The future of cement lies in sustainable practices
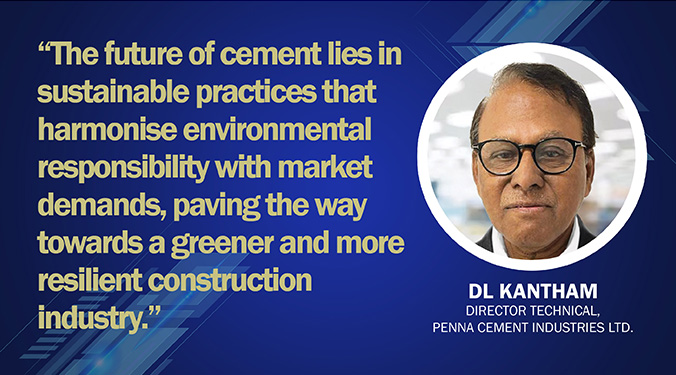
DL Kantham, Director- Technical of Penna Cement, talks about the difference between traditional and sustainable cement production.
How does the production of sustainable cement differ from traditional cement production?
Sustainable cement production differs from traditional cement production by incorporating practices that reduce environmental impact. One key aspect is the use of a lower clinker factor. Clinker, the primary ingredient in conventional cement, is associated with substantial carbon dioxide emissions. Sustainable cement production aims to decrease the reliance on cement clinker by incorporating alternative materials or processes. Additionally, sustainable cement production emphasises using lower energy inputs, both thermal and electrical, to minimise energy consumption. This approach also considers market requirements by ensuring better grindability, thus meeting the desired quality standards for sustainable cement. Overall, sustainable cement production strives to balance environmental considerations with market demands.
How does sustainable cement’s carbon footprint compare to traditional cement?
Sustainable cement’s carbon footprint is significantly lower than traditional cement. Compared to conventional cement production methods, sustainable cement production can reduce approximately 60 percent of carbon dioxide (CO2) emissions. This substantial decrease in CO2 emissions is primarily due to using a lower clinker factor in sustainable cement production. Sustainable cement significantly mitigates its environmental impact by reducing the clinker factor, a carbon-intensive component. This reduction in carbon footprint highlights the environmental benefits of adopting sustainable cement production practices and their contribution to combating climate change.
Are there any limitations or challenges to the widespread adoption of sustainable cement, and how can they be addressed?
The widespread adoption of sustainable cement faces certain limitations and challenges. The recent changes in the concrete industry, such as the rise of precast concrete and fast-track projects utilising techniques like MIVAN shuttering and monolithic concrete pour, have increased the demand for high early strength in concrete applications. Due to inherent reasons, sustainable cement falls short in meeting these requirements. Additionally, there is resistance to using sustainable cement in ready-mix concrete production in India.
Several actions can be taken to address these concerns. Firstly, the cement industry should develop rapid types of sustainable cement that meet the high early strength requirements, aligning with EN standards and other specifications. Secondly, the Bureau of Indian Standards (BIS) should consult with key stakeholders, including cement manufacturers, concrete manufacturers (including ready mix and precast products), chemical admixtures manufacturers, and project consultants, to develop specifications for additional types of sustainable cement like rapid types. Sufficient research and development efforts involving all stakeholders with a clear agenda and short timeframe can help establish the required specifications for enhanced sustainable cement consumption, specifically in segments like precast and ready mix concretes that demand high early strength. By addressing these current limitations, the adoption of sustainable cement can be improved and expanded.
for more info visit : https://www.pennacement.com/
Cookie Consent
We use cookies to personalize your experience. By continuing to visit this website you agree to our Terms & Conditions, Privacy Policy and Cookie Policy.