Evolution of monsoon proof homes
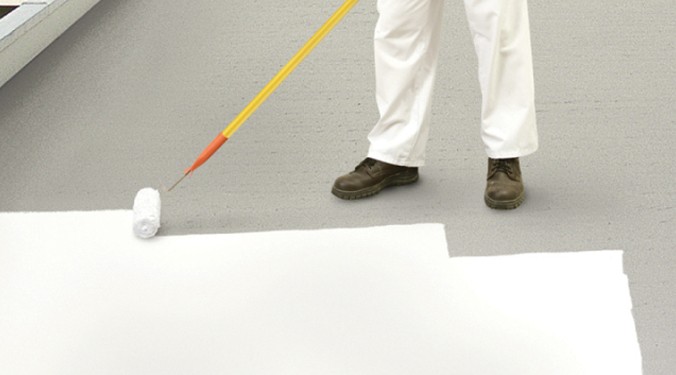
From the right choice of products to proper planning and correct application, a sequence of procedures need to be carried to ensure buildings, apartments and homes are monsoon ready, read on to know more
A building, apartment and home is designed to provide its occupants with a space to live and keep them protected from the local environment. To ensure lifelong protection, they too, need to be properly maintained. One of the key concern areas, which involves a number of other parameters too, is waterproofing. Water damage can result in serious issues to a building’s structure and appearance. When exposed to water, foundation cracks or joints may lead to bigger structural problems. These include leakage, spalling and deterioration, not to mention growth of mold spores. Waterproofing ensures that the building remains safe from water induced damage usually caused by rain, moisture and leaks.
Apart from completed projects, the under construction projects also need to be protected especially during monsoon Prem Nath, Principal Architect, Premnath And Associates says “Monsoon is one such time which can cause havoc on site, hence the most efficient way to avoid it is to always plan ahead. Apart from the technological advancements, pre-planning, critical arrangements and provisions of equipment and labour can ensure a steady workflow for the project. There were advancements in the traditional ways too, use of tarpaulins which are made of polymers and other fabrics. These fabrics are usually stitched together or bolted to the scaffolding or the framing of the building as an envelope.”
Having said that, Sanjay Shah, Vice President – Projects, The Wadhwa Group points out “These two or more cycles of monsoon witnessed by buildings are a boon to identify any lacuna/defects in the structure and to take appropriate action so that future possible problems are avoided. We identify areas that need attention during the monsoon cycles by detailed survey and plan for the measure to treat them once the building is readied for final finishing both internally and externally.”
From choice of the right product to its proper application there are a number of key areas which need to be looked at when it comes to proper waterproofing. That apart, all the stakeholders like the structural engineer, waterproofing consultant, architect and the builder too need to be on the same page in terms of tackling the issue in an effective way. Speaking about the application and planning which is imminent for effective waterproofing Yogesh Patil, Lead – Structural Engineer, Adani Airports Holdings says “When applying waterproofing, we need to remember to add protection layers and follow a pre and post application checklist with the site engineer to ensure that the work is done properly. Unlike earlier, today there is a great deal of awareness about waterproofing but it is essential to plan from the beginning itself. From the position of the drainage points and AC units to the detailing and the product, there is a proper sequence which needs to be followed. Usually waterproofing failures happen when one does not follow this sequence.”
Adds Sanjay “Issues of water leakages are resultant of two factors. First bad workmanship and second defective joinery. Once the slab is cast it is followed up with a series of checks to ensure quality output. Nowadays most reputed developers have adopted to aluminium formwork method where external walls are in concrete. No more brick walls/concrete block walls on the exterior with plaster-like good old days. Being cast monolithic in concrete the external walls withstand better weather impact. The second issue of joinery of artificial cladding materials with mother structure if not done well can cause water leakage/seepage. Hence the use of innovative products that keep coming up in the industry wherein from the casting of structure to the application of finishing material up to the final readiness at every stage these materials are brought to use so as to achieve monsoon proof design of the structure.”
Deepak Mehta, Principal Architect, Deepak Mehta Architects who has worked on numerous high-rise projects in Mumbai and Dubai points out “In order to avoid waterproofing problems and seepage down the line, inputs from MEP consultants and HVAC players must be taken in the design stage itself. Depending on the geography, we need to decide what kind of precaution is to be taken, where to put rain breakers. In some areas, like Mumbai, we cannot have continuous dead walls and the joints between the beams and the brick/concrete walls need to be waterproofed correctly. If your room is facing the south or south west, 4ft wide sun shades are recommended, so that it can take care of the rain lashes as well. Even the detailing of the windows need to be fitted properly or you could have seepage down to the foundation of your home. Even with terraces and balconies, the slopes need to be planned properly so that the water flows out, not in. Textured paint has proved to be useful for waterproofing too, It has been proven to slow down the trickle of water from vertical surfaces.”
Numerous waterproofing problems crop up also owing to the pace of construction. Gautam Eunny, Vice President, Pidilite Large Users Business says “The reason we are seeing problems today more often is because of the fast pace of construction. The pace at which concreting is being done leaves it more susceptible to cracking, sand quality going bad and so on. Waterproofing costs one 1% of the overall building cost. But it causes 80% of the headaches. And most of the failures happen either due to a faulty choice of materials, design, or application.” Speaking on market innovations Euny adds “Nowadays, polymerized acrylic coatings have come up. They are much more versatile. Unlike paint, coatings are thick. They provide much better longevity and weather proofing compared to usual paints. Having said that no matter what you have on paper, it is the choice of your applicator which matters a lot. Do they have the skilled manpower to do the job, are they trained enough to do the job, that’s your biggest warranty.”
Just like polymerized acrylic coatings, Modified Silane Technology is also one of innovations which is being taken note of. Bibhas Aggarwal, Director, Anagha Engineers says, “So far, silicon has been the best sealant for achieving a waterproof, protective joint seal , because it has the capability of resisting weather, humidity, rain, sun, UV light, and wind. However, prices of silicon have soared, and another technology has arisen called MS, Modified Silane Technology, which is much better. MS has a very good bonding and expansion capability between the substrate and the sealant. It can also withstand a greater range of movement as compared to a silicone sealant and can withstand temperatures up to 100 degrees celsius.”
Elucidating on the innovations further Vinit Dugarwal, Director, AM Consultants opines “The construction chemical domain has come a long way. There are a lot of options available today for project managers and developers to choose from when it comes to waterproofing. Some of the popular options include nanotechnology, crystalline and waterproofing membranes. There is also a self-healing water-repellent spray-on coating that is being used nowadays.”
Though there are a lot of waterproofing problems after the people have started residing in a building, home or a house; a number of them can be addressed at the building stage itself. Samir Dharurkar, Principal Architect, We Architects has a word of caution for builders and developers alike he says “Prevention is always better than cure. I would suggest spending a little extra towards the correct product at construction stage only. Ultimately you may land up paying more towards repairs. For high-rises nowadays we have very efficient cranes, cradles, spiderman type systems for high rise buildings. But these repairs have to be carried out considering all safety factors.”
68
Cookie Consent
We use cookies to personalize your experience. By continuing to visit this website you agree to our Terms & Conditions, Privacy Policy and Cookie Policy.