in a lot of homework to the work table of the manufacturers of admixtures who have to ensure that the product has to perform with the many numerable properties of products given by mother nature and also manmade products made from mineral additives that add to the performance of the flowable stone. “Through our experience at SKOF India, and through the numerous trials on molecules of Polycarboxylates, we derive that PC is the product for today and tomorrow, which by virtue of its properties of reduction of the water to cement ratio; has been the product of the era to better construction technologies and construction products,” adds Choksi.
Expansion agents and carboxylic ether with heat less technology
Expansion agents and carboxylic ether with heat less technology modified will change the future technology of the construction, believes Arvind Agarwal, SP ENG MSPE UK, SPL Ltd. He says, “As it will save energy time and hopefully will be more economical. These products are eco friendly and create better architecture designs. Besides this give longevity to construction. It will also reduce overall cost of maintenance and further protect weathering effects of concrete. The product is workable for all temperatures.”
The product saves water for curing of concrete. It will also help constructing three designed developed infrastructure with less weight. It is very helpful in trench less technology and precast construction. High strength concrete with high slump retention and water proof concrete may be formulated with good surface finishes. The main advantage reducing coercion and water saving without effecting concrete hydration.
Self-healing concrete
You can’t expect path-breaking innovations to happen (telephone, electricity, internet or cell phone) in the construction chemical sector, believes Dr.Subash Cipy, Managing Director, Cipy Polyurethanes Pvt Ltd. He says, “This (construction chemical) segment is relatively slower to adopt and adapt newer technologies, which might be due to the massive scale of this industry, which accounts for 8 per cent of GDP in India and 6 per cent of global GDP.” There are now a few technologies emerging which will bring notable changes. The development of self-healing concrete would definitely change the shape of future world. As everyone knows, cracking of concrete is a major problem in construction, usually caused by exposure to water and chemicals. Researchers are looking to develop a self-healing concrete, using a mix containing bacteria within microcapsules, which will germinate when water enters a crack in the concrete to produce limestone, plugging the crack before water and oxygen has a chance to corrode the steel reinforcement.
He adds, “Efficient thermal insulation materials are becoming increasingly important throughout the construction industry. Ceramic or glass microspheres are commonly used for this purpose, but, Aerogel, a technology developed by Nasa for cryogenic insulation, is considered to be the futuristic insulation material. The super plasticisers, currently based on polycarboxylate ethers, which offer unbeatable versatility and performance, are going to be replaced by bio based polymers which are green.”
High performance elastomeric anti carbonation, water repellent and heat reducing coating from Chembond
Concrete may be exposed to many environmental conditions and hence requires protection. Among the less aggressive of these is atmospheric carbonation. Carbonation occurs because carbon dioxide diffuses into the concrete and dissolves in the pore water. This produces carbonic acid which reacts with lime to form calcium carbonate. Coatings may be applied to concrete to arrest the carbonation process.
“KEM proof ultimate is a high quality acrylic emulsion based coating launched by Chembond. KEM proof ultimate is elastomeric in nature and has good resistance to weather and sunlight. It is single component system containing inert pigments and fillers suitable for application by brush, roller or spray. It prevents chloride ion ingress and exceeds all the requirements of a coating that resists carbonation and provides a smooth, durable and water repellent coating for concrete and masonry surfaces,” briefs Swapnil R. Deshmukh, Marketing Manager, Chembond Chemicals Ltd.
Uses:
• KEM proof ultimate is designed to bind and to protect concrete structures against carbon dioxide, air/water born chlorides.
• It is also used as elastomeric water repellent coating for asphalt, timber, fiber cements and zinc sheets.
• It may be applied to many types of substrates particularly those commonly requiring elastomeric anti carbonation and water repellent coating like concrete bridges, highways, structures in marine environments, car parking structures, commercial and industrial buildings, flat and slopping roofs.
• Also acts as heat insulator and protects from damage and reduces heat conductivity.
Advantages
• It acts as a comprehensive barrier against carbon dioxide, water, sulphates and chloride ions.
• It maintains its appearance and elastomeric performance with high recovery even after long term UV weathering.
• Easily applied by roller, brush or airless spray.
• It is capable of bridging cracks and withstands substrate cracking up to 2 mm and cyclic movement up to 1 mm.
• It acts as a barrier against salts and atmospheric gases.
• Masking imperfections in substrate.
• It protects concrete from waterborne salts.
• Water vapour can escape from the structure.
• Helps in reducing room and surface temperature, thus helping to keep room cool.
Coverage
KEM proof ultimate – 3 to 4.5 m²/litre/2 coats
Cookie Consent
We use cookies to personalize your experience. By continuing to visit this website you agree to our Terms & Conditions, Privacy Policy and Cookie Policy.