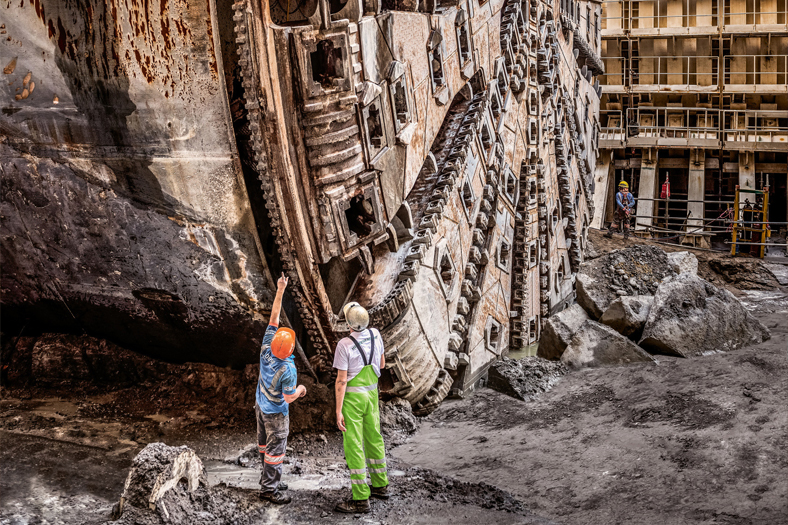
Manufacturers developing tunnelling equipment that support producing high-quality, safe and durable structures.
Tunnelling equipment manufacturers are developing tunnelling technology to produce safe, high quality and long-lasting tunnel structures even in new, highly complex terrain. Tunnel construction method depends on factors such as the ground conditions, ground water conditions, length and diameter of the tunnel drive, depth of tunnel, logistics of supporting tunnel excavation, final use and shape of tunnel and appropriate risk management.
Development of technologies
According to Herrenknecht AG, in the last years, new feasibility standards have been set in tunnel construction with projects like Eurasia tunnel, Istanbul. There, three challenges came together – at a large diameter of 13.66m, 11 bar of water pressure and in a demanding, mixed geology (fractured rock and soft ground – wear-intensive ground) the 3.34km long bore is unprecedented.
Launched from the Asian side, the underpass for the two-story Eurasia road tunnel was a huge endurance test for ultra-modern tunnelling technology. The large-format Mixshield tunnelled down to the deepest point 106 metres below the Bosphorus. There the water pressure was 11 bar. Combined with a quite changeable, wear-intensive underground, this places extreme demands on the giant cutting wheel’s excavation tools. This necessitated a range of different safety features that, trialed in previous undertakings and further developed for pioneering projects like this one. The particular challenge was to develop a cutting wheel that allows safe replacement of the excavation tools from the inside even with the huge external pressure, according to the company. This results in a cutting wheel accessible from the rear through narrow working chambers. The tools can thus be changed safely by the crew through special lock systems under atmospheric pressure conditions.
The diameters of the tunnels are increasing, so enabling two-story road tunnels or a road line on the upper deck and below a metro line. The largest TBM in the world was used in Hong Kong (Ø 17, 6m).
In highly variable ground, classic tunnel boring machines can reach their technical or economic limits with their specific method. Along one tunnel alignment can change largely. Multi-mode TBM is developed for such cases (also the Socatop TBM was a Multi-mode TBM). The basic concept makes it possible to change between slurry support, earth pressure support and open mode within one tunnel alignment, by undertaking a range of conversions. The Variable Density TBM combines the advantages of EPB and slurry-supported mode in one machine. There, without mechanical modification the machine can switch between different tunnelling modes. This means that geological and hydrogeological changes along the alignment can be managed with extreme flexibility – it’s like an ‘all-rounder for loose soils of all kinds’. Beside this, variable density concept provides additional possibilities for muck removal, which also might be an advantage depending on the project requirements.
Putzmeister has a range of solutions for tunnel constructions. The company’s traditional stationary concrete pumps been deployed in the construction metro projects such as London and Bengaluru metro. The high density solids pumps help transport spoils away from tunnelling sites to designated areas – during the construction of the Eurotunnel for example 8 Putzmeister high density solids pumps transported 8 million m3 of spoils in 90,000 operating hours.
“We have specially designed compact concrete spraying (shotcreting) equipment that has helped build roadway tunnels all over the world. In fact, for over 30 years, Putzmeister has been designing, developing and producing special equipment for tunnel construction including shotcrete batching plants and low-profile concrete mixers,” says Wilfried Theissen, Managing Director, Putzmeister India.
Emerging technologies
Formkret: automated formwork filling system
In collaboration with Kern Tunneltechnik, Putzmeister offers Formkret, an automated formwork filling system. It is regulated by a set of two-way valves integrated in the formwork structure and connected by a single delivery line that links the entire system in sequential rows. Formkret significantly reduces the overall number of operators needed onsite, increase safety and help deliver tunnel projects in a time-efficient manner, says Theissen.
Formwork installation time is shortened, as the structure can be easily placed and aligns itself to the tunnel’s geometry. The integrated concrete delivery time eliminates need for manual hose switching, reducing worksite hazards and making it safer. The structure is then connected to the pump, which can be operated remotely.
Eco-friendly installation of underground cables
Herrenknecht’s E-Power Pipe allows small diameter drives with ten times greater lengths, shallow depths as well as high precision and speed. This technology protects the environment through the innovative trenchless installation of underground cables and is cost-effective.
E-Power Pipe has purposefully modified and further developed proven drilling technologies so that underground cables can be installed trenchlessly and close to the surface at a depth of between 1.5 and four metres with minimal intervention in the landscape. The heart of the system is the fully remote controlled tunnel boring machine AVNS350XB, which has an excavation diameter of 505 millimetres and is designed for drive lengths of more than 1,000 metres. The machine can keep to the planned alignment with high precision and thus, cross safely under existing infrastructure such as pipelines, roads, railways or smaller bodies of water. Individual boreholes can be placed a small distance of only 1 – 2 m apart, so several lines can be installed in parallel.
The tunnelling machine is equipped with a jet pump and an integrated hydraulic power unit. With conventional methods, restrained inside space limited muck removal over longer sections and as a result also limited the possible drive lengths. Through the use of the jet pump for transporting the muck, up to 10 times longer tunnelling distances can be realised at high speeds in the small diameter range.
The installation of underground cables using the E-Power Pipe method is a ground-conserving alternative to the conventional open-cut method. Due to the trenchless installation method, earth movements are reduced to the places where HVDC cables have to be connected later. This can mean a reduction of about 90 per cent in relation to the entire alignment. Installation takes place without any environmental impact over long distances, since the surfaces and the soil structure are left largely untouched. The use of construction machinery and trucks is also significantly reduced in this way, as are noise and emissions.
Putzmeister has been designing, developing and producing special equipment for tunnel construction including shotcrete batching plants and low-profile concrete mixers.
Wilfried Theissen, Managing Director, Putzmeister India
18
Cookie Consent
We use cookies to personalize your experience. By continuing to visit this website you agree to our Terms & Conditions, Privacy Policy and Cookie Policy.