Let’s talk about prestressed precast concrete
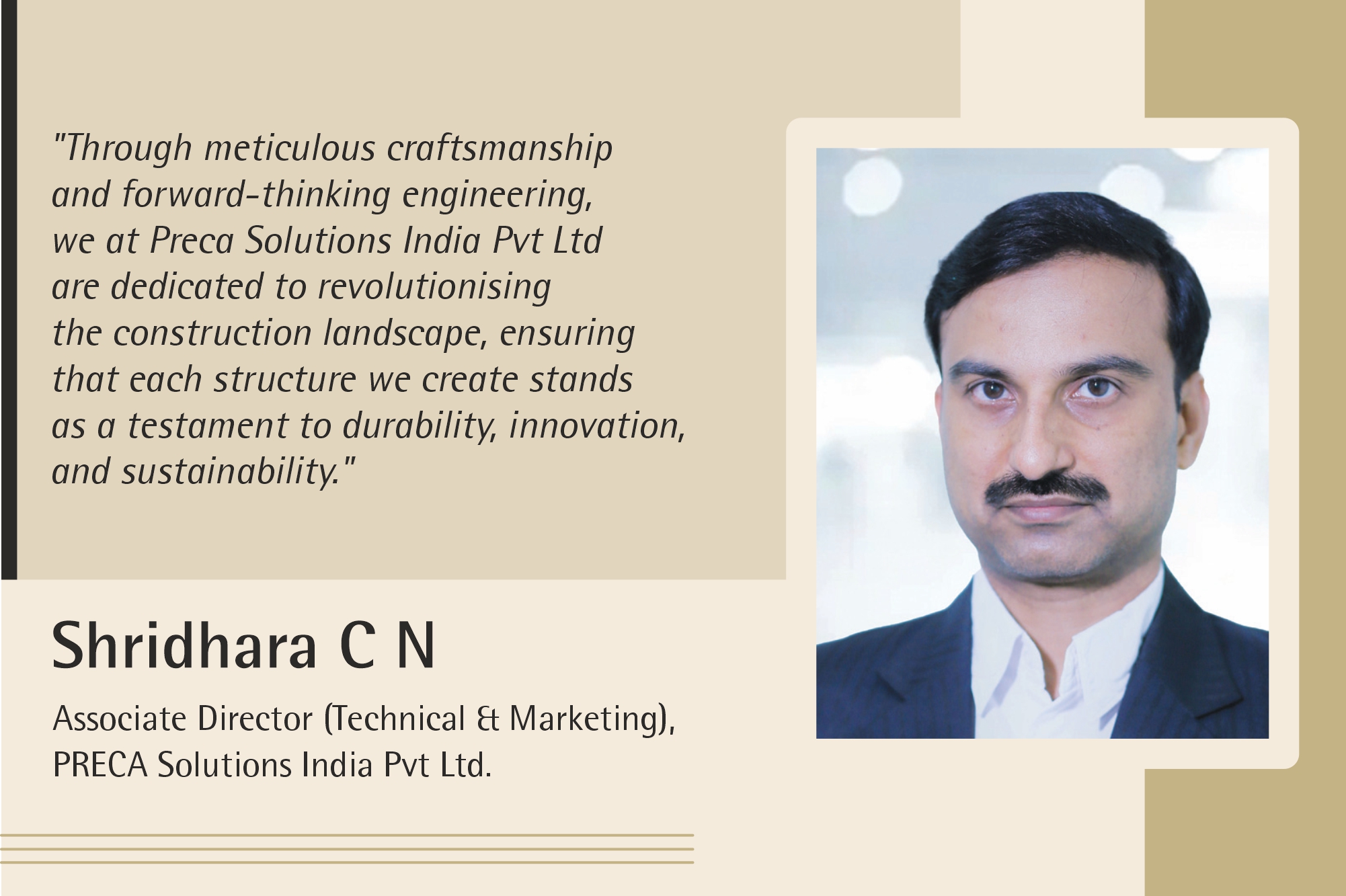
This interaction delves into the avant-garde precast prestressed concrete solutions offered by PRECA, unveiling the excellence, craftsmanship, and commitment to shaping a resilient tomorrow.
Could you describe the range of precast prestressed concrete products that Preca offers?
As a PRECA, we deliver a comprehensive range of precast prestressed elements in the international market. Our facilities allow for the production of building sectors using precast columns, wall panels, retaining walls, staircases, prestressed precast hollow-core slabs with thicknesses ranging from 120mm to 300mm, prestressed precast beams, precast prestressed solid slabs, and precast prestressed double T-slabs. Additionally, for infrastructure sectors, we provide precast trenches, drains, manholes, roads, water tanks, swimming pools, and lakes.
Can you shed some light on the advantages of precast prestressed concrete compared to traditional construction methods?
In precast prestressed technology, all elements are cast at the factory, not on-site. These elements are then brought to the site and connected to form the designed building. Prestressed methodology allows for longer spans with lesser depths, achieving more working spaces inside buildings. Casting elements in a controlled factory environment using sophisticated steel moulds ensures high-quality products. Precast factories conduct rigorous quality checks, utilising at least M40-grade concrete and sometimes even M50/M60 grades. All curing happens at the factory, eliminating the need for on-site curing and saving water resources. No plastering is required on top of precast prestressed elements, reducing the wastage of cement and sand. Adopting precast prestressed methodology minimises pollution, dust, construction sound, etc. Construction time is significantly reduced, saving 60 to 70 percent compared to traditional in-situ construction. Manpower usage on-site is reduced to 8 to 10 people, compared to 100 people in traditional in-situ construction.
What quality control measures does Preca have in place to ensure the reliability and durability of its precast prestressed concrete products?
Quality control is essential at all stages and precast processes. The quality team performs pre-pour and post-pour checks at the factory, monitors grouting works and connections on-site, and records all results in a standard checklist. The production and project teams work closely with the quality team, requiring quality approval to proceed from one stage to another in the construction process.
In what ways is Preca committed to sustainable practices in precast prestressed concrete construction?
Preca is committed to minimising the wastage of natural resources, such as water and other materials, and promotes using green products like fly ash/GGBS in concrete. The company adheres to planned schedules and timings to improve workforce health at factory and construction sites.
For more info visit: https://preca.in/
Cookie Consent
We use cookies to personalize your experience. By continuing to visit this website you agree to our Terms & Conditions, Privacy Policy and Cookie Policy.