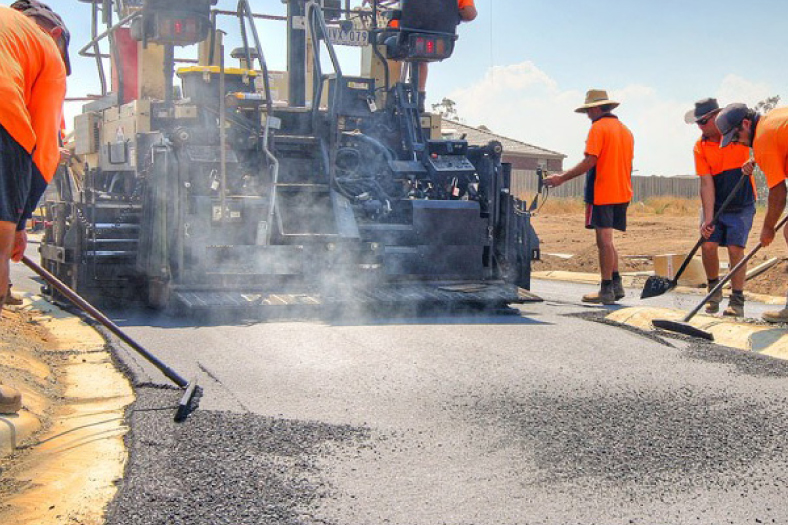
Equipment that saves energy as well as fuel while maintaining uptime, is the need of the hour.
With the government implementing a multitude of big-ticket projects, roads and highways continue to be a strong growth driver for the construction equipment industry. However, ensuring timely completion of these projects not only entails the best quality output, but also creates a need for specialised, intelligent and technologically-advanced construction equipment.
Parameters for buying road construction equipment
Product reliability and productivity
To fully leverage the opportunity in the road construction sector, JCB introduced a wide range of innovative machines which exhibit a blend of technology and digital innovation to meet the demand for machines to build India’s next-generation infrastructure. Jasmeet Singh, Head- Corporate Communications and Corporate Relations, JCB India Ltd says, “Today, customers are looking at products which offer value for money along with all the advanced features. They are looking at a higher return on investment (ROI) over an extended period of time.” Product reliability, productivity and support are key factors in the purchase decision.
Fuel efficiency
Volvo’s equipment offers fuel efficiency and productivity levels – things which customers’ love globally, particularly in India. Dimitrov Krishnan, Vice President and Head, Volvo CE India says, “Customers in India love Volvo machines so much because they can deliver the fuel savings they want but without the need to take on newer hybrid systems, instead utilising proven designs. Volvo offers high quality and productive equipment that delivers the best levels of fuel efficiency in the industry.” With Volvo CE, the customers can do more with their equipment and downtime is minimised. The company’s lower fuel consumption improves cost efficiency and means work environments are cleaner. Overall, its customers can enjoy high levels of ROI.
Dimitrov says, “In 2018, with the government’s infrastructure push, we expect to see strong interest in the EC200D, which was designed specifically for general construction work.” The excavator features Volvo’s famed fuel efficiency, a bucket breakout force of 123 kN and an arm tear out force of 96 kN, which helps it deliver high job site productivity and fast cycle times.
Enhancing uptime
Considerations for improving productivity
The latest compactor from JCB, the 11T Soil Compactor – the JCB116 comes with a revolutionary telematics technology – JCB Livelink. This state-of-the-art technology enables users to get SMS alerts on their mobile phones or smart devices regarding service alerts, operations and security of their machines. In addition to this, JCB India, for the first time in the industry, introduced a compaction monitoring system integrated with Livelink in JCB116. It provides relative compaction value which helps in achieving consistent and uniform compaction throughout the patch. JCB compaction monitoring system digital display shows high or low frequency and amplitude values for compaction control. This versatile system is suitable for both asphalt and soil surface.
The JCB220LC Xtra (the 22T excavator) is 8 per cent more fuel efficient and comes with gross power of 170 hp. With 8 power modes and smart controls – this machine is 7 per cent more productive in H+ mode. The JCB 305LC (The 30T excavator) comes with JCB Diesel Max engine and delivers 221HP for excellent productivity. 222kN of bucket breakout force makes it easy to remove any thing that comes beneath thereby improving the productivity. Higher productivity of the equipment contributes significantly to the owners’ ROI. Another parameter to improve productivity of equipment is the focus on the operator environment. Over the years, JCB has made significant investment is designing machines which offer the best-in-class operator environment. For example, the 455ZX Wheeled Loaders comes with air conditioning as standard. Additionally, the large cabin interior offers excellent entrance. The stylish, modern central dash display combines analogue dials and a colour LCD screen that displays the health status of the machine, service requirements and operating information. A comfortable operator will be able to use the machine better and safer.
All these class products are backed by sound technology and after-sales support. In 2015, JCB India pioneered an Advanced Telematics Technology called JCB Livelink in its range of products, thus taking the ownership experience to a new level. JCB Livelink enables users, dealers and JCB have complete control on their machines from any part of the world. It provides real-time updates on service, operations and security of their machine and gives vital information to the customer in terms of number of hours the machine has been operational, service intervals, fuel levels, malfunctions if any in real time etc. Jasmeet says,“To monitor these machines in real time, we have set up a command centre at our Delhi-NCR facility. Our dealerships have also set up similar Livelink command centres to ensure real-time support is provided to the customers as they can now plan for service schedules and also engage with users and customers in preventive maintenance.” JCB has introduced multiple mobile applications which ensure all the relevant information is just a click away for users. Applications such as JCB Livelink, Smart Diagnostic, Parts E-sell and Digital product manuals will re-define how customers interact with manufacturers. They are all aimed at improving the overall customer experience by providing all the important information in real time.
Machine monitoring information – save time and money
Dimitrov says, “Equipment uptime is related to optimising machine and operator performance, as well as proactively managing service and maintenance.” With insight into when services or maintenance would be needed, fleet owners and operators can schedule it in rather than dealing with repairs in case of sudden breakdown. To enhance equipment uptime, Volvo offers CareTrack – a telematics system that gives equipment owners access to a wide range of machine monitoring information that can help save time and money. The system generates a wide range of reports with data on aspects such as fuel consumption, operational hours, geographical location and more. These reports are available via a web portal or can be received via SMS or email alerts.
CareTrack can also be used to manage machine servicing and wear parts. This allows fleet managers to reduce fuel costs, optimise machine and operator performance, as well as proactively manage service and maintenance to maximise uptime. CareTrack is offered not as a standard practice but as specialised packages designed to enhance customers’ businesses.
CareTrack packages offers:
• CareTrack standard: Access machine hours and location and manage service plans and wear parts via the web portal.
• Tracking and status: Notifications tells one when a machine goes outside pre-set location and time boundaries. A status report supplies fuel level, machine location and machine hours.
• Operation: Reports highlight how each machine is used and if operators are working efficiently.
• Production: On board weighing technology shows a machine’s true productivity. Accessible information – including load efficiency and number of cycles – reduce fuel consumption and improve component life.
• Anti-theft: Volvo crawler excavators can be fitted with an anti-theft tracking system.
• Communication: Satellite communication is provided in areas where no or weak cell phone connection is available.
• API: API enables CareTrack data to be incorporated into one’s management system.
CareTrack provides maintenance, invoicing, fleet management and operator training. With CareTrack, customers can monitor load efficiency, number of cycles, overload percentages and identify operator training needs. For example, CareTrack can tell owners what time the machine operation starts, takes a break and ends. What’s more, CareTrack allows owners to tap into a wealth of actionable data including fuel consumption, idle time, machine location, fluid levels and service alerts. Dimitrov says, “As owners are pushed to deliver more with less, CareTrack is a great way to proactively manage machines and increase uptime by planning service and maintenance requirement in advance, avoiding potential problems.” It’s also possible for Volvo CE dealers to troubleshoot faults remotely—minimising service and downtime.
__
Customers are looking at products equipped with advanced features, higher ROI over an extended period of time.
Jasmeet Singh, Head- Corporate Communications and Corporate Relations, JCB India Ltd
Equipment uptime is related to optimising machine and operator performance, in addition to proactively managing service and maintenance.
Dimitrov Krishnan, Vice President and Head, Volvo CE India
Cookie Consent
We use cookies to personalize your experience. By continuing to visit this website you agree to our Terms & Conditions, Privacy Policy and Cookie Policy.