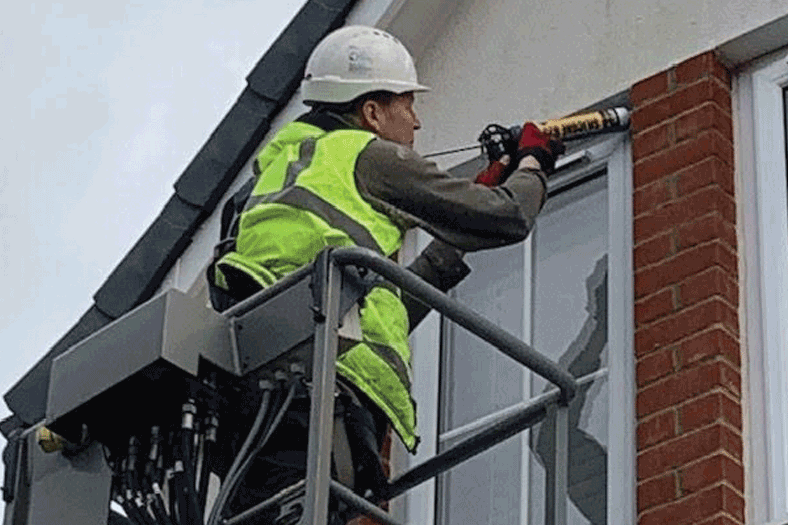
Modern buildings rely heavily on joint sealants to prevent water leak damage to their structures. If a joint sealant fails, there is little or no barrier to leakage. Unfortunately in today’s building environment, there are many points in the design and construction process where bad judgment results in sealant failure. Here are the following tips on how best to avoid these situations.
Most commonly, Joint sealers are used to close open joints to keep water and air out. Most rigid exterior substrates are purposely jointed, to allow movement without damage to the material. The two principal causes of movement are thermal expansion and contraction and seismic movement.
Exterior joints are many times made of different material combinations and as a result, seldom form a watertight joint without the addition of a sealer.
The principal exterior substrates that are sealed are:
- Exterior wall joints
- Door and window frame
- Concrete paving joint
- Metal flashings
- Roof joints
- Seismic movement joints
To avoid failures
- Choose the correct design
- Estimate the actual amount of movement
Building joints move in three different ways that affect the sealant in the joint: expansion, contraction, and shear
- Choose a sealant product that will withstand the movement expected
- Choose a sealant that will withstand the environmental conditions
- Specify the sealant product correctly
- Specify the scope and execution of sealant work completely.
ASTM C 1193 covers typical applications in great detail as help to the specifier.
Selecting products: Most joint leakage is caused by using the wrong sealant. Some sealant characteristics are critical to performance, others are arbitrary or user preferences.
To simplify the selection and specifying process, try the following techniques:
- Identify the exterior joints with the most extreme movement and select a sealant for them.
- Using the characteristics of the sealant selected, identify any other exterior joints that cannot be sealed with this sealant; assume all others will be sealed with this sealant.
- For those joints that cannot use the selected sealant, identify the factor that makes that sealant unsuitable and look for a substitute.
The sealant types which are most common are MS Polymer/Hybrid/Polyurethane, silicone, polysulfide, butyl rubber and acrylic latex.
The characteristics listed below are importance to performance of a sealant.
Consistency: Joint sealants come in two consistencies: non-sag and pourable. Vertical joints require non-sag sealants so the sealant will not run down out of the joint. Polysulfide sealants are usually available in both consistencies. Acrylic latex, butyl, solvent-based acrylic, and silicone are non-sag.
Continuous immersion durability: In a location where the sealant must be in contact with water at all times, use only products that are tested to ASTM C 1247. Polysulfide sealants are among the few varieties that are suitable for continuous immersion.
Suitability for exterior exposure: The qualifications for exterior exposure consist of low-temperature resistance, UV and ozone resistance, and heat-aging resistance.
Suitability for traffic exposure: Sealants subject to vehicular and pedestrian traffic need to have a certain hardness to resist puncture and tearing. Mildew resistance: For “bathtub calk,” specify an Antifungal sealant specifically manufactured for mildew resistance.
Acceptable joint widths: Most elastomeric sealants are limited to joint widths between 6 mm and 32 mm. Some MS Polymer and polyurethanes are designed for wider joints. Polyisobutylene sealants are designed for very narrow joints with no movement at all.
Movement capability: This is the gauge of how much extension and compression the sealant can withstand without failing in adhesion and cohesion. It is measured as a +/- percentage of the joint width, tested to ASTM C 719. Movement capability over 25 percent is available mostly in Polysulfide, polyurethane and silicone sealants.
Adhesion: Suitability for a specific substrate usually comes down to adhesion. MS Polymer sealants generally have the best adhesion, Products tested to ASTM C 920 Use M (for masonry) have acceptable adhesion on the most common porous construction substrates, such as concrete, masonry, and stone.
Hardness: Hardness is mostly used to judge whether the sealer is suitable for traffic use; minimum and maximum values are specified in ASTM C 920. Porous substrate staining probability: Sealants can have chemical compounds which might leach or migrate, especially into a porous substrate such as stone. Elastomeric products tested to ASTM C 920 meet minimum nonstaining requirements.
Volatile compound emission: Volatile organic compounds (VOCs) in some sealants may evaporate easily into the air under normal conditions; VOC emissions from architectural joint sealants are regulated by states.
Cure type: All joint sealants cure (change from being of toothpaste consistency to being solid) except those that are intended never to cure for some specific reason. The cure type is relevant because it affects other characteristics, notably VOC emission and installation friendliness.
Expected service life: Service life is usually used to represent the longevity of the material under the conditions it was designed for. MS Polymer, Polysulfide and Silicones typically last 20 years or more.
Relative cost: It is usually false economy to scrimp on sealants, when you consider the cost of labour to remove failed sealant and install a replacement (and the effects of enduring leakage for an extended period before deciding to make the replacement).
For more details, contact:
Dr. Mohan Ravi,
Essrbond Sealants
mohan@essrbond.com
Website: www.essrbond.com
Cookie Consent
We use cookies to personalize your experience. By continuing to visit this website you agree to our Terms & Conditions, Privacy Policy and Cookie Policy.