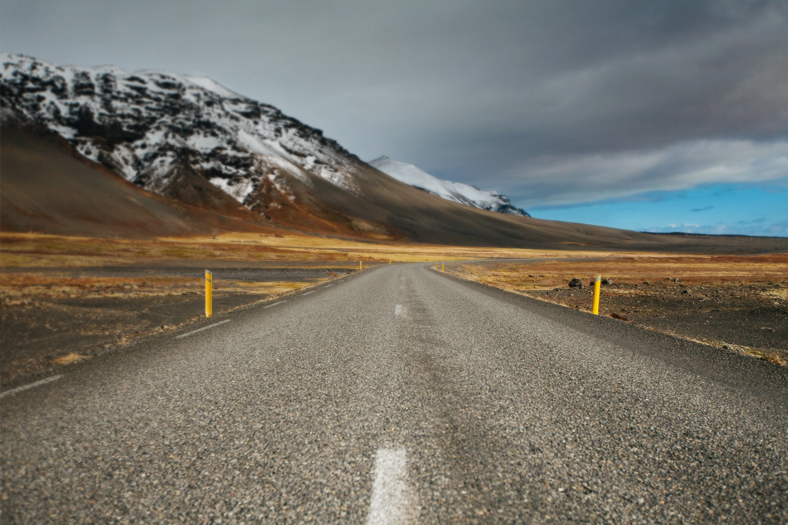
For higher quality of concrete, taking precautions while choosing the raw material is crucial for sustainable road building.
High quality concrete is essential for road construction as roads are dedicatedly used for heavy and light vehicular movement. The quality of concrete is achieved by attending following precautions. The raw material used for quality concrete i.e. sand and aggregates are must
The most important role to achieve good quality of concrete mixing which is attended by ready-mix concrete. Mixing plays an important role in achieving the quality of concrete, says Girish Bothra, Director, Reackon Concretes Pvt Ltd.
Use of plastisizer (admixture), to maintain the workability and limited quantity of water to achieve W/C ratio. Use of fly ash with OPC cement to reduce the heat of hydration and enhance the durability of concrete. As roads are affected due to abrasion, to avoid abrasion better to use fibre in concrete. While laying it is must to use needle and surface vibrator to make concrete dense. By these all factors we will definitely achieve the high quality concrete.
Rubber mould pavers are better option
Paver is good option for roads projects. Paver is manufactured by compacting technology by hydraulic press and rubber molded vibro technology. Pavers manufactured by rubber moulds are better option than compaction technology with hydraulic pavers. As rubber mould pavers is manufactured by concrete having high cement content, according to Bothra.
Improves quality and safety
Forest Press has successfully delivered multiple plants and equipment for infrastructure products for road, railway, sea, and aviation projects. Transportation engineering and highway planning in India is progressing on faster pace, this time with more streamlined approach, where safety, energy efficiency and the importance of pavement to cope with the movement of commercial vehicles.
“Our equipment like block master, concrete batching system and wet press system are ideal solution for enhancing the safety and durability of the projects, reducing the maintenance and operational cost. Our block master produces Vibro cast eco-friendly paved road and wet press machine produce hydraulically-pressed kerb and water drain cover or dish channel,” says Manoj Kumar Pillai, Managing Director, Forest Press Machineries Pvt Ltd.
In Block Master, high volume production with high strength can be achieved in quicker production cycle of less than 20 sec. Consistent quality as the pavers are produced in controlled conditions, with proper concrete mix. Lastly, pavers and water drain channel allows to maintain the water table balance in our eco system.
More compacted and compressed concrete
Wet press machines are designed with 400-tonne hydraulic press, offering more compacted and compressed concrete. Hydraulically pressed kerbs are accepted in many economies for their sturdy performance as they withstand extreme climatic variations like, heat, freeze and thaw resistance and lasts for decades. Dimensionally accurate kerbs acts as to guide the road users and enhances safety.
Cutting-edge technologies
With the tailwinds of demand blowing in favour of concreting segment especially with a strong emphasis on indigenisation, AJAX has strategically aligned its product portfolio in line with the Indian government’s ‘Make in India, Sell Global’ programme by indigenising its product portfolio offering state-of-the-art machines equipped with top-class technology manufactured at its Bangalore plant for the complete bandwidth of construction infrastructure segments.
“AJAX’s prime focus is onto the cutting-edge features providing product accuracy and reliability in terms of technological advancement in our concreting machines to remain competitive enough by continuing to be a market leader by always a competitive advantage with product differentiation in the business thereby side-lining the substitute products,”says Debasis Bhattacharya, Head – Marketing, Sales & Product Support, Ajax Fiori Engineering India Pvt Ltd.
Wide range of products
From mixing and batching to automatic cubing and splitting, Columbia builds a complete line of equipment to outfit entire concrete products plant. The Model SPM20 which is for Indian market can be used to produce a wide range of high quality concrete products such as hollow blocks, paver blocks, retaining wall blocks, flyash bricks and kerbstones, says Ramesh Babbar, President & Director, Columbia Machine Engineering (I) Pvt Ltd.
The company has made several design changes in its flagship product SPM20 and also launched new and fully automatic Concrete Block Machine SPM30 last year. The Model SPM30 machine is provided with a unique Rack Loader /Unloader Model UL30 made in India with technology from Columbia Machine, USA. UL 30 provides completely automatic loading and unloading the production pallets in to the racks.
Further, cured products are automatically cubed on wooden pallets using the Plate Style Cuber PSC 200 again made in India with technology provided by Columbia Machine USA. This increases Pallet and product handing efficiency and improves productivity as well as reduces product handling damages drastically.
Long service life, low maintenance cycles
“Our products like RDC Supercrete, RDC Expresscrete, RDC Selfcrete creates value for our clients and saves time. Also, products like RDC Greencrete, RDC Toughcrete, RDC Fibrecrete and RDC Corrodresistcrete helps in construction of structure with a long service life and low maintenance cycles and cost,” says Anil Banchhor, MD and CEO, RDC Concrete (India) Pvt Ltd.
These products help in reducing wastages, lower carbon footprint and paves path for a sustainable future. Products like RDC Imprecrete and RDC Selfcrete addresses aesthetic requirement in today’s needs where aesthetic have become a prerequisite.
Mixing plays an important role in achieving the quality of concrete.
Girish Bothra, Director, Reackon Concretes Pvt Ltd
Our equipment are ideal solution for enhancing safety and durability of projects.
Manoj Kumar Pillai, Managing Director, Forest Press Machineries Pvt Ltd
Prime focus is on cutting-edge features providing product accuracy and reliability in terms of technological advancement.
Debasis Bhattacharya, Head – Marketing, Sales & Product Support, Ajax Fiori Engineering India Pvt Ltd
From mixing and batching to automatic cubing and splitting, our equipment outfit entire concrete products plant.
Ramesh Babbar, President & Director, Columbia Machine Engineering (I) Pvt Ltd
RDC Supercrete, RDC Expresscrete, RDC Selfcrete create value for our clients and save time.
Anil Banchhor, MD and CEO, RDC Concrete (India) Pvt Ltd
21
Cookie Consent
We use cookies to personalize your experience. By continuing to visit this website you agree to our Terms & Conditions, Privacy Policy and Cookie Policy.