Waterproofing the Motera: The worlds largest cricket stadium
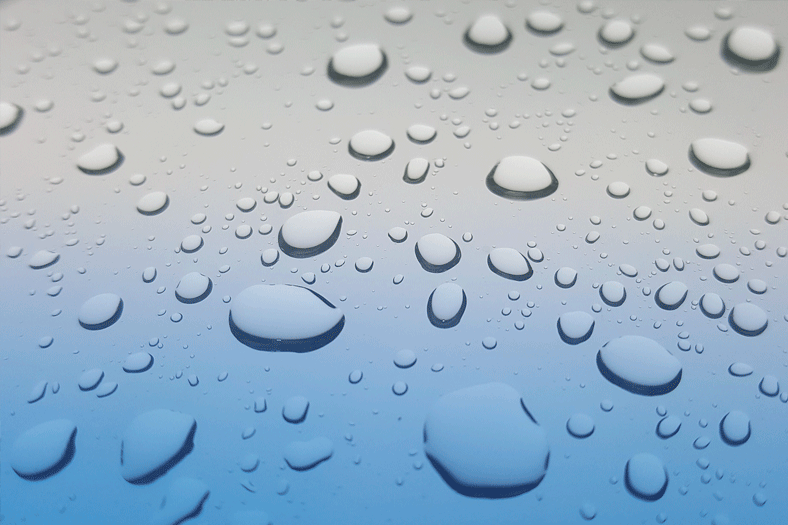
Motera Stadium – elevating cricket to a global sport
Ranked among the “Top 5 waterproofing brands of India”,Sunanda Global had the honour and privilege of providing end to end waterproofing systems for the Sardar Patel Stadium or Motera Stadium in 2019.
With a reported seating capacity of over 1.10 lakh, the stadium is the pride of the nation and the largest cricket stadium in the world. Prior to Motera stadium the largest stadium in India was Eden Gardens, which can host up to 66,349 people. Motera Stadium is built across 63 acres of land, has three practice pitches, an Olympic-size swimming pool, four dressing rooms, a clubhouse with 55 rooms, 76 corporate boxes, and an indoor cricket academy.The parking area is built to accommodate nearly 3,000 cars and 10,000 two-wheelers. It has been designed by renowned architect firm Populous, and the construction company was Larsen & Toubro.
The project, as conceived by Honourable Prime Minister NarendraModi was ambitious in both its magnitude and the very aggressive timelines. The entire design and construction was completed in a record time of 3 years. As a result, every aspect of design and construction of the project required innovation, challenging the status quo and executing with speed, determination and accuracy.
While posing a major waterproofing challenge, the decision to adopt precast technology was the game changer in being able to deliver the project in such a short construction time. For example, cast in situ columns would have put the time line at over 7 years as the design involved 43 Y shaped columns which would have required two months each. However, by switching to pre-cast technology, the timeline was much reduced with columns gaining the required strengths in 10-12 days. To put the scale of the project in perspective, some statistics are listed below:
Concrete in situ – 66,000 cu.m,
Concreting (Precast) – 34,000 cu.m.
Precast elements – 6,600 nos
Reinforcement – 14,000 metric tons
Masonry – 16,000 cu.m.
Plastering – 1,48,000sq.m.
Flooring – 51,000 sq.m.
Assessment of Project Conditions
India’s four month long annual monsoon rains present unforgiving conditions for a structure to endure. This is compounded by the extreme temperature gradient encountered in Ahmedabad with cold winters where night time temperatures drop to low single digits (Celsius) and hot and oppressive summers where peak day time temperatures can go to the high forties (Celsius) and sometimes even break the fifty mark. As a result adopting conventional waterproofing methods, materials, technologies and specifications have led to disastrous consequences in several high profile construction projects.
Add to this the challenge presented by pre-cast construction with respect to waterproofing. However, with forty years of global experience Sunanda’s team has several veterans of pre-cast waterproofing.
We quickly put together an internal task force which was led by the group’s Ahmedabad regional headquarters with senior members representing the R&D and technology development from the innovation centre and corporate headquarters in Mumbai giving their inputs as associate members of the task force. This cross functional, experienced and diverse team was entrusted the task of delivering a leakage proof waterproofing solution to the Motera stadium.
Given the nature of the construction and precast elements, the selection of waterproofing system, design, implementation and execution of fool-proof waterproofing specifications and on-job quality assurance assume paramount importance. Post a detailed inspection, identification of weak spots, the custom methodology in keeping with client’s waterproofing requirement and specification was recommended, approved by the project management consultant M/s Stup and client GCA. Post approval of the product and methodology, the end to end waterproofing was executed by the Sunanda’s team under the umbrella of main civil contractors Larsen & Toubro.
Selection of Waterproofing Technology
ELASTOROOF PUTM manufactured by Sunanda Global is a single component, high build, liquid applied polyurethane chemistry was adopted as the technology of choice for the waterproofing coating system. This material chemistry offers significant benefits in the case of fast track, mega projects such as Motera stadium due the stellar performance and track-record of the material in achieving 100% waterproofing in the most trying conditions.
Due to their high mechanical properties, elongation and flexibility, particularly at lower temperatures, as well their capability to cure under a wide range of conditions, ELASTOROOF PUTM polyurethane based liquid applied membranes can also be used in a diverse range of climatically challenging environments. Ahmedabad has extreme temperatures with cold winters and oppressively hot and dry summers. This high temperature gradient tests the limits of most waterproofing membranes and materials due to the thermal stresses.
Unlike other waterproofing systems like sheet membranes and acrylic/cementitious liquid applied membranes, this ELASTOROOF PUTM polyurethane application requires comparatively less skill and supervision.
As being a liquid applied membranes, ELASTOROOF PUTM cures to a joint free barrier membrane which is especially important in case of large spans/slabs/areas and pre-cast construction projects.
Application is fast and curing of the ELASTOROOF PUTM membrane is also quite rapid making the system rain resistant almost immediately after application.
Further the rapidity of the curing reaction enables for speedy overcoating and further laying of the protective course.
Single component chemistry saves time and eliminates the risk of mixing errors and make the product easy to use.
The entire waterproofing of the podium and stadium areas was executed in a record time using a combination of the innovations in material science, chemistry and mechanization of the surface preparation, pre-treatment, application of waterproofing materials. An end to end emphasis on quality control and testing at every step of the process were critical in ensuring that the desired performance and speed was achieved and the project was handed over in time.
Ducts, cutouts and wet areas were used using composite systems of grouting with POLYEXPANSETM non-shrink grouts, SUNEPOXY 358TM epoxy compounds and ELASTOROOF PUTM as described above.
Planning, Execution and Application
Planning and sequencing a project of this magnitude is a skillset that is unique to very few companies in India. No stranger to mega projects, strict performance requirements and aggressive timelines, Sunanda’s indigenous large manufacturing capacity allowed us to deliver massive quantities of product in a very compressed timeline a feat few other companies have managed, especially on complex products like single component polyurethanes. Product conforming to international standards manufactured under the “MAKE IN INDIA” banner is a matter of pride for the nation.
Maximum utilization of mechanical application methods like floor polishing machines, grinding machines, airless spray equipment for membrane application and a much reduced dependence on manual application were also critical technology inputs in enabling the waterproofing to be completed in a timely fashion. Planning for disruptions, spares, several site related unforeseen circumstances requires experience, expertise and a hands on approach to job completion.
Authored By:
Ishita Manjarekar, Technical Director, Sunanda Global
Saurabh Manjarekar, Director (Operations), Sunanda Global
Cookie Consent
We use cookies to personalize your experience. By continuing to visit this website you agree to our Terms & Conditions, Privacy Policy and Cookie Policy.