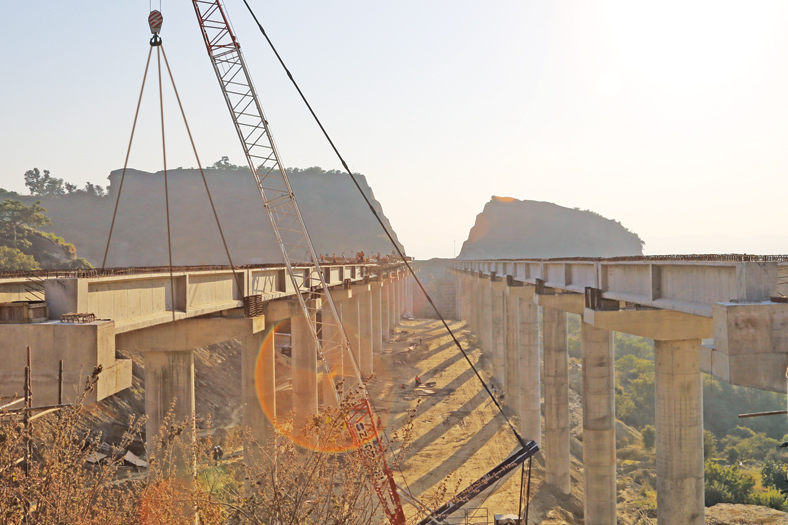
How precast technology can speed up construction
Precast technology is gaining popularity on faster bases as it allows the developers to standardise quality and build faster. Due to qualities like faster development, time saving, cost-effective it has become priority in the construction industry. On the other hand, government’s agenda of ‘Housing for All’ is developing on a rapid note and to accomplish this mission precast could be the ultimate answer to India’s mass housing needs. To understand how precast technology helps speed up construction and how will it build infrastructures, houses etc in short span of time we bring an exclusive feature on the same.
One important aspect of construction is speed which translates to time saved (cost saved). “Using precast technology is a proven method of cutting down construction time by over 50 per cent. Theory of constraints has a good application in precast technology, where offsite manufacturing of building elements, help crash the critical path of construction,” states Chander Dutta, Managing Director, Elematic India Pvt Ltd.
In addition to time, by choosing the right structural system and design, you can bring in material saving of 10 to 15 per cent in concrete and steel used. “Precast construction uses concrete, the most versatile and low cost material known to mankind. The only way to construct large fast track building projects is by utilising technology and precast technology is widely used all over the world for the reason that it’s mechanised way of construction, offers high quality and durability,” adds Dutta.
Elematic is a Finland based company, has foot print in more than 100 countries and can offer end to end services for execution of construction using precast technology.
Precast concrete is an age-old and age-tested methodology of construction all over the world. After a quiet start few decades ago, slowly, people are again exploring this option. The prime reason, interesting for the client’s higher management to consider being, earlier ROI for fast track projects, believes Kapilesh Ajit Bhate, Chief Coordinating Officer, Precast India Infrastructures Pvt. Ltd. (PIIPL).
While citing an example Bhate explains, “PIIPL has the pride in citing their own live examples, whereby we have completed 2 projects in the commercial heart-land of Pune having lease square footage of around 6L sq. ft. each (so 12L sq. ft. for both projects) and we completed the 6L sq. ft. RCC work in 6 to 7 months each. So, if a core developer is getting his leaseble/saleable product in 40-50 per cent of the time (compared to conventional CIS), his inbound cash flow can start that much earlier (once, and provided, the finishing works are done with equal pace, coordination and intensity). The amount of early cash flow may come back in tunes of crore, depending on the lease/ sale rate per sq. ft. having other interest-saving effects in the overall project finances in totality. Same applies for Production facilities in urgent need to start production and supply (sale).”
Another reason, needless to mention, is the quality control which is possible in a manufacturing environment as opposed to site concreting.
Bhate emphasised, “Precast technology is extremely technically challenging, which needs lot of pre-engineering and fast decision making from all professionals involved, like client, architect, service consultants and of course structural design teams, but which, if handled by a professional and technically sound precaster, is a phase not taking more than 2-3 months. The client, thus, having completed all his major decisions regarding building systems, can be sure of the project budget right in the 3rd or 4th month, which is a luxury for any top management, as opposed to approving and recapping limits throughout the project’s timeline.”
To conclude, a fast track project with just enough time to pre-engineer the coordination and which requires a high quality standard spells precast, and PIIPL is glad to cite many such examples.
In a typical project the least time given by owner is on construction and after award everyone is concerned about completion. On site work has its own constraints like statuary clearances, insitu construction cycle, climatic challenges. Festivals and unscheduled absence of skilled and unskilled manpower at site, quality and safety issues, local issues like hindrances from the land owners , authorities etc. It is a great challenge for project manager to maintain the schedule of the project.
Off site construction methods come to rescue by providing unhindered work in factory where elements can be manufactured with least challenges. In this all elements are produced in factory and minimum work is done at site.
“High performance precast concrete can help maintain a project schedule through speed in design, construction and finishing processes,” states Suresh C Tripathi, Vice President Tech – Supertech Precast Technologies Ltd.
Working with a precaster early in the design process can help the designer choose the most efficient elements type to cast, saving both time and money. For example, for the Supertech’s Golf Village Project on Yamuna expressway project we used Hollow core prestressed slab as roof and floor panel and precast wall panel as shear wall. This helped the design work to move quickly to the shop drawing stage.
He adds, “Once designs are approved, the precast elements can be cast in the plant, under factory-controlled environment, parallely the construction site is being prepared for receiving the elements. As these elements are manufactured in the plant, climatic challenges of bad weather are not a concern.”
The engineering and manufacturing precision produces exact dimensions, which is not possible in cast in situ construction. Electrical conduit can even be embedded in the panels at casting. (This eliminates one cycle of work at site) once produced, precast can be scheduled and delivered to a project site based on need. Components can be installed quickly, oftentimes shortening a schedule by weeks or even months.
For example, for the Supertech’s Golf Village project the company had planned for a 11,000 sq.ft. of floor plate area in a time cycle of 15 days this included erection of all wall panel, hollow core floor slabs, putting MEP conduits over floor and screeding the same after tying the nominal rebar as per drawings. At the end of tower construction Supertech could do this in 13-day cycle.
Supertech has set up two separate units in this factory – one for hollow core slab (prestressed) and the other for mechanised precast wall panel’s production. All the machines and units required to execute the process of production has been imported from Germany and Belgium.
Further Tripathi informs, “We are already doing 20 plus (3 basement) storeyed precast towers (hollow core and shear-wall combination) on Yamuna expressway which is highest precast structural building in NCR. Apart from our own group companies we are also doing precasting works for other clients like Shapoorji, Tata Projects, Alstom, Arabtech etc.”
Shridhara C N, Head-Technical & Marketing, Preca Solutions shares few qualities of precast that help in speeding up the construction.
Quality
Precast technology, by virtue of the industrial process involvement of casting under controlled circumstances, adheres to the highest standards of quality control.
Speed and Strength
Precast concrete construction does jobs sooner. Depending on size and site conditions, flooring for a number of units can be laid in a single day. Use of higher grade concrete and steel, than conventional, makes it structurally superior.
Easy installation
Precast concrete products are arrive on-site ready to be installed and require minimum manpower to do so. Installation is quick and accurate, making the process more efficient and effective.
Long spans
Pre-stressing allows for casting elements longer than those achievable by conventional systems. A typical 300 mm hollow core slab can span up to 16 m and T slabs up to 22m without intermediate columns and beams.
17
Cookie Consent
We use cookies to personalize your experience. By continuing to visit this website you agree to our Terms & Conditions, Privacy Policy and Cookie Policy.