Making of airport runways
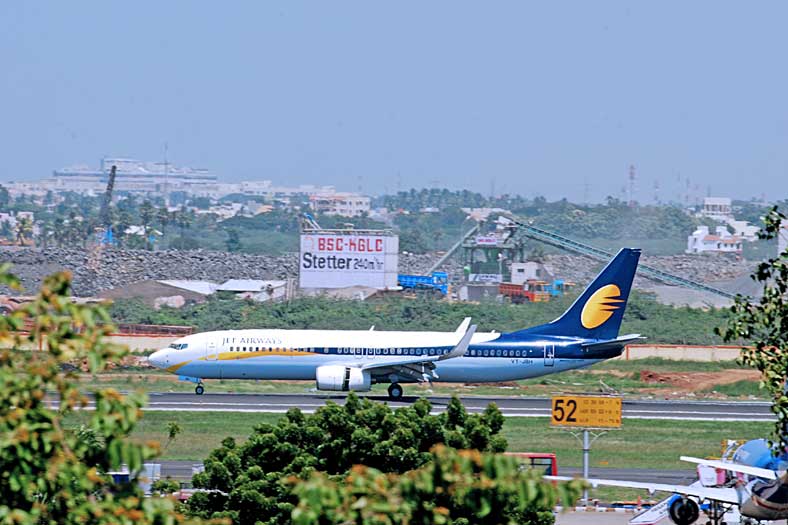
Discussing the role of advanced technology in making high speed, high quality runways for airport.
As airport runways must withstand the huge forces applied by aircraft landing or taking off, the engineering and construction behind them requires a higher level of quality than for regular roadways. Equipment that is used to construct these airport runways must also meet this performance requirement.
“Durability is a characteristic that contractors look for in any machine, but especially so for airport runway construction. As airport security tends to be higher, the process of replacing a machine on these sites is arduous. Hence, durability is crucial,” observes Dimitrov Krishnan, Vice President and Head of Volvo CE India.
He claims, Volvo machines are well known for their durability and are a popular choice among contractors. At the Kempegowda International Airport in Bangalore, there are 18 Volvo machines working on the construction of a new runway. They comprise EC300DL and EC480DL excavators, and SD110 compactors. “The fact that two separate contractors on the project both chose Volvo machines for this work is the testament to their ability to get the job done. The completion of earthmoving works six months ahead of schedule demonstrates the machines’ capabilities alongside our customers’ site management skills,” said Dimitrov.
The powerful EC300DL crawler excavator is well suited to high-volume earthmoving and offers a maximum digging reach of 11.32 metres as well as a digging depth of 8 metres. Its Volvo D7E engine with a 169 kW power rating ensures that the heavy-duty unit delivers powerful performance alongside excellent fuel efficiency.
The EC480DL is the bestselling large excavator in India, with a maximum breakout force of 284 kN, informs Dimitrov. He adds, “Equipped with a Volvo D13H engine, the machine has the largest bucket capacity in its class at 3.1 cu.m. This high productivity is particularly useful on a job with tight deadlines.”
The SD110 soil compactor is powered by a Volvo Tier 3/Stage III D5 engine and plays an important role in delivering high-quality runways. The machine is engineered to efficiently and effectively compact all types of soil, making it ideal for the exacting nature of airport runway work.
P6820C ABG paver – the latest entrant in Volvo CE’s asphalt pavers
The P6820C ABG paver is the latest in a line of Volvo tracked pavers that are built for power and precision. This paver can pave widths of 2.5 metres up to 9 metres. It is powered by a 142 kW-rated COM 3A/EPA Tier 3 diesel engine, which has relatively low fuel consumption.
Volvo’s industry-leading Electronic Pavement Management II technology is built into the paver’s main control unit (MCU), which gives operators total control at their fingertips – allowing instant adjustment to all paving functions. This is ideal for paving precisely on curves and delivering sharp edges on straight stretches.
On the machine is also Volvo’s Variomatic screed, which efficiently delivers quick and consistent heat across the full length of the screed through a three-zone heating system.
Schwing Stetter’s end-to-end concrete solutions
Concreting equipment manufacturing giant Schwing Stetter has always stayed in its toes, to meet the massive demands of every growing industry. This rapidly growing aviation industry demands novel, varied and complex concrete solutions and the same is being delivered by Schwing Stetter India because of its consistent focus on research and developments in innovating concrete solutions.
Schwing Stetter’s high capacity batching plants like H6N (240 cu.m./hr.), H4N (140 cu.m./hr.), H3N (120 cu.m./hr.), H2.25N (100 cu.m./hr.), Mobile plants M2(93 cu.m./hr.), M1.25 (56 cu.m./hr.) etc. are employed to suit the heavy concrete demand arising in these industries for the construction of runways, aprons, hangers, control towers etc. The company’s truck mounted concrete boom pumps of S 36X and S 43SX, Separate Boom Placers SPB 32 and 35, high capacity concrete pumps SP 3000, SP 3500, SP 4507, SP 4800 and SP 8800 have considerably eased the challenges encountered in these projects. GOMACO paver helps in paving runways and aprons using GOMACO GHP 2800. It uses state-of-the-art technology of 3D stringless guidance for slipforming an airport apron.
Projects of such diverse dimensions requires complex solutions because of the peculiarity of its application, which has laid way for innovations like temperature controlled concrete production plants, producing high strength concrete with silica fume, using combinations of two or more admixtures and many more. Modernising concrete solutions based on the market requirements have become a character of Schwing Stetter.
“Be it producing large volumes of concrete or pumping concrete to greater heights, Schwing Stetter India’s equipment have inimitable superiority in carrying out its work with grace,” claims V. G. Sakthikumar, Managing Director, Schwing Stetter Sales and Services Pvt Ltd.
Case Graders for levelling and shaping a surface
For high quality runways, Case India has its graders which are used mainly for levelling and shaping a surface to very fine measurements. “Case Graders are the best available machinery in their class and are engineered to give a very long product life,” assures Shalabh Chaturvedi, Head Marketing, Case India. He adds, “Equipment uptime is one of the major factors that customers consider while deciding on the machine. Time bound projects need reliable machines and considering that CASE’s graders feature an FPT Industrial 6.7-litre engine with triple horsepower ranges on the 865B model and dual horsepower on the 845B to match the power requirements of various applications and deliver optimum fuel efficiency.”
The Grader is offered with an automatic ZF transmission. The machine has a multi curvature moldboard which reduces the resistance coming on the engine and hence reduces the fuel consumption. The air-conditioned cabin of the Grader is spacious and provides excellent all-round visibility and operator comfort.
Case India has two models in Motor Graders with the following specifications:
Features
Maximise productivity: Unique Multi-radius moldboard design that provides mixing effect that does not only push the material on ground but also rolls it, along with net variable HP (140-163 HP) gives a unique mix of power and fuel efficiency.
Optimise fuel efficiency: The grader is equipped with variable horse power FPT engine renowned for its fuel efficiency worldwide. The Grader is offered with an automatic ZF transmission. The machine has a multi-curvature mouldboard which reduces the resistance on the engine and hence reduces the fuel consumption.
Operators comfort: For better control the graders are equipped with a forward-mounted articulation joint and rear-mounted cab, giving operators a clear sense of direction and excellent moldboard visibility from the operator’s cabin. Case also provides optional air-conditioning cabin for better operator comfort.
Ease of maintenance: The motor graders feature single piece engine hood for easy engine compartment access. The machine design also incorporates the Case hallmark ground-level access to daily service checkpoints for quick and efficient maintenance.
Sophisticated operator console: The unique trip meter on the operator dashboard continuously monitors the fuel consumption, hours operated and operating temperatures. The dashboard has electronic indicators for any safety related or operation related parameters.
Cookie Consent
We use cookies to personalize your experience. By continuing to visit this website you agree to our Terms & Conditions, Privacy Policy and Cookie Policy.