Concrete continues to be the leading material in modern day construction
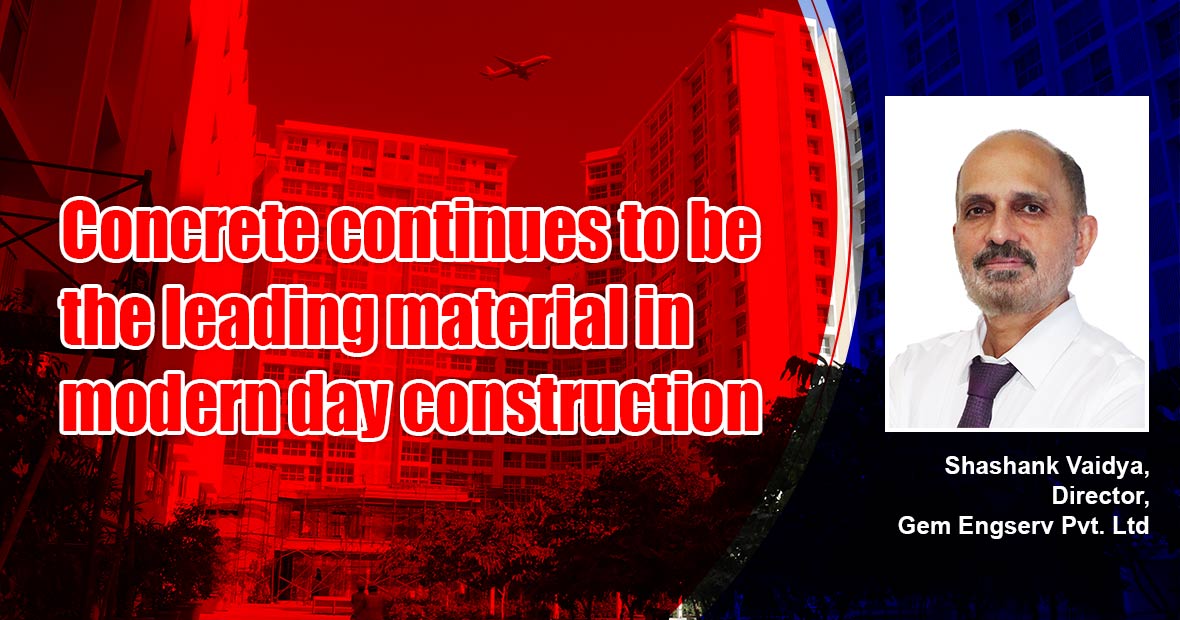
Concrete continues to lead the pack and is emerging in different avatars like self-compacting concrete, self-curing concrete, self-healing concrete and foam concrete etc says Shashank Vaidya, Director, Gem Engserv Pvt. Ltd.
What kind of maintenance is required for the existing buildings which have come into existence as a part of the modern construction methods?
In the context of maintenance efforts, changes and improvements that have taken place with regard to services (MEP) and finishing works have greater impact. Though many new technologies such as use of Aluform formwork, precast construction, tunnel form etc. are emerging, these do not change the basic structural form or the material of construction. We continue to use concrete in different grades and characteristics in RCC and prestressed concrete construction. Structural steel in any case is even older than concrete construction.
What has changed is the speed of construction. A building that used to take up 3-4 years to construct can now be completed in 2 years or even faster. The pace of construction sometimes has resulted in the appearance of cracks or settlement etc. and these need to be identified and addressed early.
Settlement cracks also cause disturbance in waterproofing treatment done in the buildings. Even after taking a warranty of 5-10 years by a waterproofing agency, the appearance of seepage and leakages in the flats give worst nightmares to the occupants of the flats, especially for buildings in Mumbai where in rains are heavier compared to other metros. Therefore, maintenance for arresting waterproofing issues becomes very essential.
Unlike a regular building when it comes to high-rises, what kind of maintenance measures are most desired to keep it in good health?
With new technologies and many incentive schemes like additional FSI/FAR extended by many governments, the height of buildings has gone up (still nothing compared to those in the developed countries). With high rises, come greater lateral displacement and time dependent changes in structural concrete. If we do not recognize and manage these, it could lead to distress in the façade. At higher elevations, design of windows needs to be carefully done to take care of higher wind forces. There needs to be greater emphasis on better quality of windows etc. Use of glass façade also changes the maintenance requirements of buildings. Elevators and fire-fighting systems are obviously far more critical in a high rise than in a low/mid-rise building and these deserve greater attention during design, construction and maintenance phases. Access to various parts of the building is also crucial and this aspect must be considered at the design and planning stage itself.
When it comes to infrastructure audits, what should be the frequency of this exercise when it comes to infrastructure facilities used by the public, what are some of the key parameters to be looked at?
I presume that by audit, we are referring to structural audits or regular inspections to monitor the health of the structure and not quality audits during construction. All structures deteriorate over time, due to the loads imposed on them, exposure to the environment and time dependent changes such as fatigue, creep and shrinkage. It is difficult to lay down a frequency for such audits. What is required is an effective inspection management system. Different structures deteriorate at different rates and the inspection frequency should be flexibly determined. Younger structures do not need frequent audits, whereas older ones require to be monitored at close intervals. It is also a good practice to have different protocols for general and detailed inspections. General inspections help detect any defect early and can trigger detailed or focused inspections.
What are some of the modern construction methods developers and builders need to adopt in order to create robust buildings?
Precast construction, though not a new technology per-se is definitely something we all need to embrace in India and on a bigger scale. 3D printing technology is also rapidly gaining ground, though I do not have enough knowledge about it to make any definitive comment. Combination of concrete and structural steel, light weight steel (LGS) in different elements of a structure are other possibilities.
What are some of the key materials which will forge the buildings of the future?
Concrete continues to lead the pack and is emerging in different avatars like self-compacting concrete, self-curing concrete, self-healing concrete and foam concrete etc. With greater awareness and emphasis on reducing the carbon footprint of construction we may see some other materials emerging and challenging concrete. Bamboo construction is already catching up, though its cost is a constraint and areas of its application are still limited. There are attempts to find alternatives to steel as reinforcing material in concrete and these include basalt fiber reinforcement and bamboo. Glass, aluminum, GRP, composites are not new but their application in building construction is more in non-structural elements rather than in the main frame of the building. Newer materials using nanotechnology will continue to emerge and owners will do well to have in-house capabilities to critically examine all such newer materials and use them appropriately.
For more info visit: http://www.gemengserv.com/
Cookie Consent
We use cookies to personalize your experience. By continuing to visit this website you agree to our Terms & Conditions, Privacy Policy and Cookie Policy.