PERI has consistently addressed complex challenges involved in metro projects
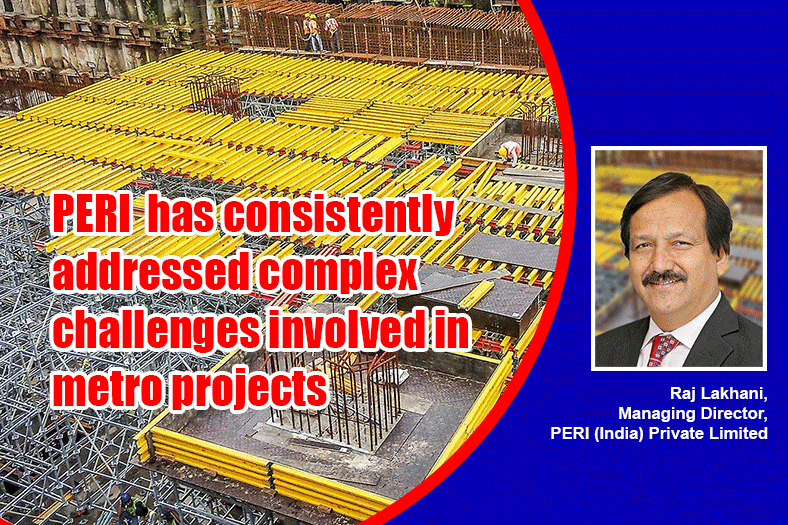
Hyderabad Metro, Mumbai Metro, Bengaluru metro, Mumbai Trans Harbour Link (MTHL), Lucknow metro are some of the projects which have utilised our state-of-art formwork and scaffolding system says Raj Lakhani, Managing Director – PERI (India) Private Limited.
When it comes to ongoing metro railway projects, they are either overhead or underground, keeping this in mind, what kind of formwork solutions are required?
PERI India has been growing its footprints in the infrastructure & real estate sector in India. With landmark Infrastructure projects such as Mahatma Mandir, Statue of Unity, Agra[1]Lucknow Expressway, Hyderabad Metro, Mumbai Metro, Bengaluru metro, Mumbai Trans Harbour Link (MTHL), Lucknow metro using our state-of-art formwork and scaffolding system, we have proved our mettle in delivering customized solutions for every complex need in a cost-effective manner. The Bandra Kurla Complex (BKC) metro station is one such recent project. It is an underground station on the Mumbai Metro, a rapid transit system that is currently under construction. The rapid transit system in the Indian metropolis will serve the city of Mumbai itself as well as its entire metropolitan area in the state of Maharashtra.
By supplying comprehensive formwork and scaffolding solutions, PERI has been providing assistance since construction began on the major project in April 2019 so that the BKC can be completed within the demanding construction timeline. The Bandra Kurla Complex (BKC) is located on the section of the 33.5-kilometre-long Colaba-Bandra-SEEPZ line (also known as line 3) that connects the Cuffe Parade business district in the extreme south of the city to the Santacruz Electronics Export Processing Zone (SEEPZ) and the Aarey in the north. Upon completion, the BKC will act as an extremely important hub for passengers looking to change swiftly to line 2. The BKC will be the largest underground station on the Asian continent.
What were some of the complex challenges involved in this underground construction?
The 475-m-long and 30-m-wide underground station consists of two subterranean levels. The first level is 8.4 m high, ending with a 750-mm-thick slab. The second level is 5.5 m high and ends with a 1,200-mm-thick floor. Since all loads acting on the slabs are transferred directly into the columns, approximately 1450-mm-thick drop panels were used between the columns and the slabs. Concreting the retaining walls was the first challenge that the construction team faced due to the fact that it was impossible to absorb the horizontal fresh concrete pressure on the wall formwork using formwork ties on account of the subterranean position up against the ground earth. What was required was a singlesided formwork solution that could also cover the surface of the 24-m-long and 4.5-m-high concreting sections at a single pour.
Constructing retaining walls at a depth of around 16 metres
PERI came up with a special-purpose solution that ensured that the retaining walls could be constructed in only a single cast and in the sectional dimensions required: the single-sided SCS Climbing System in combination with the LIWA Panel Formwork. With the aid of the SCS Climbing System for non-tied wall formwork, it was possible to transfer the loads resulting from the fresh concrete pressure through climbing ties and into the previous concreting section via the brackets. In this way, it was possible to stick to the demanding concreting cycle of only 25 to 30 days that had been stipulated.
The LIWA Panel Formwork was also used at the construction site in Mumbai for the construction of the 8.4-m-high columns. This system formwork stands out not only due to its low weight but also on account of its integrated perforated strip. This allowed the construction site team to use the elements in a multi-purpose manner. For example, it was possible to form the columns in a single operation and without the use of any special-purpose components. Opting for the LIWA system instead of a conventional formwork system resulted in valuable time savings and a significant reduction in personnel costs.
What are some of the other products this project utilises some more products from PERI’s stable?
The construction site team came up against another challenge when it came to constructing the 750-mm-thick slab area and the 1,200-mm thick roof floor covering 24 m x 32 m single pour plan area. The solution came in the form of the height-adaptable table support PERI UP Flex Shoring Tower Plus. With the aid of standards and horizontal ledgers of the modular scaffold PERI UP Flex and a few additional components, it was possible to erect shoring that was ideally suited to slab tables. It was also possible to adjust the positions of the standards so that they were perfectly equipped to deal with the loads to be transferred, with each standard being able to absorb a maximum load of 40 kN.
To form the slabs, TABLE MODULE VT Slab Table was used in combination with VT 20K Formwork Girders, which stand out due to their high cost-effectiveness. The large-scale formwork areas of the slab tables were moved quickly and easily by crane and movable trolley. The slab tables were pre-assembled at site, meaning they were ready for use in no time at all, thus contributing to the smooth execution of the time-critical construction schedule.
What are on-site support you offer for such large scale infrastructure projects?
PERI has delivered around 480 tonnes of formwork and scaffolding material to the client’s construction site. The planning and construction engineers from PERI have also been on hand to support and train the construction site team throughout the entire process to ensure that the major construction project is completed within the scheduled construction period.
38
Cookie Consent
We use cookies to personalize your experience. By continuing to visit this website you agree to our Terms & Conditions, Privacy Policy and Cookie Policy.