Advanced design approaches – a necessity for the construction sector
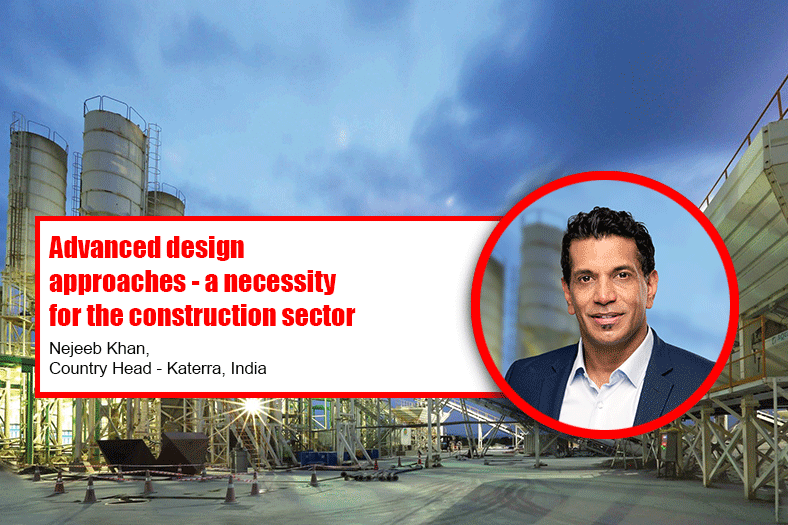
In a timeline when the Covid-19 crisis has restrained the operations of the construction world across the globe, it’s time to bank on a new design approach like DfMA says Nejeeb Khan, Country Head – Katerra, India.
India, similar to most countries in the world is working diligently to manage the Covid-19 crisis. The country’s medical fraternity is the first line of defense, and they are doing a stellar job, all things considered. Most cases of Covid-19 are being handled in government hospitals, and data from the National Health Profile 2019 shows that India has around 7,13,986 beds, which is just 0.55 beds per 1,000 people, an abysmally low number.
An epidemic like coronavirus necessitates the creation of more hospitals and increasing the number of beds available, both for critical care as well as management of a pandemic, while, of course, still taking care of nonCovid patients with chronic ailments. Using advanced design approaches such as Design for Manufacture and Assembly (DfMA) has its advantages in the construction sector. It can play a significant role in the management of a pandemic like Covid-19. DfMA combines two methodologies; Design for Manufacture (DFM), which means the design for ease of manufacture of the parts that will form a product, and Design for Assembly (DFA), which means the design of the product for ease of assembly. DFMA forms the foundation of offsite construction.
The intricacies of hospital design
Hospitals are complex constructions comprising of a range of services and functional units. Every hospital has diagnostic and treatment sections, clinical laboratories, imaging, and emergency rooms, as well as complex surgery departments and theatres. They also need to incorporate hospitality functions of foodservice and housekeeping alongside a wide range of in-patient care services. Having wide-ranging features and requiring high-end mechanical, electrical, and telecommunications systems, hospital construction faces three main challenges – high costs, time delays, and cost overruns.
Hospitals typically do not have standardized design components, which often leads to starting the project based on prior designs and, without a clear patient care pathway, resulting in creating inefficiencies. Modular design and build platform strategies can address these complexities of hospital construction, thus reducing time in project delays, ensuring the project stays within budget and adding further monetary value.
Katerra, a US-based technology-driven offsite construction company has created a hospital build platform, that is essentially a catalog of standardized modular components, and subsystems, complying with global hospital standards and care-pathways, forming a library of hospital designs. These not only help to reduce the time and cost of multiple design changes, but it also offers clients a design library of options, based on their requirements, which is personalized, while still being built with high efficiency.
Hospitals in a Katerra catalog may range from small 15-bed to more extensive 500- bed facilities, with the number of predesigned modules, customized or changed based on customer requirements. The completion time can be between 2 weeks to 2 years, depending on size, almost 75 per cent faster than traditional hospital design and build projects. Using a building platform design approach, Katerra can provide form and functionality customized based on estimated patient flow and medical specialties. Design is based on optimized patient care rather than only aesthetics.
Decoding the design process
The four crucial part of a design processes are as follows:
- Standardized Components – Bathrooms, Rooms, Patient rooms, MEP, etc.
- Modular approach – Components can be flexible across different building design types.
- Efficiency – To ensure the design is most efficient with minimum unique parts.
- Personalization – Personalization comes through the facade, interiors and fit-out options, fixtures, and interior design aspects.
Here’s how it all comes together. For instance, a 500-bed hospital that will have around 2-3-bathroom types, each can be designed following a standardized design instead of building them separately following a DfMA approach. With DfMA, all building components are manufactured offsite in a factory-controlled environment without compromising on design quality. The modules are assembled using automation, and robotic technologyled assembly-line production methods. Finished modules are then transported and assembled onsite. This approach allows companies to reuse identical parts and components and produce bathrooms in an assembly line system and simply install onsite with an easy plug and play. The simplicity of an albeit sophisticated technology has now made it feasible for use in small- and large-scale construction projects of every kind.
DfMA for faster hospital construction
The several benefits of the DfMA make it the ideal one to use for the building of hospitals in the country in a short frame of time. With this approach, a 400-bed hospital can be built in two weeks. This hospital will have all that is needed of an isolation center and can be created to include central testing and diagnosing cores, segregated out-patient areas, and a separate emergency block for acute patients. It can have an open-plan observation layout and multiple levels of quarantine sectors – segregating those who need life support and quarantine.
Typical isolation hospital design modules would include 14-bed isolation wards, isolation rooms, quarantine, and observation wards along with the other sections. These can be constructed in a 9 step sequence, with pre-cast solid walls, columns, beams, and hollow-core slabs with inter-connectors enabling quick assembly on site. All of the design, construction, fabrication, and assembly can be monitored with a single unique software that is created to track and tie together all the processes involved.
In India, DfMA has been extensively used in the infrastructure sector for large scale construction projects such as bridges and flyovers. The use, however, is still in the nascent stage in the consumer sector. The coronavirus pandemic has brought to the forefront; the need for a quick turnaround in hospital construction and DfMA is critical in making this possible.
Covid-19 has highlighted the need for technology in all sectors and construction is no different. Automation and digitization in construction are crucial aspects today. Technology plays a significant role in the transformation of traditional construction methods. Offsite construction is a proven technology effectively being adopted in several countries like China, the USA, Australia, across the Middle East, and Singapore as well. Its efficacy must be promoted in India – the adoption of construction technology will be critical for developing essential building services in India, especially in sectors like – healthcare, housing, education, industrial buildings, and others. The current situation has highlighted more than ever the need for construction technology, and we must make adopting this a priority.
Cookie Consent
We use cookies to personalize your experience. By continuing to visit this website you agree to our Terms & Conditions, Privacy Policy and Cookie Policy.