Technological advancements disrupting the global construction industry
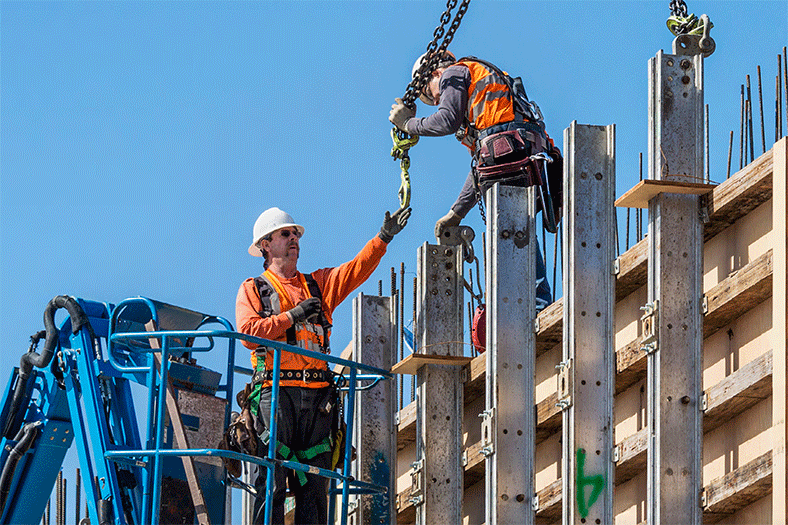
This comprehensive study has been co-authored by Eric Ottinger, Harshit Minglani and Mark Gibson FRICS Ernst & Young LLP.
Global construction trends and technological advancements
The world’s rapid transformation from manual processes to digital technologies is empowering the construction industry. Construction companies are now provided with unprecedented levels of transparency, choice and convenience. With enhanced capabilities, there is an increased demand for higher quality, greater safety and timely completion of projects. This influx of technological solutions is mitigating risks and streamlining the building production process. Digital innovations and megatrends continue to evolve and shape the future of the construction industry.
This research provides a high-level overview of the technology landscape and potential future state of the construction industry. It is the first of a series of papers that will focus on three core areas identified herein: 1 Design oriented digital technologies 2 Industrialized and componentized construction advances 3 Construction automation — supporting work through digitization Realizing the demand IT and software companies have recognized a demand for digitization in the construction industry and are expanding their software offerings to include solutions tailored for many processes. There have been several innovative construction technologies introduced in the last decade, including building information modeling (BIM), project control and scheduling software.
Sensors, cameras and drones are being used to monitor project progress and create smarter buildings. Automation is to be found in almost every repetitive process and the industry is seeing a resurgence in industrial manufacturing in order to compensate for declining on-site construction productivity. These evolving technologies have directly impacted construction activities throughout the value chain. Field labor is becoming more productive, project management is having greater oversight and executive staff are obtaining better transparency and reporting. Consequently, as the economy has experienced expansion in the last few years, the construction sector has regained its momentum since the great recession, driven by increased demand for infrastructure and real estate developments. Incorporating and expanding on these technologies allows for more intelligent planning of construction, supply chain management and delivery.
The construction industry is experiencing technological innovations throughout the project lifecycle, with internet of things (IoT) leading at the forefront. In 2019, the IoT industry was estimated at approximately $270B and is expected to grow at a 26% compound annual growth rate (CAGR) for the forecasted period through 2025.1 3D printing currently holds the smallest market share of the construction industry, however is expected substantial growth at 245.9% CAGR.2 Other technologies, such as blockchain, artificial intelligence (AI) and robotics are also expected to contribute to this growth, at greater than an estimated 30% CAGR. Full-scale digitization may help escalate the construction sector and generate an estimated 12-20% in annual cost savings within a decade.
Design oriented digital technologies
Building information modeling (BIM) Utilizing BIM has become the most commonly used technology in the construction industry, from design through project completion and operation. 73% of US contractors surveyed by Dodge Data & Analytics reported utilizing BIM, with 79% of those using it on more than 30% of their projects.9 BIM is the process and digital representation used for modeling and management of the physical and functional characteristics of a construction project or facility. It is a shared knowledge resource for information about a facility, forming a reliable basis for decisions during its life-cycle; with the possibility of existing from earliest conception to decommissioning.10 BIM can be applied to create 3D models, and has evolved to additional dimensions, including schedule (4D), cost estimating (5D), sustainability (6D) and operations maintenance (7D).
It affords a number of benefits, such as more effective design, enhanced coordination, a reduction in change orders and a more efficient construction process overall. During design and construction, BIM offers savings in cost and time, gains in accuracy and reduction in errors and rework. The estimated savings of total project cost using BIM is typically between 4% to 6%.10 Critical information can be input to the digital BIM at the earliest phases of design and planning. BIM allows engineers to easily analyze alternative scenarios and visualize the entire planned sequence of the project. This limits waste and allows products to be delivered closer to a just-in-time model rather than being stock piled onsite. Because of this, BIM can directly compliment prefab design, supply chain management and project installation by allowing owners and contractors to identify impacts to multiple project elements. As the dimensions of BIM have evolved, it has become a critical input to digital twins.
Digital twin
One of the latest trends in the construction industry is creation of a digital twin to enable simulation and predictive analytics. The digital twin enables convergence of the physical and virtual world, where every process, product or service is represented by producing a digital replica of a physical asset or living entity.
This allows analysis of data and monitoring of systems to identify and resolve problems before they occur, prevent downtime, develop new opportunities and plan for the future by utilizing simulations. By reconstructing an as-built state of a structure in BIM, we can then compare it to as-planned execution and take corresponding actions to correct any deviations. Digital twin building simulations can be used to assess the energy demand, indoor environmental quality, carbon emissions and payback periods of energy management systems over the lifetime of an asset. Once the building is operational, a digital twin can notify the user of maintenance malfunctions, such as a light going out in a fire stairwell. The manager can then check the visual representation to locate the exact positioning of the bulb and the best access route. Strategic benefits will also include automated progress monitoring, facilities management, root cause analysis, intelligent recommendations, self-tuning, predictive maintenance, 3D databases of reflective virtual asset information, data collection for AI systems, data storage and historical recall.
Augmented and virtual reality
Technologies like augmented reality (AR) and virtual reality (VR) have enabled construction companies, investors and customers to visualize elements of the design, build and post-construction phases of their projects. AR is a live, direct or indirect view of a physical, real-world environment whose elements are ‘augmented’ by computer-generated sensory input, such as sound, video, graphics or GPS data. VR is an artificial environment that is created with software and presented to the user with a virtual model of the real world. VR therefore allows for isolation of the user during prototyping. 2D, CAD and BIM plan sets can be transformed into a fully immersive augmented and virtual reality, providing a virtual 3D overlay view of buildings and interiors. This allows stakeholders to obtain an improved understanding of what is to be built, along with visibility of spatial mapping. Additionally, it can increase customer and investor satisfaction by allowing a greater degree of input in the initial planning and design phase. Providing full emersion allows for stakeholders to increase accuracy in projections, optimize training, identify risks and increase safety before the construction process begins.
Subsequently, it can increase reliability while decreasing margin of error. Usability can consequently be improved earlier than the traditional process of utilizing plan sets. Geo-enabled technologies Geo-enabled technologies have unlocked the potential of location data to drive informed decision-making, process standardization and efficiency. These technologies utilize cameras and sensors to obtain data, measurements and quantities over the lifecycle of a project. Drones, also known as unmanned vehicles or remotely piloted aircraft, are becoming increasingly popular to provide onsite digital asset tracking, continuous spatial inspection and progress monitoring. Having the ability to capture broad-scale aerial photography and send real-time images, video and data to computers or mobile devices is expected to be used for simulating a construction environment to test scenarios and facilitate evidence-based decision making.
Such deployment promotes faster planning, construction work and site safety. In the UAE, contractors are extensively using drones for monitoring and inspecting sites. In a labor deficient Japan, Komatsu Ltd. began using drones that create 3D maps, extract blueprints and simulate construction plans. The future of drones on a construction site will help enhance analytics, schedule management, labor efficiency and promote waste reduction. 360-degree cameras can provide monitoring for enclosed rooms and buildings. These cameras are providing assistance with waste reduction and tracking materials, equipment and inventory. This technology is also advancing toward labor productivity tracking and precise real-time spatial measurements.
Suffolk Construction has integrated image recognition software with automated monitoring capability to recognize construction risks and hazards. Cameras eventually may be used in optimizing cost management and holding contractors accountable for design, materials, labor and potential change orders. Sensors have also become increasingly popular. Gilbane Construction Company has recently adopted a system of wearable sensors that enables management to analyze construction operations and productivity in real-time. Utilizing these sensors alongside GPS diagnostics, work can be monitored remotely to help enhance productivity.
Industrialized and componentized construction advances
Digitally-enhanced manufacturing of componentized buildings
With a heightened focus on efficiency and faster building methods, industrialized construction (prefabrication and modular) is on a growth path and the trend is emerging across the globe. According to a survey conducted by Commercial Construction Index, “nearly half (45%) of contractors currently using prefabrication and modularization techniques have seen increased use in the last three years.9 The industrialized approach shifts many construction activities away from the site and allocates these tasks to a factory. Preassembled building components and modules are then shipped to the construction site for assembly.
While these are not new concepts, opportunities have compelled developers and contractors to apply prefabrication with technological innovation to their projects. Pursuing this strategy helps overcome construction challenges, including speed of delivery, economic viability, quality and enhancing environmental sustainability. Many construction companies are applying digitization to prefab and modular. This will drive further momentum and may eventually lead to the emergence of one or two market leaders in this space.
Technology is a dominant theme as it continues to reshape conventional property uses, while transforming the back office and construction supply chain. Many of these technologies addressed in this paper, such as drones, 3D printing, robotics, AI and IoT, are expected to provide substantial improvements to industrialization and construction productivity. The continued impact of disruptive forces — from changing customer behavior to technology initiatives, changing demographics and growing competition from non-traditional players like startups and technology-based businesses — is leading to continued and advancing change. It seems likely that, over time, componentized or industrialized construction will become the dominant solution in the industry for certain asset types, such as multifamily and commercial.
3D printing
Also referred to as additive manufacturing, 3D printing digitally creates successive layers of materials to produce three-dimensional objects from a digital file. 3D printing has evolved to be a natural fit within the industry, usable for a variety of suitable materials (notably polymers, metals, ceramics and concrete) and providing almost limitless freedom of flexible design.
Realizing reduced costs associated with fabricating complex shapes provide less constraints on architects and designers. Emerging opportunities include printing piping and fittings, tools and equipment, formwork for concrete, structural insulated panels, walls with embedded MEP systems and roofs with solar tiles. 3D printing is especially valuable for prefab and modular construction. With the large majority of prefab construction work done in a factory, it becomes more feasible to add a 3D printer to the production lines. A 3D printer has the ability to print complete components and modules (integrated with insulation and MEP) that will eventually be shipped to the construction site.
Internationally, 3D printing has evolved to printing complete houses and offices. In 2014, Winsun, a Chinese company founded by inventor Ma Yihe, built 10 houses of 200sqm in a day using an industrial-scale 3D printing machine. Most recently, MX3D created a 41-foot smart bridge from 3D printing technology utilizing metal alloys. Reduction in construction time, human surveillance and environmental impact suggest that 3D printing will continue to become more prevalent.
Physical robots
Robotics that allow complex physical tasks to be performed with minimal human intervention are becoming more common in the construction industry. There has been extensive development of methods to automate various trades. Robotics are being utilized for bricklaying, welding and concrete pouring. Employing robots to perform typical human labor provides construction efficiencies, precision, reduced human labor and enhanced safety. Similar to 3D printing, utilizing robots in a prefab factory can be highly effective. Robots have been contributing to production lines of manufacturing industries for decades, performing repetitive tasks more efficiently and with greater accuracy than humans. Some prefab construction companies are exploring robotic capabilities and have begun implementing them in their production factories. Present initiatives indicate that fully autonomous factories, logistics, transportation, and eventually the complete supply chain, may be completely automated with robotics.
Construction automation — Supporting work through digitization
Robotic process automation (RPA)
RPA is one form of automation, commonly used for boring, repetitive and mundane tasks. Automation takes a current or modified process and enhances this via the use of digital tools, enabling machines (computers) to undertake the work previously executed by humans. It improves speed, accuracy, consistency and cost of executing these routine tasks. RPA can change project controls and tasks related to project finance. For example, financial forecasts may no longer require manual entries in Excel. Instead, the robots (a ‘bot’ or ‘program’) can collect data from multiple systems, while algorithms build forecasts based on past and present data (using predictive analytics). A computer software program that operates repetitively with rule-based processes, RPA replicates and collaborates with the actions of a human being, interacting with the user interface of a computer system. The software is trained to connect multiple fragmented systems with automation and is based on functional specifications that can be adjusted. Given a renewal of the existing IT landscape is not required, a high level of automation that collects and transforms data can be reached with minimal effort.
The software then allows the capture and interpretation of a business process in a repetitive, audited and controlled manner. Subsequently, business and administrative processes can be fully automated and programmed by a computer to monitor and reduce costs, save time and enhance reporting. Briq has developed RPA programs with bots to track and record city council meeting minutes and permitting issuances across municipalities. Users receive weekly ‘intent to build’ scores for the metro area, along with market updates and forecasts. This allows for real-time information to be shared with developers who look to capitalize on investment opportunities from a recent entitlement or rezoning. EY teams have recently created Payment Application Managed Service (PAMS), a digitally automated back of house support solution. PAMS is a cost-efficient construction and facilities management invoice processing solution for clients with large owned or leased real estate or infrastructure portfolios.
Successful digital transformation of a company’s payment application and processing leads to internal procedures being automated and therefore saving costs, improving controls and enhancing transparency. PAMS has had many success cases, including automating 72% of payment processes for a global company and reducing the processing time from 60 to 7 days. This client experienced 40% processing cost savings and 9% lower total costs for all of their payments. RPA and other forms of automation can supplement typical human tasks, reduce error rates, enhance controls and eliminate redundant and repetitive tasks. This may help address some of the skill shortage being experienced by construction in the competitive labor market.
Facial recognition and biometrics
Facial recognition captures graphical information using multiple data points like distance between the eyes and facial curves that are unique to individuals. The information is stored utilizing an algorithm in a database. When accessed, the system scans and matches the facial information by applying it to the algorithm. Current investment by owners, developers and contractors include facial recognition to enhance safety at the construction site, access control and productivity monitoring.
Using facial recognition, site access is restricted to workers and authorized personnel. Contractors are also able to use the data from facial recognition as backup for invoicing. In 2019, the global facial recognition market was projected to grow from $3.2B to $7.0B by 2024, at a CAGR of 16.6%.8 As the technology progresses, it can potentially change the landscape of physical security, payroll systems, project controls and resource optimization, helping to reduce cost and enhance control. Facial recognition is currently saving Health and Safety International’s building services contracts £140,000 per year.
Artificial intelligence (AI)
The global AI construction market is also forecasted to grow substantially, from $407.2M in 2018 to $1.8B by 2023, at a CAGR of 35.1% 3. AI is a label given to computing systems that exhibit the ability to perceive information, retain it as knowledge, and apply it to making decisions. AI may also interact in ways that seem natural to humans, while simultaneously learning from those interactions by utilizing machine learning. Supported by vast amounts of accessible data, advances in AI have allowed for improved learning algorithms that enable the extraction of deeper levels of meaning. AI can drive productivity improvements as the systems augment human skillsets and reduce the need for tedious human effort. The rising demand for AI- and machine learning-based solutions, the increasing need for greater safety and the ability to reduce production costs are all expected to drive the growth of AI in the construction sector.
Current AI efforts include project schedule optimization through historical data, identifying unsafe worker behavior through image recognition and classifying signals and patterns to deploy real-time solutions. This allows AI to prioritize preventative maintenance and prevent unplanned downtime through enhanced analytical platforms. As this technology progresses, it will optimize project supply chains by tracking and analyzing complex data, such as providing the ability to employ artificial neural networks to predict cost overruns.
Blockchain
Blockchain helps provide the construction supply chain increased functionality, efficiency and visibility. Blockchain is an open public database where transactions are stored in virtual blocks. These blocks are connected together in a chain, creating a complete history of all transactions that have occurred within a particular network. Blockchain has the potential to encrypt and protect key elements in construction operations and supply chains. This technology could potentially handle all contractual relationships using concepts like smart contracts and electronic verification. Blockchain-enabled distributed ledgers can enable better transparency and accountability in construction projects by addressing scope creep, contract changes and elimination of waste to reduce costs.
A grouping of smart contracts can be used to create a decentralized autonomous organization (DAO) that is operated by rules encoded as computer programs. Smart contracts executed between the client and the contractor will enhance the design, tender, install, monitoring, certification and handover of the built asset. By integrating blockchain, a construction company or building maintenance system could function by a project or building’s DAO placing an order for products and services.
Materials are tracked in an undisputable blockchain ledger and the DAO accepts delivery. Once the DAO calls out a contractor to install the material, smart contracts release payments as materials and services achieve milestones. Should milestones or thresholds be missed indicating reduced fees, the automated system would send alert and recommend course correction. Lastly, the DAO would make final payment to both the supplier and installer from the owner’s bank account. The DAO could enhance rent collection, corporate expenditures and insurance payments with autonomous management.
Internet of things (IoT)
IoT enables the connectivity of assets and big data analytics, providing new insights for project teams by capturing large amounts of reliable data in real-time. IoT is the network of physical devices, such as components, appliances, equipment, buildings and vehicles embedded with electronics, software, sensors, actuators and network connectivity, enabling these objects to collect and exchange data over the internet. Combining the features of telematics, asset management and connected BIM, along with using radiofrequency identification and tracking devices, could lead to highly increased efficiencies. The benefits of IoT span across the entire lifecycle of a project and promote sustainable, whole life costing. Throughout the entire life cycle, machine learning will continue to recognize opportunities and provide analytics and recommendations to maximize productivity.
Emerging opportunities include installing meters and monitors at the beginning of construction to analyze output (energy, utilities, labor, etc.) and optimize visibility supply chain interaction and site conditions. IoT enables green buildings to complete tasks, such as shutting down unnecessary systems when the building is unoccupied and opening and closing louvers automatically to provide optimal levels of natural light. Predictive maintenance programs can also be established with IoT. When fitted with sensors, construction equipment can automatically send notice if any abnormal patterns are detected. This alerts workers to intervene early to avoid critical down time or further damage.
Smart buildings to smart cities
IoT is the basis and overarching framework for smart buildings, providing a key enabler of new business models for commercial real estate. With building automation and IoT centralizing control and integrating all systems in a building (heating, ventilation, lighting, etc.), it augments the complete project life cycle and establishes the business case for smart buildings. Smart buildings are constructed to provide autonomous improvement strategies and recommendations (utilizing AI, RPA and machine learning) that enhance the well-being and productivity of users while simultaneously saving operational costs and increasing building efficiencies.
Building managers are looking at smart buildings to analyze space users’ needs and move beyond the traditional lessor/lessee relationships. Smart buildings are planned to transform the business model and create real estate as a customer service platform. The customer service platform leverages data, machine learning and integrated building infrastructure to significantly enhance the user experience. To enable the transformation of a smart building requires a deep understanding of tenants, usage and occupancy patterns, as well as driving more information from building management systems — all of which can be explored through various smart building technologies.
New technologies, such as Tesla’s battery packs and solar roof tiles can be incorporated into smart buildings to enhance energy efficiency and enable the building to be net zero. Net zero establishes that the total amount of energy consumed by a building is roughly equal to the amount of energy created on-site. With a battery pack and solar roof tiles, buildings are now able to become completely net zero, create and store additional energy, which can allow a building to remove itself from the traditional power grid. Surplus energy can then be sent back to the power grid and require the owner to be compensated. Smart buildings will consistently analyze energy consumption and determine its distribution during operations.
Conclusion — Implementation of ConTech and PropTech
The globalization of capital, emerging technologies and changing demographics require the real estate and construction sectors to rethink traditional paths to successful management of the built environment. To remain competitive, companies must explore new structuring options, improve the efficiency of operations and balance portfolios to maximize return on investment — all while mastering digital disruption and gaining a deeper understanding of customer preferences. To create a successful digital strategy that will maximize chances of long-term success, firms should first challenge its strategic direction, and then define the future state of the organization that will create lasting value. Only 25% of real estate and construction firms have a digital strategy and only 9% feel they are prepared for the digital revolution.
A key factor in this lack of progress is the minimal profit margins systemic within the industry. Construction firms typically have profit margins of 2-3% compared with an average of 20% in other industries. When profit margins are narrow, spending 1% of revenue on digital upgrades and innovation can seem like a heavy and risky investment; however, failing to invest in solutions that could boost output is counterproductive. The most innovative will invest and gain a critical strategic advantage over the rest. The World Economic Forum estimates that a 1% rise in productivity could result in savings of $100B per year in the construction industry.14 Additionally, many studies have recognized that the industry wastes up to 30% of all capital injected, an unsustainable situation in the long term. We expect a few, digitally focused, construction and real estate organizations to take on these challenges and to subsequently dominate the global market in the second half of the century.
New technologies and market competitors continue to emerge. The rapid evolution of construction and real estate technologies emphasizes that those who act fast and decisively, embrace disruption, and focus on achieving long-term flexibility will emerge as the leading organizations in the future. Companies should include digital in every aspect of their operations in order to achieve maximum data-driven insight. This will enable them to identify new opportunities and threats across their value chains. With technological innovation quickly expanding, now is the time to embrace disruption, use change to enhance productivity and efficiencies, and prepare for the progressive digital evolution within the construction industry.
Cookie Consent
We use cookies to personalize your experience. By continuing to visit this website you agree to our Terms & Conditions, Privacy Policy and Cookie Policy.