Integrating systems, processes, methods in Construction & Maintenance
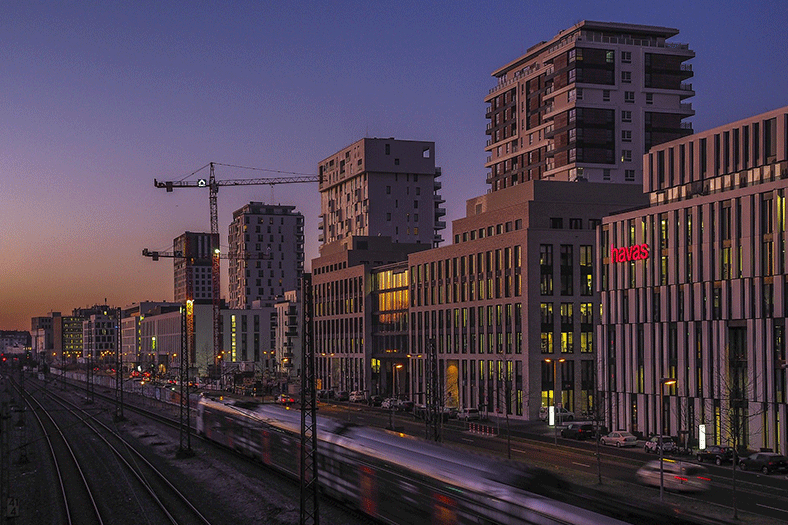
Construction mandates the symbiosis of man, machine and innovative technologies. In the long run these three elements re-converge to preserve the built environment and keep them functional.
Evolution, innovation and preservation is an essential element of any environment, the survival of all species depends on it. So likewise in the built environment, the buildings and bridges need to be constructed and preserved. Hence human civilization has consistently witnessed a circle, a circle of construction, restoration and maintenance, which also includes demolition. A circle which keeps afloat the existence of the concrete civilization we as humans have invented.
Construction mandates the symbiosis of man, machine and technology. Today we have witnessed an increase in vertical expansion and huge infrastructure projects. This is a clear result of the innovations being witnessed in the construction sector. Projects which were unthinkable yesterday have been created today. Right from Vidyasagar Setu to Bandra-Worli Sea Link and Trump Towers to BKC the exposition of the buildings and allied infrastructure continues to enthrall the urban ecosystem.
Construction of mega projects tend to have their specific needs and the manufacturers usually tend to respond accordingly. The utilization of traditional formworks has been witnessed in the realm of construction and infrastructure development. Even today it is used. However, keeping in tune with the needs of the emerging metropolis formwork systems have evolved. Tunnel Formwork System is a result of this evolution “Using one set of tunnel forms,” says Satish Kolaki, Managing Director, Satcon Engineers and Construction Equipment “you can build the shell for a house in one day Regardless of the building system or materials used, and there is no faster way to build a house than with tunnel form construction. With the smallest labour force, walls and decks (ceilings) require only one forming operation and single concrete placement.
Tunnel form construction can be ideal for high-rise buildings, student hostels, hospitals, joint family and nuclear -family residences, hotels, townhouses, military housing, prisons, and some warehouse applications. But to take full advantage of the system, the decision to use tunnel form construction must be made before the design process starts. There must be a crane on the jobsite, and there must be the opportunity for repetitive use of the tunnel forms.”
Unique project challenges often turn into opportunities for innovation and product development. In the current pandemic situation getting the requisite amount of manpower is a challenge. Different companies have taken note of this development. “In its VTC tunnel formwork system,” says Raj Lakhani, MD, PERI India “PERI has integrated many simplifications or, let’s say, features which make it easier for site personnel to operate the formwork. Many details make sure that mistakes cannot be made in the first place. These clever solutions can be explained to the customer in detail by the specialist consultant in a coordination meeting. In other words, especially in the case of “high-end” equipment, many of the work steps are simplified or even removed from the site crew. This means, on the one hand, that less personnel is required and, on the other hand, that only very few well trained workers are needed.”
Usually, construction and infrastructure projects are bound by deadlines to ensure the cost of the project does not shoot up. To meet deadlines too technological innovations come to the rescue. The Motera Stadium, which happens to be the largest stadium in the world decided to use precast technology for timely completion “While posing a major waterproofing challenge, the decision to adopt precast technology was the game changer in being able to deliver the project,” says Ishita Manjarekar, Technical Director, Sunanda Global, “in such a short construction time. For example, cast in situ columns would have put the timeline at over 7 years as the design involved 43 Y shaped columns which would have required two months each. However, by switching to pre-cast technology, the timeline was much reduced with columns gaining the required strengths in 10-12 days.”
The use of precast and prefabricated technologies is a global phenomenon from mass consumption properties to individual properties, its use is profound. The Porto-based architectural SUMMARY Studio designed the newest project using their prefab and modular building systems. In the whole building, the structural material – precast concrete – is directly exposed, without any additional finishing, thus reducing the resources, the manpower and the arts involved in the construction process and, consequently, reducing its environmental impact. The prototype of the project was released earlier at the exhibition in La Biennale di Venezia Manmade marvels of construction have to remain functional over a period of time. Hence today there are a number of companies in the construction sector alone who specialize in providing maintenance. From façade cleaning to structural strengthening all aspects are covered diligently. As long as we keep in tandem with nature and carry out timely maintenance of the projects, they will serve us for centuries. If you have a doubt take a look at the heritage structures, they will convince you for sure.
Structural strengthening is one of the major focus areas in the maintenance of aged buildings. The methods of achieving this is numerous. Vishal Kakkar, Business & Projects Head and Partner, Envisage says “The strengthening method of any structure is dependent on the materials of construction. Structural elements of existing buildings are commonly constructed of concrete, steel, timber and masonry. No matter what strengthening innovation is used, the ability to perform as an integrated system can be obtained only by providing an adequate bond between the existing members and the repair/reinforcement to ensure a monolithic structural behaviour. The changing times that we are a part of, demand for us to go back to the basics of what we learnt at architectural school and relook at the spaces we design from a holistic perspective of creating a healthy building. A sound structure that can bear the high seismic activity and a healthy building in response to the post-pandemic situation are our high focus areas right now.”
Anand Sharma, Founding Partner, Design Forum International says “For exposed steel structures, weather-resistant paints are applied. Especially in the coastal areas where the air is saline, there are specific coating available to protect the exposed steel structures from corrosion. Newer technologies such as metal coatings are now used in the structures to elongate the lifespan. The coatings are either done using hot-dip galvanization or thermally sprayed metal coatings. To protect concrete structures, the first line of defence is to use concrete with low water permeability and use adequate cover around the reinforcements. These days with innovations in the materials, high-quality cement is available in the market, which ensures that the corrosion doesn’t set inside the concrete structure.”
Apart from the existing methods and techniques of maintenance in place, robotic building maintenance is gradually being adopted. Shiju Bhaskaran, Project Manager – Turner India says “Robotic maintenance units are now available in the market making easy access for men and materials attainable for the entire building perimeter. Automated Robotic units are one of the recent additions to the BMU technology. In future, the use of robots in areas of building maintenance and facility management is expected to increase. Future designs of buildings could be with access arrangements for robots to maintain it. New sensor technology will provide better visibility through robots as compared to human vision. When the technology advances further to a state where robots could be entrusted with hazardous and unwelcome tasks, one of the serious problems faced by maintenance engineers will get solved. Nanotechnology and artificial intelligence are expected to make revolutionary changes in the construction industry.”
Cookie Consent
We use cookies to personalize your experience. By continuing to visit this website you agree to our Terms & Conditions, Privacy Policy and Cookie Policy.