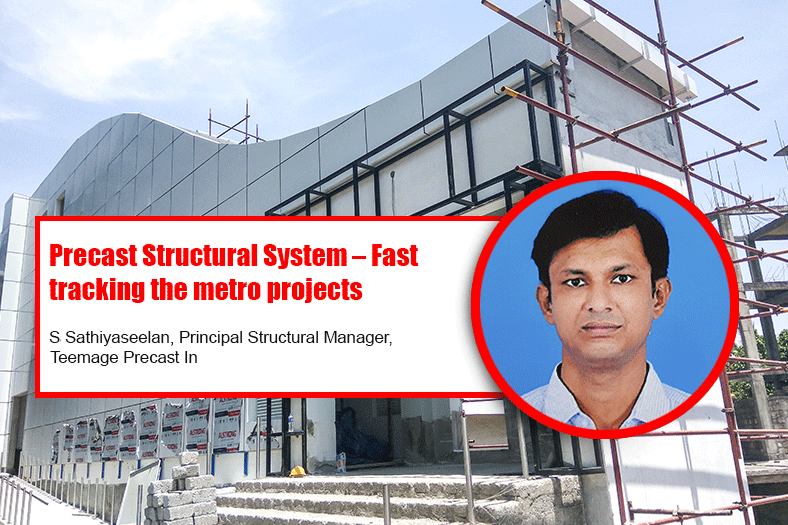
It is essential to understand that infrastructure projects, especially the ones being designed for the masses need to be completed on time. In this entire gambit, the role of precast becomes very important says S Sathiyaseelan, Principal Structural Manager, Teemage Precast In.
What are your thoughts on the ongoing metro projects?
Given the high population density, it is increasingly been accepted by the policy makers that Mass Transport System (MTS) is inevitable and is the need of the hour to cater to the growing traffic demand. Among the available options, Metro rail projects have yielded good results in terms of addressing the people traffic volume and time. Hence, the said system is being adopted in all major cities.
What is the existing method of construction system opted for the ongoing metro projects?
In any typical metro project planning, among various factors, timeline and extent of disturbance to the existing traffic forms one of the key factors. These factors made the ‘shift’ towards precast construction system, an inevitable one and hence almost all the track way deck structures are made with precast elements, which are cast at dedicated precast factory setup established nearby.
Presently, in most of the projects, the column piers and pier caps are been made in conventional cast in-situ system while the decks are made out of precast, casted elsewhere and transported to site and are launched using a dedicated launching system. In addition to above, all the station buildings are made using conventional cast in-situ which often results in delay while the track corridors are readied faster owing to its dedicated precast system via deck construction.
The main reason for adopting conventional system particularly for station buildings involving shear wall and framed structure is due to lack of technology, machineries & expertise in the areas of design, production, logistics and erection of precast elements which reduce both, time and project cost.
How is the precast technology being utilized successfully for the Kochi Metro project?
Six station buildings of Cochin Metro have been constructed successfully using precast technique.
Staircases
Most of the station buildings comprises of wide stairs, spanning over multiple floors which forms one of the major portion of the project. This has been erected in a single day for each floor thereby making the structure look like a complete one. Thanks to precast technology otherwise this is the most difficult and time consuming part if the conventional system is utilized. This speedy erection of stairs in turn gave easy access to its upper floor for carrying out further activities immediately thereby catalysing the construction process.
Frames – Columns and Beams & Slab system
Being located in high seismic zone, the frames are designed and detailed for seismic zone IV and the respective joints are made with special detailing to withstand the increased earthquake force. In this project, Solid column – Trough beam system is employed to achieve the said seismic strength and ductility with reduced time. Most importantly the structural joints are planned and designed such that precast beams & columns are made to address the load independently thereby making the erection of subsequent elements without ‘wait’ time for joint filling of element interface with high strength grout.
Similarly, joints are planned in such a way that the slab system, composed of hollow core elements, each of 1200 mm width, are erected immediately after beam and column erection without the need to wait for the beam trough portion to be filled with concrete. Hence, by proper design and detailing of precast elements and joints, the time is controlled without compromising the strength and durability.
Structural finishing
The construction of stair and slabs ensured that the electrical work for each floors continues unhindered, likewise it also facilitated the errection of additional precast elements required. The use of precast also eliminated the need for scaffolding since the outer wall was smooth and ready for painting purpose. All this helped in reducing the project construction time considerably.
At the outset, Precast is thus a viable and profitable option since it accelerates timely project construction, reduced labour engagement, high structural strength and durability.
Cookie Consent
We use cookies to personalize your experience. By continuing to visit this website you agree to our Terms & Conditions, Privacy Policy and Cookie Policy.