Dry Construction
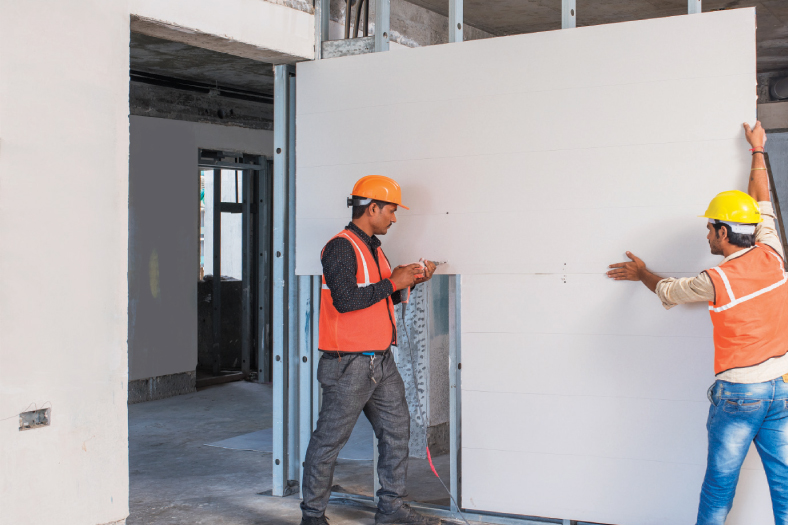
A pioneering global standards in premium home construction
T he Indian economy is now in its fourth year of sustained 7 per cent growth – a trend, which is likely to continue over the coming years.
The effect on the real estate (RE) sector has been a trailblazing transformation of India’s top metros where RE growth has transformed skylines, business districts, neighbourhoods and suburbs of every metro.
Owed to demonetisation, REITs, RERA, and the centre’s focus on manufacturing, FDI inflows in real estate and construction technology will only continue to rise over the coming years.
While brands like Panchshil Realty have seen higher-than-average capital value appreciation and absorption, smaller and medium developers are having to contend with rising expectations of a globally aware home-buyers with high expectations of product quality, service and support. Overall there is a clear market shift towards investing in leading brands with a proven track record and reputation.
Add to that issues of rising cost inflation, timely completion and construction quality and it is clear that rapid and significant transformation for real estate construction is the need of the hour.
Panchshil Realty’s success however lies in the introduction of several such global practices in India through its best-in-class use of construction technology – one of them is Dry Construction Technique (DCT).
What is Dry Construction Technique?
By definition, DCT involves the use of innovation to reduce the use of water and the impact of a real estate on the environment. It also includes the use of lightweight material, structures and systems created on the principle of lightweight construction.
DCT involves the construction of interior walls, ceilings and floors using plastered or microfiber board that is joint at the time of installing. Apart from dry wall and ceiling; the façade is also done with Aluminium Composite Panels (ACP) instead of brickwork and plaster. This is a signature technique being followed in recent Panchshil projects like Yoopune (by Philippe Starck) and Panchshil Towers.
The light-weight construction technique is 8-10 times lighter than traditional brick and cement work and allows up to 70 per cent saving of construction time, while ensuring the minimal use of water (compared to traditional wet construction).
Demand for DCT
Globally DCT is projected to become a $ 79.08 billion market by 2020 (Markets & Markets 2015), growing at a pace of 5.3 per cent YoY (Research & Reports 2015). However most of the growth is now expected to come from India and China.
DCT brings together an ecosystem of global manufacturers of materials, metal frames and beams, covering, wiring, piping, insulation, structural parts, pre-fabricated panels, boards, flooring, glass, waterproofing among others across US, Europe, SEA, ANZ and now India.
Water conservation using DCT
For large-scale Panchshil projects (such as the one in Kharadi), most of the development area is covered by a network of roads. In conventional practices, concrete roads are preferred. But as these roads requires cement and plenty of water; Panchshil has opted for the more contemporary method of making roads with ‘paving blocks’. These blocks are fixed on drycrush sand, which do not require the use of water. Also, during monsoons, paving blocks allow rainwater to percolate into the ground, which ultimately increases the groundwater table.
When it comes to the use of concrete, Panchshil has been an early user of curing compounds (an alternative way of curing the fresh concrete), and recently for the Trump Towers (Kalyani Nagar), the Pavilion (SB Road) and the nine (9) Panchshil Towers coming up in the Kharadi cluster.
For a better understanding, curing every 100,000 sq. metre area of concrete saves nearly 1 million litres of water, which is a marvel of modern DCT. Interestingly, Panchshil Towers is seeing an extensive use of this technique which uses high-end plasticisers and reducing the water-cement ratio, and has succeeded in saving nearly a million litres of water so far.
Global standards using light-weight techniques
A quick background on light-weight construction–the technique originated from a need to minimise the mass without compromising on the structural strength and was a prevalent process of high-technology sectors like ship-building and aircraft manufacturing and other such where timely completion, cutting-edge quality and operational efficiency were critical to the project success.
Lightweight technique again, is based on three fundamental principles which maybe combined in different ways:
• Lightweight materials: Use of building materials with a low density and is placed in relation to the stress and strain to which the material is subjected.
• Lightweight structures: Use of structures which resist the loads with minimum self-weight.
• Lightweight systems: A combination of load bearing functions with other functions like enclosing, sound insulation, fire-proofing, etc.
The growing use of light-weight construction in DCT is primarily the shorter construction timelines, good economics, better building mechanics, but above all in their superior sound insulation and fire-protection (especially when compared against regular brickwork and masonry).
Other advantages include ease of repairs, renovation and maintenance. For instance, when fitting out elements such as lighting units, speakers, detectors and sensors, the finish is flush and near-perfection. Another advantage is that unlike the traditional brick and mortar method, the process, generates minimum construction waste. It also helps to preserve room temperature and provides energy efficiency. Incidentally, most of Panchshil projects have been awarded Platinum and Gold LEED certification.
Future of DCT
With more innovation and evolution of this category, the processes, shapes and surfaces can be further modified to suit different architectural and design requirement.
Top brands are already ensuring the health and safety of their customers through use of hazard-free ingredients, moisture resistance materials, and use of non-toxic/non-irritable materials.
With increasing commitment to sustainability in all aspects of construction, ‘green’ dry construction technology will be the future of the DCT market where re-manufacturing, durability, low-maintenance, recycling, reuse and sustainable sourcing will be part of the DCT best practices in India.
Authored by__
Santosh Kolekar
Executive Vice President for Construction
Panchshil Realty
54
Cookie Consent
We use cookies to personalize your experience. By continuing to visit this website you agree to our Terms & Conditions, Privacy Policy and Cookie Policy.