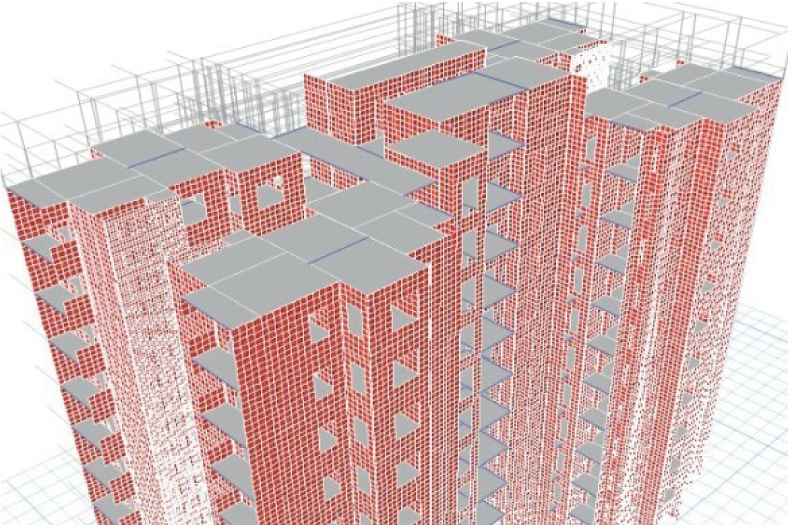
Nuclear Power Corporation of India Limited (NPCIL) at the Kudankulam Nuclear Power Plant located near Kanyakumari in Tamil Nadu has recently adopted precast technology for their housing need. This requirement originated from the recently approved additional reactors and the need to add additional manpower to operate the new reactors.
For this, NPCIL approached precast vendors for participating in the tender and bidding for the same. Teemage Precast was the successful bidder. The proposed building was an executive apartment (BUA / unit of 945 sq.ft) and was designed as stilt+10 floors with a central core of lift and staircase and four units in each floor. The total built-up- area was 55,400 sq.ft and the stipulated time of completion was one year as per the work order.
The process: Feasibility Study of the drawings as well as the site to understand adoption of
Precast and challenges for the same.
• Design development using the provided architectural layouts and elevations, understanding the usage of precast elements based on the capacity of the equipment.
• Manufacturing of precast elements at the factory and stocking.
• Transporting the elements as per the erection schedule and erecting the elements.
• Finishing activities included elevators.
• Flooring, electrical, plumbing, firefighting and painting etc.
The challenges in the process were mitigated using expertise at each level to make sure time and cost overruns are minimised. The production of 100 per cent of precast elements was completed within 120 days and the erection was completed within 150days. The two activities had a lag of 15 days and hence the structure was completed within a span of 180 days including the cast-in-site foundations. Currently in the finishing stage, Teemage Precast plans to handover the project within 10 months, thus saving two months from the schedule.
Precast design
Standard design with beams and columns were provided in the bid documents with the option of converting it to a shearwall structure. By converting it, Teemage was able to increase the carpet area vs built-up area percentage by 4 per cent. The details of precast elements are as below.
¢160mm Precast Concrete Shearwalls for Vertical Elements
°90mm Precast slab + 60mm CIS screed for Floor and Roof Slabs
¢160mm Precast Pergolas and Parapets. *Cast-in-Situ footing with pedestals for the Sub-Structure.
ETABS Models were created for different schemes and the most structurally efficient scheme was adopted and proof-checked at IIT Madras and the representatives from NPCIL. Various softwares and in-house design spreadsheets were used for element design and connection design in line with the Indian Standards Codal Provisions as well as International Standards for Precast.
Conclusion
The precast solutions provider will need to constantly thrive to address the challenges through its modified polices/methodologies in varied dimensions, with the objective to make the project profitable, both to the company and the end user. One such action is the complete integration of all the precast construction activities right from planning to erection cum finishing at site, with specially trained, dedicated in- house team for each of the activities, involved in a typical precast project cycle. This greatly helps in reducing the project cost which in-turn makes precast affordable housing, an achievable target.
Realising the potential of mass housing and its thin profit margin; geographical distribution all over the country, the company also needs to become specialised in establishing site factories in order to reduce its transportation, handling and other hidden costs thereby making precast, a viable option in realising the EWS and LIG housing project at much needed speed and quality, in the prevailing market cost itself. Due to the fact that a precast project becomes cheaper if there is more repetition in elements, a typical mass housing project can be readily completed within the price of ` 6-7 lakhs per housing unit, having a plinth area of about 375-400 sq.ft. Hence, it is very much possible to achieve the LIG housing projects even without Government subsidy on housing loan interest under PMAY scheme.
As a conclusive remark, it is very much possible to address the present problem of widespread disparity between the house hold income and unit price of a house and hence the widening of gap between demand and supply in the affordable housing sector, through the adoption of latest construction methodologies and precast is one such technology which can be relied upon taking account of its inherent advantage of factory quality control in housing element production, reduced project time thereby helping oneself to overcome fluctuating construction cost and most importantly, the predetermined reduced cost with no further cost over run in the complete project flow path.
About Teemage Precast
Teemage Precast In is a technological solution provider to the construction industry. They have developed a path breaking solution for the construction industry to build faster, better. They are one of the leading companies in India to employ state-of-the-art precast technology for more than 150 projects with a built-up area of 50 Lakh Sq.ft.
The journey in precast started in 2012 with captive consumption requirements of the parent company, “The Chennai Silks”, the largest textile kingdom in Tamil Nadu and now a conglomerate with diverse business interests in many verticals. Currently, their corporate office is located in Tirupur which houses the sales, marketing, design and project controls team and operate four precast concrete manufacturing facilities across India (Coimbatore, Delhi, Hyderabad and Chennai) with a cumulative production capacity of 2000 tonnes of precast concrete per day and an equally strong logistics and site teams to ensure total solution to all the clients for their building needs.
They are committed to the research and development of innovative product lines that expand the versatility of precast concrete and its pivotal role in the construction industry.
29
Cookie Consent
We use cookies to personalize your experience. By continuing to visit this website you agree to our Terms & Conditions, Privacy Policy and Cookie Policy.