Building a world-class Aerospace manufacturing facility
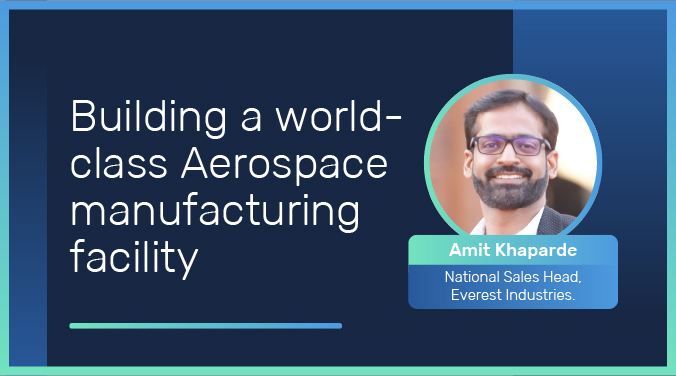
Everest has repeatedly proved its mettle as a reliable partner for executing large projects with critical design and stringent timelines.
Project brief for many reasons, Hyderabad’s world-class aerospace manufacturing facility is an aspirational project. Apart from the complexity involved in the design, this project forms a part of the “Make in India” revolution led by the Honorable Prime Minister of India because of its complexity and scale. The state of- the-art manufacturing facility in Hyderabad is a joint venture between Tata Advanced Systems Limited and Airbus France. This facility will manufacture critical components required for an aircraft in a fully flyaway condition.
Everest was selected as the successful bidder for this project after stringent scrutiny by the Tata Advance Systems Limited team on technical capability and execution without overlooking the economics. The project has been awarded to Everest, considering the gamut of stringent timelines in the execution of this project. With every eye from inland and offshore nations the project is an essential milestone for Everest. The successful execution will undoubtedly open new avenues in the aerospace industry.
Material of construction
The facility required the best materials for functionality and aesthetics. However, this facility will be fully air-conditioned, so end users and consultants have carefully selected thermal insulation with a liner panel to maintain the temperatures within the building for energy conservation. The roof of this building is more than 100 metres long as a single sheet. Hence, specially designed floating clips were used for roof sheeting to take care of thermal expansion and contraction.
Special consideration was given to flashing and trims of sheeting to make this building airtight in certain areas. The project was one-of-a-kind due to its robust design and use of high quality sealants.
Geometry
The plan of the factory has been carefully laid out to facilitate the production line of aeroplane components. The factory is singlesloped, and it has multiple-width modules. The structure is designed for heavy-duty cranes inside the building. The columns have been designed with a fixed base to minimise deflection and satisfy serviceability requirements. The structure has mezzanine areas for which composite joists have been designed to restrict joist depth. The careful lookout was extended to ensure the transverse movements of men and equipment inside the building.
Architectural features
With the roof spanning more than 128 m, it necessitated the usage of specially designed thermal clips that will allow thermal expansion of the Standing Seam roof. The elevation of the building was provided with intermittent louvres to ensure required air changes in non-air-conditioned areas.
• Properly selecting insulation with the required R-value is critical for maintaining the building’s ambient temperature.
• The width of the building and mono slope called for careful design of gutters and downspout arrangements for smooth rainwater drainage.
• Liner panels have been used inside the building to make it visually appealing and provide thermal characteristics.
• Regularly spaced polycarbonate sheets with UV coating and high transmissibility have been installed to provide ambient natural lighting inside the building while conserving energy in non air- conditioned areas.
Uniqueness and challenges
A single-slope roof for such a large width gives the building a unique look. Given the type of roof, designing sufficient gutters per the location’s maximum rainfall intensity was a challenge. Strict adherence to a very tight execution schedule was also an added challenge. Hence, completion of the design phase, manufacturing, and well orchestrated logistical support ensured the completion of the first phase’s execution well before time.
There was no room for error, as that would delay the project, and such delays would have caused a loss of precious time and delays in this marquee project. Everest Industries and its internal teams were quick enough to address early challenges that had put pressure on the complete schedule of the project and get it back on track.
Conclusion
The customer has appreciated Everest for its accurate planning and agility toward the change matrix during the execution phase. Our unmatched design expertise enabled us to provide the most optimal design for the structure, which led to significant cost savings for the customer.
We have been working with numerous cranes, boom lifts, and Farhanas in this project, and with strict adherence to safety guidelines, we have clocked more than 1,00,000 manhours in this project. We are confident that we will conclude the project with all safe practices being followed. This project, in particular, will provide access to a wide range of aerospace industry requirements.
84
Cookie Consent
We use cookies to personalize your experience. By continuing to visit this website you agree to our Terms & Conditions, Privacy Policy and Cookie Policy.