High Rises – Addressing the urban realities
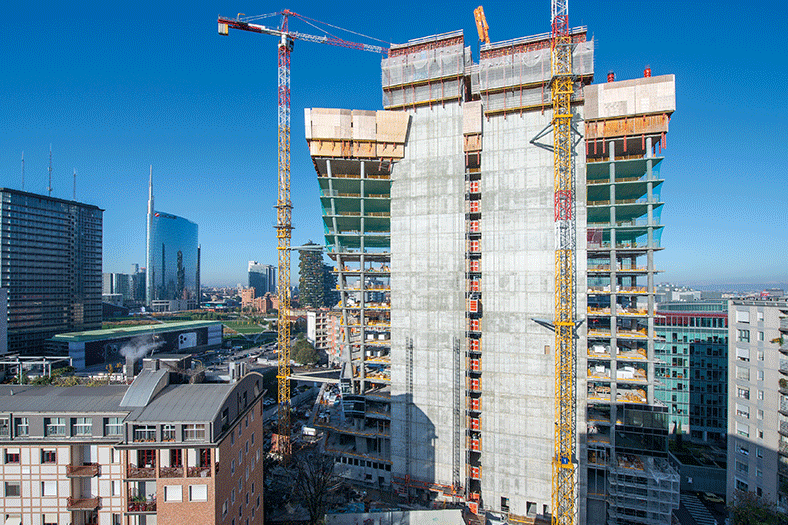
The construction of a high-rise requires a well-organized approach. All the stakeholders have to work in tandem to ensure the structure is and also remains safe, robust and sustainable for generations to come.
High-rise has become a necessity in the urban landscape to gratify the need for affordable as also quality housing. The rate of urbanization too has a direct relationship with the growth of vertical skyrises. As cities become loaded with skyrises the rural zones continue to witness horizontal expansion. The construction of a high-rise is a challenge because it necessitates the requirement of immense resources in terms of specific building materials, construction equipment and efficient as well. Tall buildings can be thus be effectively used to meet the requirements of modern society and solve the problem of limitation of construction site resources. On the other hand, they are often seen as symbol of economic prosperity. Nowadays high-rise buildings rise higher and higher, with more and more complex and individual plan and elevation, such as multi-tower buildings.
Considering that a high-rise accommodates numerous families as also offices in case of mixed-use high-rise, it is extremely essential to carry out a thorough analysis and test to ensure it remains robust and sustainable. The designing of such projects also entails a big challenge because all the areas of the project should be easily accessible for commuting as also maintenance and emergency purposes.
Designing the right way
With increase in the use of high-rises, it makes sense in ensuring that they are designed well and fixed with the right kind of elevators. And these issues need to be addressed at the designing stage itself Deepak Mehta, Principal Architect, Deepak Mehta Architects says “Right from conceptual stage, the architect needs to dwell on positioning of elevator, zoning of the elevator and selecting the right elevator. The architect also needs to have a proper estimate or the traffic analysis as I like to call it of the entire building, so that a proper decision can be taken on the elevator to be used. These days architects and builders also utilize the services of an elevator consultant to make the right choice. Apart from the elevator, the design of the elevator lobby especially in projects is also important. In Mumbai I worked on a project which houses 275 offices, now consider if each office has an average of 25 employees what is the total head count, we are looking at. If the elevator lobby is not well designed all these people will feel claustrophobic.”
Test and Analyses
The different tests which are carried out before construction of a high-rise include FEM analyses, 3D volumetric construction, flat slabbing technology, Insulating concrete formwork. Especially in high-rise projects, a structural consultant carries out all these indispensable tests to ensure the feasibility and the safety of the structure. Apart from high-rises these test even extend to other areas of the built environment like bridges for example.
“With regards to the various tests & analysis that are required to be done,” says Prem Nath, Principal Architect, Prem Nath and Associates, “I as an architect, do not interfere with my team member, the structural consultant – I allow him to test the design with all aspects and simulations required – while I am confident that the architecture & form that I design for a particular high rise building is designed to be the best combination of flexible w.r.t. wind loads & seismic forces and yet rigid enough to take loads of the occupancy/use it is designed for.”
“FEM analysis and wind tunnel are not new methods,” says Ram Raheja, Director, S Raheja Realty “but they have been followed by ancient architectures. The only difference is it has gained value now. Other techniques like 3D volumetric construction, flat slabbing technology and insulating concrete formwork are also widely used. (a) 3D volumetric construction – In this technology modular, construction technology is used and 3D units are produced in controlled factory settings using needful construction and building materials. (b) Flat slabbing technology – This technology is used in contemporary framework for slabs to facilitate easy and swift placing of horizontal amenities and for partitioning. (c) Insulating concrete formwork – A building system that uses lightweight formwork (prepared from an insulating material) to support concrete walls whilst they are being cast insitu and which is then left in place as insulation.”
Project specific solutions
When it comes to tall structures standardised solutions may not deliver, in such situations it is necessary to dwell on project specific solutions. One example which can be cited here is of the tailor-made formwork and climbing solutions provided by PERI in construction of GIOIA 22, the 120 m tall tower at the heart of the Porta Nuova district which will cater to approximately 2,700 people have 350 parking spaces and 13 lifts.
The building consists of a main core with 26 floors and a secondary core with 13 floors. The special feature: from the second floor upwards, the tower starts to fold in on itself so that the slabs become wider with each passing floor. A project specific combination of different systems was required to create the unusual shape of the building. Moreover, the construction work had to be completed as quickly and efficiently as possible in order to meet tight deadlines. For these reasons, the decision was made to combine the SKYDECK Slab Formwork with an additional RCS P System Solution to realise the slabs from the second floor upwards. Systematic erection sequences and lightweight system components made it possible to complete an entire floor in a week.
Characteristic features of the building are the 17 round columns of which seven columns are inclined. They were erected using SRS Circular Column Formwork. With their high-quality, architectural concrete surfaces, the columns are also aesthetically pleasing. The diameter of the columns vary between 1.0 m and 0.8 m, becoming smaller with the increasing height of the tower.
The client used approximately 1,000 m² of TRIO Panel Formwork to erect the wall space in both cores. The TRIO System was combined with the BR Shaft Platform and the RCS C Rail Climbing Formwork to form the staircases and lift shafts. A particular highlight was the use of the ACS P Self-Climbing System. It allowed the lifting of the 32 m long concrete distribution arm from floor to floor.
It is safe to conclude that at the designing phase itself all the intricacies involved in designing a project should be noted. All the specific tests and the equipment that is needed should be categorically listed. It is extremely essential for the stakeholders involved in the construction of high-rise to communicate seamlessly. A perfect collaboration is destined to give good results and ensure the end product is safe, sustainable and brings joy across the faces of its occupants.
19
Cookie Consent
We use cookies to personalize your experience. By continuing to visit this website you agree to our Terms & Conditions, Privacy Policy and Cookie Policy.