Advanced concrete mixing technologies
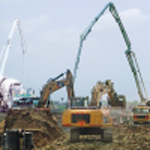
Featuring innovations in concrete mixing technology.
As the demand for housing is increasing every day, the demand for the construction also increases. This increase in the demand has given birth to many technologies, and therefore the challenges for companies to develop advanced technologies and machines for concrete pumping and mixing. Though these technologies are very common and one can find it on the construction sites, these modern mixing technologies have become an essential aspect of the construction realm, as it gives proper mixed material for the use of building construction. These machines helps combine cement, water and other building material to form concrete which is then applied to during construction. On the other hand, these technologies comes with additional qualities such as saving time, money, man power.
Advanced technology
Finishing the projects in minimum time has become an objective of the construction industry. This maximum work in minimum time can be achieved by advanced technologies, new concepts and latest products. To tell a few, products like planetary mixers by Ajax, ring pan mixers from Liebherr and the drum concept by Schwing Stetter are developed to serve the construction industry.
Apart from concrete pumping technologies, concrete mixing technologies is widely used in the construction industry. To give a brief, mixing is a systematically controlled random process. In the concreting industry, the purpose of any mixing process is to bond various raw materials such as aggregates, cement, water etc, with diverse properties to a single substance known as concrete. In mechanised mixing processes, these materials are subjected to targeted acceleration and set into motion relative to each other. There are various mixing technology available to the customers to choose as per their project requirement.
“Ajax Fiori always believes in customer satisfaction and all its products are designed as per customer requirement,” states Debasis Bhattacharya, Head – Sales, Marketing & Product Support, Ajax Fiori Engineering (India) Pvt Ltd.Giving information on mixing technologies, Bhattacharya shares, “The batching plants supplied by Ajax Fiori are with superior planetary mixers and customised PLC based control system. The planetary mixer is robust and extremely efficient at mixing.” He adds some of the key benefits of planetary mixers over conventional turbo mixers that are:
• The planetary mixer mixing tools rotate in a synchronised manner and are able to turn the material distributing all of the material uniformly in the pan without favouring the different nature of the materials creating a homogeneous mix; each revolution changes the flow pattern.
• The intensity of the mixing action, appropriate speeds combined with design of the mixing tools provide a complete homogenisation and an efficient flow pattern.
• The pan of the planetary mixer is completely empty thus allowing the material to cover the complete area in a minimum time.
• Planetary mixers have a single type of mixing tool with a geometry that together with a combination of movements distributes evenly the material.
More so, these planetary mixers are manufactured in-house under strict quality control procedures, in technical collaboration with Eurostar, Italy. World over, the planetary mixers have replaced the turbo mixers for most applications, owing to its capability of producing high quality concrete of different types.
The unique product offerings in Ajax Fiori batching plant range are: Compact batching plants with planetary mixer – capacity of 30 cu.m/hr. and 60 cu.m/hr. Their new launch compact reduced bin with planetary mixer – capacity of 30 cu.m/hr. And in line bin type batching plants with planetary mixers / twin shaft mixers – capacities of 30 cu.m/hr. to 180 cu.m/hr. Ajax Fiori also manufactures their unique batching plant namely the radius lift ARM batching plant of 20 cu.m/hr and 30 cu.m/hr with reversible mixer technology.
“While talking about mixing technology we would also like to talk about our flagship product which has a drum mixer technology. Self-loading Mobile Concrete Mixers (SLCM) of Ajax Fiori has shifted the paradigm of producing concrete for small and medium scale infrastructure projects and for all construction activities in semi-urban and rural areas in India,” states Bhattacharya.
Further Bhattacharya added that, Ajax Fiori is the pioneer in bringing this very unique mixing technology way back in 1992 with joint venture with Fiori, S.p.A. Italy. Before the onset of SLCM technology in India, contractors were dependent on static mixers at one end or on batching plants at the other end. While the static mixers have limitations on productivity and quality, the batching plants are not cost effective because the size of the projects and the corresponding concrete requirement does not justify the same.
Ajax Fiori’s “ARGO” series of self-loading mobile concrete mixers has just bridged the gap very effectively. The USP of these machines have been mobility within job sites, productivity of quality concrete and substantial reduction in manpower. The versatility of these machines explain the fact that they have been the perfect choice for contractors over wide applications ranging from canal linings, check dams, residential and commercial buildings, industrial structures, urban infrastructure, windmill and transmission line foundations, roads and curbs, drains and culverts, to name a few.
“Schwing Stetter India manufactures concrete transit mixers which are without reason the number one in Europe and India,” states V G Sakthikumar, Managing Director, Schwing Stetter Sales and Services Private Ltd.
The innovation of concrete mixers came into being in order to make the tedious process of transporting concrete for long distances easy. “We are working closely with many chassis manufacturers for mounting of our range of concrete mixers on Asia Motor Works ltd, Ashok Leyland Ltd, Daimler India Commercial Vehicles, Mahindra Vehicle Manufacturers Ltd, MAN Trucks India Pvt Ltd, TATA Motors Ltd, and Volvo Eicher Commercial Vehicles Ltd,”informs Sakthikumar who is Chairman of Mechanization committee, Builders Association of India.
Briefing on the drum concept Sakthikumar says, “Concrete mixers manufactured by Schwing Stetter India are designed with a beginning of statically and functionally ideal shape of the drum of largest diameter of the largest possible mixing chamber volume. Stiffening cone in the bottom drum for wear protection to provide corresponding stability. The additional plates on the drum shell on transitional points are particularly subject to wear. The drum wall thickness in these places is thus increased to 9 mm without unnecessary increase of weight. This provides safety for innumerable cubic meters of work output.”
The mixing drum and spirals are made of highly wear resistant steel with a high percentage of Chromium and Nickel. The apparent yielding point and the tensile strength are the two features that prove the capacity of resistance to wear. The well-conceived thickness of the mixing spirals and drum shell round off this as an economically-sound solution.
High speed and constant discharge of material due to varied spacing of the spirals from the bottom of the drum to the discharge piece, the special design of the mixing spirals in the discharge area and the large diameter of the drum outlet offers a huge advantage. AA protective grating, folded edge protection at the discharge hopper and an oversized clamping brake on the swivel chute complete the safety measures. All controls (levers and the panel) are available at one place, thereby making the operation user friendly.
Ergonomical, built to last, smooth pouring, high productivity are the key features of our equipment with a drum technology that solely drives on longevity. Concrete mixers that has been mounted on chassis which has been commercialised are of various capacities from 4 to 10 cu.m.
Further Sakthikumar states, “We develop for every new chassis introduced in the market an application in the concreting equipment industry. This could be a truck mixer or a truck mounted concrete boom pump on a 6×4 or 8×4 truck chassis.”
Last several years, Aquarius has delivered state-of-the-art-technology concrete batching and mixing plants to number of precast factories across India and abroad. “Today, Aquarius stands out as a leading manufacturer and supplier of precast application batching and mixing plants with total 13 plants performing in India and 1 plant in Africa at present, states Yogesh Salvi, Manager – Export & Special Application, Aquarius Engineers Pvt. Ltd.
Aquarius manufactures precast series batch plants to cater need for dry and wet precast concrete requirements of precast factories. Sharing the features of the batching plant Salvi says, “ We have custom delivered these plants equipped with several key features like: Planetary and twin shaft type mixers, specialised control software and interlocks, it has moisture probes, it has high precision water dosing mechanism, it has concrete shuttle monitoring system and varied levels of automation.”
Each of the precast application batching plant is unique in several aspects. The selection of right type and capacity of batch plant mixer is an important aspect in a precast factory set up, as it is a key to enhance productivity of the unit in totality. Speaking on the technology Aquarius provides Salvi informs, “Right from the inception, Aquarius is manufacturing batch plants with planetary and twin shaft mixing technology. Aquarius batch plant designs have inherent flexibility to update and orient the plant footprint as per the precast factory setup requirement. Till date, Aquarius has delivered the largest capacity batching plant in India equipped with 2 No. x 2 cu.m./batch capacity mixers on a single platform.”
Highlighting on the offering from Liebherr Dr Dobler says, “Liebherr ring-pan mixers are constructed in nominal sizes of 0.5 cu.m. to a maximum 3.0 cu.m. An agitator system is available as an option up to a nominal size of 1.5 cu.m. Upwards of 1.5 cu.m. The agitator system is included as standard, and a double agitator system is even possible as an alternative option. Ring-pan mixers featuring agitator systems are ideally suited for the concrete goods and precast element industries. The high-grade concrete types used in these sectors, such as SCC (Self-Compacted Concrete) and UHPC (Ultra-High Performance Concrete) necessitate intensive mixing procedures with high energy input.”
Conclusion
Advanced concrete mixing technology is the need of the hour for the construction industry to provide well mixed materials that will provide strong constructions. The consistent growth in the construction industry will increase more competition amongst the equipment players to introduce new technologies which will be much more advance than the existing products.
Hopefully in the coming years, the industry will be ready to see and bring much more advanced technologies that will take the construction industry to the next level.
—————————————————————–
The batching plants supplied by Ajax Fiori are with superior planetary mixers and customised PLC based control system.
Debasis Bhattacharya, Head – Sales, Marketing & Product Support, Ajax Fiori Engineering (I) pvt Ltd
———————————–
Ring-pan mixers featuring agitator systems are ideally suited for the concrete goods and precast element industries.
Dr. Gerold Dobler, Head – Corporate Communications, Liebherr-International Deutschland GmbH
————————————–
Concrete mixers manufactured by Schwing Stetter India are designed with a beginning of statically and functionally ideal shape of the drum of largest diameter of the largest possible mixing chamber volume.
V.G. Sakthikumar, MD, Schwing Stetter Sales & Services Pvt. Ltd.
—————————–
Right from the inception, Aquarius is manufacturing batch plants with planetary and twin shaft mixing technology.
Yogesh Salvi, Manager – Export & Special Application, Aquarius Engineers Pvt Ltd.
Cookie Consent
We use cookies to personalize your experience. By continuing to visit this website you agree to our Terms & Conditions, Privacy Policy and Cookie Policy.