3D Printing set to revolutionise construction industry
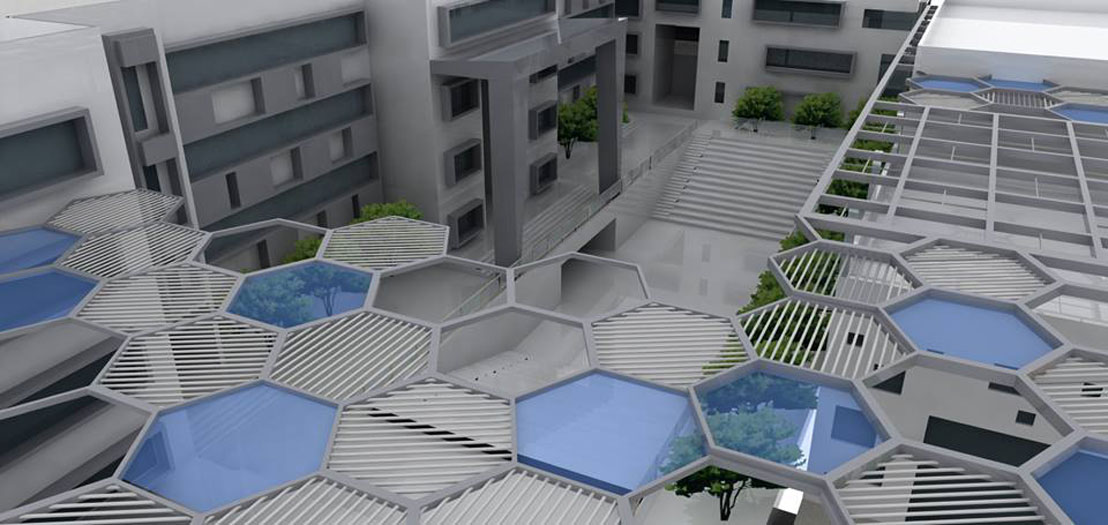
Future building materials will take their cue from current scientific technologies.
Drone Surveying and 3D Concrete Printing
The act of building is a basic component of human activity. For centuries, humans have created structures, beginning with the simplest of huts to the most modern of skyscrapers. As per Vibhor Mukul Singh, Principal Architect & Proprietor, Designers’ Alcove for Art & Architecture 2016 has brought some great advances in technology for the architecture, engineering, and construction industry. From new survey methodologies to building techniques, there were many noteworthy milestones. “The two most remarkable ones that I can think of right away are – Drone Surveying and 3D Concrete Printing,” he states.
He adds, “It seems that 2016 was the year of ‘drone technology’—small, remotely operated multiple-rotor aircraft. There’s no end to what these versatile devices can accomplish. Now drones have come to the construction industry, and they are promising a revolution in surveying of our world. Armed with high-resolution digital cameras and advanced software, these little aircraft are set to take surveying to new heights.”
Similarly, concrete has been a building material of choice for some of the greatest construction projects in the world. “Now 3D Printing technology is being integrated to produce complex building forms. This union has the potential to reduce the time required to produce such components by several orders of magnitude – from weeks to mere hours,” he notes.
How 3D Printing is adding value
Extremely large 3D Printers have already been built that can use concrete-like materials to fabricate a variety of large structural components and even entire buildings, such as emergency huts and residences.
Explaining on how this technology added value to the profession of architecture, Singh says, “Raw materials tested include recycled plastic, bioplastics, concrete, synthetic stone-like material made of sand and chemicals. Most printers can only extrude one type of material at a time, but more advanced printers have been built that can extrude multiple materials, providing a level of speed and flexibility that was not present before.”
He adds, “The printers may fabricate wall sections that snap together like Legos onsite or they may print structural scaffolding that can be filled to create full-size walls. Reinforced concrete beams have already been fabricated using a 3D Printer.”
It’s thought that components can be printed offsite and shipped to the jobsite where they will be erected with steel reinforcement. Alternatively, the printer can be transported to a jobsite to fabricate on demand.
The benefits of 3D Printing are such that it reduces materials usage and increasing the ability to design a larger variety of customised homes and buildings. 3D Printing saves 30-60 per cent of construction waste. It also cuts down production time by 50-70 per cent and reduces construction labour costs by 50-80 per cent.
Building designers will escape some of the constraints of current construction methods. For instance, 3D Printing makes curvilinear construction practical; no longer will designs be limited by cost and process to rectangular forms.
Being able to use round shapes will impart more strength and stability to the structure because curvilinear shapes are some of the strongest while rectilinear shapes are some of the weakest of structures.
“In addition to being stronger, curvilinear design will require a minimum of material to create shapes with a consistent curve. Another benefit is that structures can be designed and printed with hollow components for the easy insertion of service utilities like electricity and plumbing,” he informs.
Acceptance of 3D Printing in architectural construction
3D Printing technology has been developed to the point where full sized testing can be accomplished. However it is going to require a high initial capital investment to build more and larger printers. Right now there are few in existence, informs Singh.
The ‘Big Delta’ printer in Italy has been used for the World’s Advanced Saving Projects (WASP) program. This printer is capable of producing a complete shelter using mud, clay, and natural fibers. The hope is to print emergency housing in areas struck by disaster. Similarly, Berok Khoshnevis, a researcher at the University of Southern California, is testing a fabrication process called contour crafting. This is a method that could automate the construction of complete structures as well as sub-components. With contour crafting, Khoshnevis hopes to print an entire building, such as a house, in a single print run. It would include conduits for electrical, plumbing, drywall, and insulation. Khoshnevis thinks it realistic to expect widespread use in the residential market by 2020 and for high rise construction by 2025.
However, on the adoption of 3D Printing technology Singh observes, “Due to the high cost of the printers and the lack of experienced operators and designers, 3D Printing is still substantially more
expensive than traditional construction. The upfront costs are also high for designing a safe, cost-effective building.”
Future of construction industry is bright
Singh feels that the future of construction industry seems brighter than ever. Besides providing various jobs to those seeking careers in this field, evolving techniques have enabled different living options for people to better suit their styles and preferences. As more and more buildings in major cities are being built, the industry is also keeping in track with the latest technologies to better improve the quality of buildings, geared towards the future of man’s day-to-day living through sustainable construction practices.
“When it comes to construction technologies, the possibilities are endless, and the current rapid innovation and technology of construction will shape the appearance of future buildings. Future building materials will take their cue from current scientific technologies,” believes Singh.
As an example, a self-healing concrete, developed by microbiologist HenkJonkers and Eric Schlangen, a concrete technologist, involves the genus Bacillus’ mixed bacteria spores. Its nutrients, when activated by water, will feed on calcium lactate to produce a primary component of limestone, which is lactite. This self-healing concrete may be available within the next few years if tests are successful. Once proven, it could eliminate concrete cracks and expensive concrete maintenance.
Alongside and influencing these technologies is a greater awareness and need to build greener, with sustainable materials used at the construction phase. While it may be easier to stick to familiar construction methods, the industry is changing and the new, innovative greener techniques, while challenging to develop to the point that they become standard, can be highly beneficial to the quality of the urban environment, and often ingenious.
Cookie Consent
We use cookies to personalize your experience. By continuing to visit this website you agree to our Terms & Conditions, Privacy Policy and Cookie Policy.