Prefabrication: The Future of Construction in India
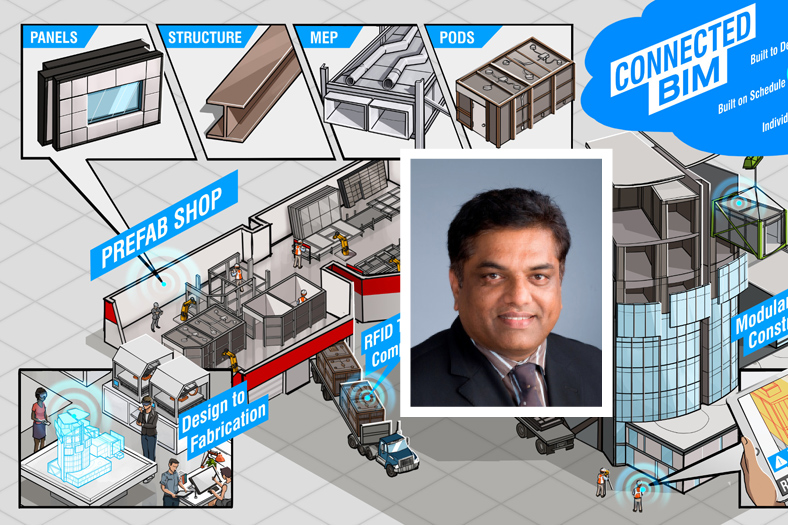
“Prefabrication will be a key enabler in mission “Digital India” and play a vital role in all infrastructural development.”
‘Building it brick by brick’ to ‘build it before you build it’, transformative technologies being led primarily by Prefabrication are now beginning to blur lines between the construction and manufacturing sectors in India. Slated to have the world’s third largest construction industry by 2025, India is witnessing a high uptake of modular techniques with its construction sector slowly transforming and behaving more like the business of manufacturing.
The last two decades are testament to the fact that from Supercomputing to Space and Pharma to Biotech, India has always taken the lead to brace innovation and tech adoption be it any sector or industry. Today, the way things are being made is causing widescale disruption across industries including construction of buildings and infrastructure – Future of Manufacturing Things (FoMT). Riding the prefabrication wave and clocking a CAGR of 7-8 per cent, the Indian construction sector today stands at the threshold of a huge opportunity to leapfrog into FoMT and prefabrication or modular construction remain at the heart of it.
Process of Manufacturing Buildings
As a manufacturing process, Prefabrication is a method of construction that includes assembling components of a structure at a separate production site and then transporting complete or partial assemblies to the actual site where the structure is being constructed. It is basically a combination of superior design with modern high-performance components and quality-controlled manufacturing procedures. Therefore, prefabrication not just ensures faster completion of a project but also brings down its overall cost. From residential high rises in New York to low cost hotels in Europe, Prefabrication allows engineers to blur lines between design and manufacturing process and create products for the future. Over the next few years, India would feature amongst the fastest-growing countries in terms of construction output, making technology intervention a key component of this.
Barriers & Challenges in Adoption of Prefab
Globally, prefabrication has already seen significant adoption by the construction sector – Burj Khalifa in Dubai and the Sydney Opera House being two of the finest examples. According to a report published by Technavio, a global technology research and advisory firm, the global prefabricated construction market is expected to grow at a CAGR of 6-7 per cent until 2020. However, in India the uptake of modular technologies continues to remain slow and prefabricated buildings comprise only 1 per cent of India’s $100 Billion Real Estate Market. The main reason for this being that Prefabrication as a technology is still battling a mindset blockade in India, with most developers averse to investing in modular methods of construction and hesitant to incorporate prefabrication in their new and ongoing projects.
The Indian construction marketplace today stands plagued by constricted space, overcrowding, delay in completion and clearance snarls. In addition to this the sector continues to be labour intensive and heavily reliant on traditional construction practices. While, upfront the cost of switching over to prefab is a lot higher but in the long term it is prefabrication that can give developers the benefit of time, safety and quality, enabling them to churn out buildings faster and capture the demand.
Rise of BIM, Green Buildings and Lean Construction
The surge of prefab and modular as a ‘trend’ is significantly tied to the rise of advanced technology platforms such as Building Information Modelling – BIM. The application of BIM in prefabricated construction has multiple benefits – while it helps to ease the design flow it also provides data-centric information based on design, specification and construction issues. Additionally, BIM can also enable developers to track time, errors, and cost. Also, the industry recognizes contribution of modular technologies in meeting green goals. Apart from waste reduction benefits, working off-site reduces habitat and site disturbance; protects raw materials from rain and extreme weather contributing to the development of a more adaptive building. Similarly, lean construction, the new buzzword these days mainly focusses on eliminating waste, leading to significant savings in both schedules and budgets.
Confluence of Manufacturing and Construction
The uptake of transformative technologies was slow in the initial years as majority of tech innovation was focused on manufacturing construction equipment but over the last few years it is the process of construction and design that has become the focal point. It is now officially the age of manufactured buildings where constructing 3 floors a day or 57 floors in 19 days as built by China’s Broad Sustainable Building (BSB) company is no longer an aspirational feat but a target easily achievable.
Most of the delay in construction happens at Stage – 1 due to faulty design. 3D Printing and designing everything on the cloud takes care of that problem with most of the iteration happening on the cloud itself. Big data and cloud computing are expected to have an immense impact on the design and management of construction projects. More frequent use of 3D printing technology, increased applications coupled with various kinds of materials and project types could completely change the process of physical delivery in coming years.
The next decade belongs to prefabrication with the Indian construction sector expected to expand to a size of $1 trillion and contribute over 15 per cent to the overall GDP. The government’s ambitious project of building 20 million affordable houses and 98 smart cities by 2022 will see the construction and manufacturing industries confluence further to create an ecosystem for increased innovation and technology adoption. Thus, prefabrication will be a key enabler in mission “Digital India” and play a vital role in all infrastructural development.
Authored by:
Sunil MK, Head AEC,
Autodesk India and SAARC
262
Cookie Consent
We use cookies to personalize your experience. By continuing to visit this website you agree to our Terms & Conditions, Privacy Policy and Cookie Policy.