The precast concrete industry has been experimenting with the use of 3D printing technology
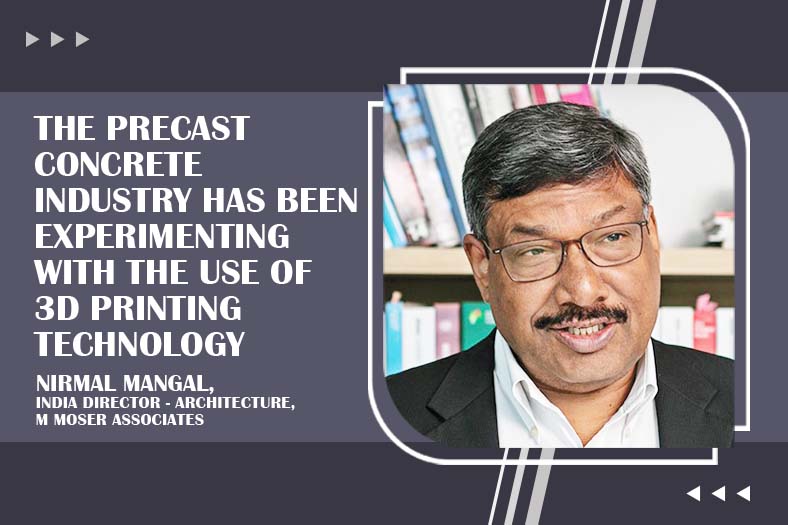
The typical 3D printing technology has been used for concrete walls, wall panels to 3D printed formwork says Nirmal Mangal, Director Architecture at M Moser Associates
Using form liners, how is it possible for precast concrete to assume different designs?
One of the latest innovation in precast industry is use of form liners to create almost unlimited range of colours, a very wide variety of patterns and textures. This finishes can range from sand blasted finish to acid etched finish to retarded façade treatment to expose aggregate matrix. The façade can incorporate any stone, brick, veneer or other façade materials. The form liners use urethane, plaster, rubber, grained wood, rope or other material as a liner in the casting form helps create finishes, reliefs, textures, shapes and patterns. The possibilities are limited only by the creativity of the design architect.
How is BIM changing precast concrete?
BIM Technology from Design to Construction: Precast manufactures are using BIM to convert models received from architects into precast components. The precast team details it to create an inclusive model that other trades can use for clash detection and incorporation of other services. Such collaboration minimizes site changes and design compromises.
More efficient project schedule aligned with construction sequence – On larger projects, the precast manufacturers are collaborating with the architect and construction managers to help define and optimize the project schedule and construction sequence. Since the construction sequence of precast concrete buildings is different, early planning of project schedule and sequence is important to best optimize the project schedule.
The use of BIM has changed the shop drawing review and change management process. The precast manufacturers along with other trade contractors start with a BIM model hosted on the cloud and provided by the design team. All development and detailing of the BIM model are automatically seen by the entire construction team. It allows the design team along with all trades to review and provide their input and feedback. The shop drawings are well-coordinated and minimizes site driven changes.
Similarly, BIM also helps in the change management process by modelling the effect and scope of potential changes. The effect of potential changes can also be quickly assessed by the precast team where the model is linked with precast manufacturing and project schedule.
BIM interface for precast erection/rigging sequence and installation schedule: Precast erection and rigging schedule drives the sequence of precast component manufacturing sequence. Often, the precast components are manufactured based on the Just in Time (JIT) methodology because of limited site logistic area. Using BIM, in collaboration with the architect and Construction Manager can agree on precast erecting sequence, and resources and equipment needed for rigging precast components.
How is 3D printing helping precast in offering custom designed solutions? Can you cite some national or international examples?
The precast concrete industry has been experimenting the use of 3D printing technology. The typical 3D printing technology has been used for concrete walls, wall panels to 3D printed formwork. There are a number of projects in the USA and EMEA where 3D wall technologies have been used in a variety of applications. Following are some example of 3D printing technology in precast industry for customized design solutions:
3D Printing of Wall Panels – A number of firms in USA and EMEA are manufacturing wall panels a variety of design options using 3D printing technology. They include choices of façade material and finishes and provision of building services.
3D Printed Formwork – One of the latest innovations in precast industry is to address problem of breakdown of form work. For projects requiring limited number of precast façade elements, the traditional method of wood formwork is appropriate and cost efficient. However, when a larger number of precast façade elements are required, 3D printed formwork provides uniform and faster manufacturing of formwork for precast industry.
What kind of automation is being witnessed in precast plants to make the process less labour intensive?
The precast industry concrete industry has been very enthusiastic about adopting automation in their plants. Automation in precast industry is very expensive and most precast manufacturing equipment are customized solutions. However, the industry has been looking for ways to address the problem of skilled labour shortage, Automation is making precast plants more efficient, more consistent, safer and less labour intensive. Some of the considerations were to decrease safety risks and health hazards associated with silica dust, noise, strains and sprains – as well as attracting future skilled labour.
The precast concrete product range has included floors slabs, precast beams and columns, solid walls, double walls and exterior façade elements. A full range of automation in precast industry includes circulation lines, stationary production lanes, production equipment, curing chambers, storage systems and tilting stations etc.
25
Cookie Consent
We use cookies to personalize your experience. By continuing to visit this website you agree to our Terms & Conditions, Privacy Policy and Cookie Policy.