3D Printing and BIM: Shaping the future of innovation in Indian construction
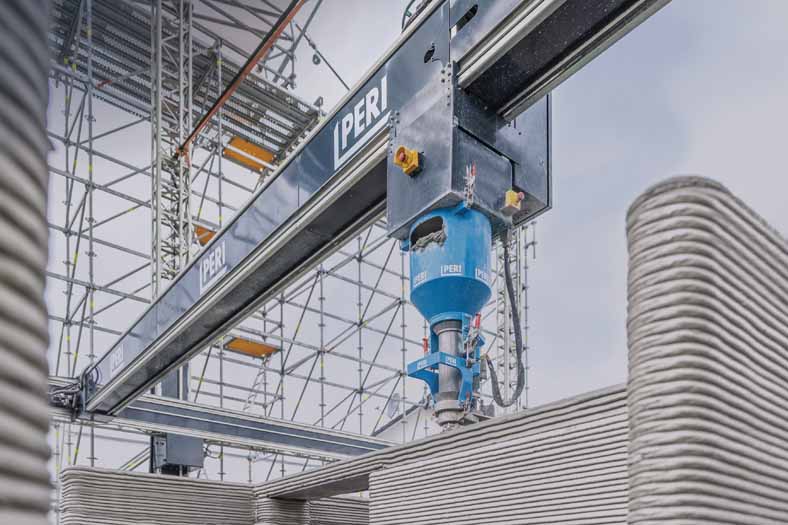
In an age when the use of technology has enabled innovations previously thought impossible, the construction sector too is witnessing this magic. Thanks to 3D printing and BIM!
In a timeline when every sector is getting revamped, thanks to technology, the construction sector too has witnessed a good degree of innovation. Some of these can be utilized across different projects, then there are some which are pretty project specific. The innovation is also being driven by the fact that the construction sector needs to inch closer to an ecosystem which is truly sustainable. Apart from technology design too is a driving force in this endgame.
Tushar Srivastava. President/Head – BD & Marketing, Capacit’e Infraprojects Ltd points out “In metro cities where vertical growth is the only feasible option any technology being utilized right from the equipment to formwork will fall under the ambit of sustainable development. Sustainable development would depend on the attempt being made at reducing carbon emissions. So to a good degree it depends on numerous factors including the quantity of steel reinforcement in the structure being used, likewise there is also a need to moderate the use of cement. Afterall steel and cement account for a huge amount of CO2 emissions. Innovations may be driven by technology but when it comes to ensuring that the construction practices are sustainable, I like to believe more than technology, the use of material has a great role to play.
The impact of concrete, one of chief construction materials on the environment, has been noted and scientists are consistently working towards looking for a feasible solution. Manu Santhanam, Professor, Department of Civil Engineering, IIT Madras says “While concrete is still the primary building material, current efforts are towards reducing the extent of cement usage in concrete, in order to lower the net CO2 impact of concrete. The increased level of understanding of supplementary cementing materials such as fly ash, slag, calcined clay has paved the way for more innovative cementitious binder systems that can impart high durability to the concrete. Advances in nano materials have also contributed to producing niche concretes such as self-cleaning concrete (which is made possible by TiO2), and conductive concrete (which has carbon nanofibers / carbon nanotubes to provide conductance, and also improve the resistance to microcracking). Also, the use of fibers (mainly steel, but sometimes also glass and polypropylene) intermixed into the concrete has made it possible to produce thin and slender concrete sections.”
In a universe where algorithms are becoming a driving force for numerous manufacturing processes, in construction too a similar trend is being witnessed via 3D printing. M V Satish, Whole Time Director & Senior Executive Vice President (Buildings), Larsen and Tubro points out “3D Printing has gained considerable traction over the past few years as has 3D Concrete printing that are being well researched globally. Across continents, several global players have successfully 3D printed concrete buildings in the recent past. 3D printing technology almost eliminates the need for formwork systems and thereby helps avoid related costs. However, the cost of special ingredients used in the concrete printing is currently high, as is the cost of the printer. As is the case with any new technology, once a certain critical mass is achieved, the costs will reduce substantially, and the technology will become cheaper than conventional ones, and of course more efficient.” Pointing out the challenges involved in this innovation he adds “3D printing technology is currently only suitable for low rise building construction due to the printing height restrictions imposed by the concrete printers. However, with ongoing research in this area, we expect that this constraint will soon be overcome, with improvised printer design and innovative printing methodology. There have been certain challenges in embedding reinforcement in 3D Concrete Printing, which L&T Construction has overcome with innovative construction design and methodology.”
3D printing can play an important role in government initiatives like “Housing for All”. Adithya VS – CEO & Co-founder of Tvasta says “Concrete Printing came into existence to cater to the ongoing housing crisis all around the world. This rapid construction method reduces labour dependency, controls the amount of material wastage, and promotes a more organised manner of construction that promotes shorter lead time. These perks remove all possible last minute construction errors that significantly reduce the cost of the end product of building affordable houses. Large scale adoption of this technology is likely to happen by 2024. There is a lot of research going on to increase the affordability for the common sector applications.”
Like 3D printing even Building Information Modeling (BIM) has made quite an impact on the way construction is executed, its impact especially in the precast segment has been quite profound. Nirmal Mangal, India Director – Architecture, M Moser Associates elucidates “Precast manufacturers are using BIM to convert models received from architects into precast components. The precast team details it to create an inclusive model that other trades can use for clash detection and incorporation of other services. Such collaboration minimizes site changes and design compromises.More efficient project schedule aligned with construction sequence – On larger projects, the precast manufacturers are collaborating with the architect and construction managers to help define and optimize the project schedule and construction sequence. Since the construction sequence of precast concrete buildings is different, early planning of project schedule and sequence is important to best optimize the project schedule.”
“BIM is particularly beneficial in the planning phase of modular construction,” adds Paul Wallett, Regional Director, Middle East and India, Trimble Solutions “This is because with modular construction, there’s not much room for error, and the design needs to be agreed upon early in the process. For example, when working within a limited space, the high level of detail in a BIM model prevents costly miscalculations. It further allows project parties to collaborate remotely without interruptions and even work in the same 3D model at the same time to ensure a clash-free final design. This in turn allows them to plan and manage projects together in as detailed a way as necessary. Modular construction uses 67% less energy than the conventional techniques of construction, and upto 50% less time is spent onsite. Thanks to BIM software, which makes it easy for designers to make changes and corrections before transporting materials. Small mistakes onsite can lead to wastage of tons of materials, and even correct materials are vulnerable to rot and damage in harsh weather. But modular construction has put a stop to this, resulting in a 90% reduction of project material waste.”
39
Cookie Consent
We use cookies to personalize your experience. By continuing to visit this website you agree to our Terms & Conditions, Privacy Policy and Cookie Policy.