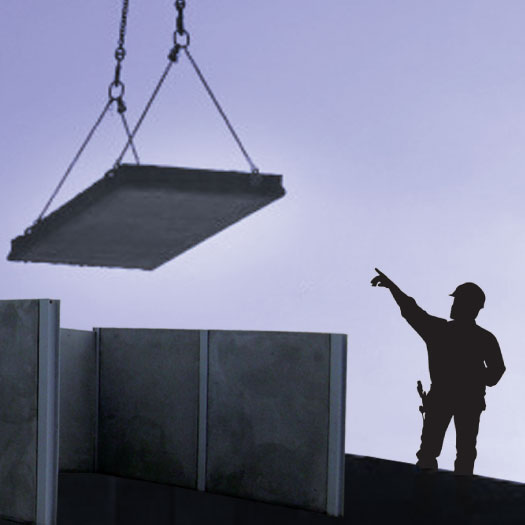
How prefab can help in meeting India’s ‘Housing for All’ target?
Pre-fabricated structure or steel structure or porta cabin are the general terms used to describe prefab in India. Prefab is the technology where one manufacture various components of a building like walls, columns, beams, roof and even floors in a factory and then transport them to the site and erect them with a fast speed. Since the design is fixed, location of door, windows and the fitments is pre defined. Installation processes is fast and seam less.
Another way of doing a prefab structure is to build the whole house in factory and then transport it to the site. Here precision increases as the full work is completed in factory but at the same time there is a hitch that the width of the house cannot be extended more than 8 ft as that is the general width carrying capacity of trucks in India. Exceptions can be made up to 10 ft in special cases.
Majority of the times people are concerned about the pricing of a prefab building and then they compare it with general RCC or brick masonry work. “Since there is variety of materials involved for prefab construction. It offers a price range starting from as low as Rs 200/sq. ft., up to Rs 2000/sq.ft., or even more depending upon specification,” informs Himanshu Yadav, Partner, MecPrefab.
Prefab technology is very durable and reliable when it comes to facing earth quacks. As it is a light weight structure, very safe in case of earth quake as less liable to fall down or causing major fatality, whereas a RCC building with improper steel in it is more prone for cracks failure in tension. As concrete behaves good compression properties then tension which majorly develops during earth quakes. At the same time when it comes to vandalism or major impact on surface prefab fails terribly. Mostly CFB boards and foam concrete panels. Whereas MS/GI/SS sheet claddings are subjected to be easily cut into using normal tools as a cutting machine even a hammer and a chisel.
“To make prefab a popular and adaptable solution it is always better to use an intermediate solution like making outer walls of house using brick masonry and remaining all components including internal partitions, roofing, structural members using prefab technology,” suggest Yadav.
Housing For All – means to meet up the requirement criteria of general Indian population, which varies on various factors such as what is a prefab? Is it cheap or cost effective? Is prefab durable and safe? Why should I adopt prefab instead of ongoing RCC and brick masonry construction? Can we make more than single storey with it?
“Prefab in India as of today is seen as a 2-Minutes Noodle solution of completing a project to meet the dead line,” states Yadav. Be it Common Wealth games in Delhi or Swatch Bharat Abhiyaan or opening of Mohalla Clinics in Delhi or other such projects across India. Various housing projects are also carried out Like Rajiv Awas in Delhi using prefab concrete blocks technology.
Sharing his opinion on how prefab can help in meeting India’s ‘Housing for All’ target Yadav says, “To meet up both urban and rural requirement of Indian infrastructure, prefab is best possible solution giving to the fact that we need to focus and push intermediate solution combining both prefab and RCC/Brick work construction to provide both reliable and cost effective solution to India’s requirement for housing sector. Truly then only we can provide ‘Housing for All’ with best and effective solution. It is also the best possible solution for construction at tedious locations and challenging environment where it is not possible to carry out any construction using RCC/Brick work methods.”
The Indian government has taken up the ambitious agenda of providing ‘Housing for all by 2022’ which entails wiping out the total deficit, besides providing for increase in urban population as well as for obsolescence. For meeting the target we have to construct nearly 5 million housing every year till 2022. The urban housing delivery so far as per the census 2011 has been of the order of 2.5 million every year. “Accordingly, we need to double the housing delivery process for achieving this ambitious target. The ‘business as usual’ may not be able to address the requirements and the only viable option appear to be through rapid construction technologies using prefab options,” Rajesh Goel, Chairman & Managing Director, Hindustan Prefab Ltd.
The prefab technology options offer better quality housing in significantly lesser time. The components are manufactured in factory controlled environment with strict quality control measures, and are accordingly much superior in quality as compared to the conventional construction. The prefab components also use agricultural and industrial waste like fly ash, and gypsum supporting environment protection. The prefab structures being significantly lighter also consumes lesser building material and thus have lesser embodied energy within it. “Prefab construction also addresses the dust issue considerably, as hardly any raw material like sand etc is stored at site and erection is mostly mechanical. Accordingly, the use of prefab technologies ensures high level of sustainability, besides proving speed and quality,” states Goel.
Government is encouraging ‘Housing for All’ by creating awareness through various mediums and also is introducing new technologies believes Goel. He says, “Towards promoting various rapid technologies, the Indian government under its Pradhan Mantri Awas Yojana (PMAY) has constituted a technology sub-mission, focused on promoting use of such technologies. Through its various efforts including awareness creation seminars, exhibitions, etc, there has been a perceptible change in the acceptability of all these technologies. Major states like Andhra Pradesh, Telangana, Orissa, Maharashtra, Gujarat, Chhattisgarh, Jharkhand etc, have taken up prefab housing in a big way and many projects are coming up in these states. The industry has also responded very favourably and has shown its willingness to invest in setting up of manufacturing facilities and contribute to the programme of ‘Housing for all by 2022’.”
Hindustan Prefab Ltd on its part has taken up a major role in promotion of these technologies as sectoral leader have brought the stakeholders together to work effectively for the effective use of prefab technologies in this ambiguous mission. The company has established the housing technology park at Jangpura showcasing 11 alternate housing construction prefab technologies, which could be utilised for construction of housing units. The various technological options at the technology park for their effectiveness to provide better quality, reduction in construction time, insulation, ease of material transportation, structured safety, durability, requirement of skill manpower and user acceptance keeping in view the living habits of the user. The park has been developed over an area of two acres at Jangpura with support from the private players, technology providers and other stakeholders. The technology park provides stakeholders an option to assess and compare the technologies for their respective use. The technology has been visited by a large number of stakeholders including batches from the engineering and architectural colleges from different parts of the country. This housing technology park has proven to be a game changer in the technology for the prefab technologies sector.
“With the massive requirements of housing in both urban and rural areas, and the stress on sustainability in construction, the prefab housing technologies have a clear path etched,” adds Goel.
Informing how prefab will help ‘Housing for All’ target Rajiv Upadhyay, Chief Operating Officer, Aerocon Building Solutions, HIL Ltd briefs, “Majority of activities for residential buildings could be completed off-site. Practically all part of house can be pre-fabricate–columns, beams, ceiling slabs, terrace blocks, wall panels, and staircases can be fitted readymade. By leveraging on innovative and low-cost construction technologies, such as pre-fabrication, developers can construct affordable houses quickly and cost–effectively.” Although the initial cost of using prefab technology is 20-25 per cent higher compared to the traditional construction technology, both developer and customer would gain from overall benefits like faster construction, lower labour cost, better aesthetics and on-time delivery of the final product. “In Europe and Middle East, use of prefab homes technology has enabled certain developers in saving up to 64 per cent of the total man hours needed using conventional methods,” points out Upadhyay.
He also mentions that prefab technology is not labour intensive when compared to the conventional method of construction. In fact, the biggest challenge that the construction industry faces is the lack of skilled labours. This can be solved by bringing in pre-fabricated and fitted units and assemble them into the residential units. Prefab homes or modular construction technology can solve many labour issues especially when building projects in distant localities.
“With Prime Minister Narendra Modi’s ‘Housing for All by 2022’ scheme, it will become necessary for developers to build affordable homes at a faster pace. This will be achieved by using modern construction technologies like prefab technology,” adds Upadhyay.
Cookie Consent
We use cookies to personalize your experience. By continuing to visit this website you agree to our Terms & Conditions, Privacy Policy and Cookie Policy.